Understanding Wafer Level Reliability for Enhanced Device Performance
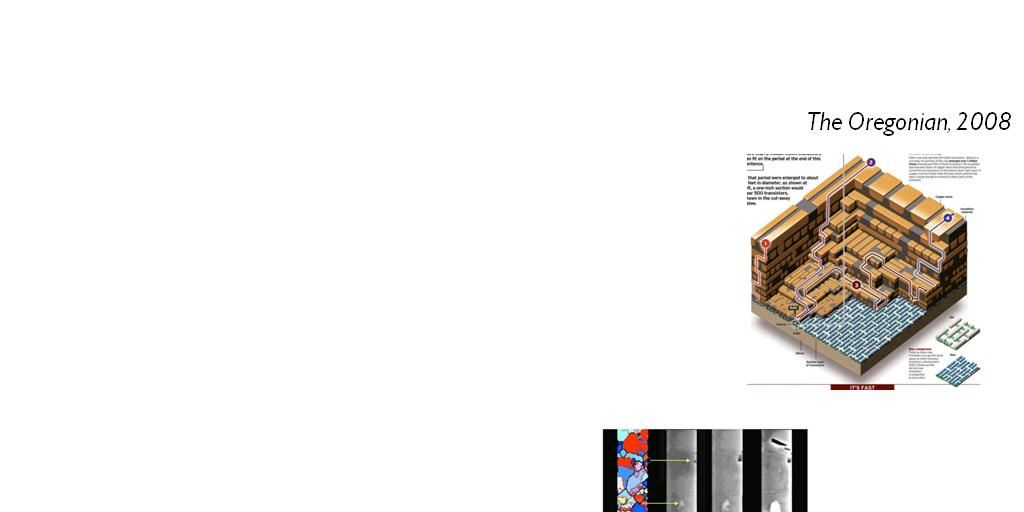
Wafer level reliability (WLR) testing is a crucial part of making sure that semiconductor devices work well and last a long time. As technology gets better and chips get more complicated, engineers need better ways to test reliability without spending too much money. This article will explain why WLR testing is important, how it’s done, the challenges faced, the new tools being used, and what the future holds.
Key Takeaways
- WLR testing helps improve production efficiency and monitor processes in semiconductor manufacturing.
- Using WLR testing can lead to better performance of integrated circuits (ICs).
- New techniques in WLR testing provide faster feedback and more flexible solutions.
- There are challenges in WLR testing, such as scalability and cost, but new tools are helping to overcome these.
- The future of WLR testing looks promising with advancements in design scales, materials, and testing methods.
Importance of Wafer Level Reliability in Semiconductor Manufacturing
Impact on Production Efficiency
Wafer level reliability (WLR) testing is crucial for improving production efficiency in semiconductor manufacturing. By monitoring thousands of parameters, fabs can quickly identify and address issues, leading to smoother and faster production processes. This proactive approach helps in minimizing downtime and maximizing output.
Role in Process Monitoring
WLR testing plays a significant role in process monitoring. It provides real-time feedback on the reliability of semiconductor devices, allowing manufacturers to make data-driven decisions. This continuous monitoring ensures that any variations in materials or processes are detected early, preventing potential failures.
Benefits for IC Performance
The benefits of WLR testing extend to the performance of integrated circuits (ICs). By ensuring the reliability of each wafer, manufacturers can produce high-performance ICs that meet stringent quality standards. This not only enhances the overall performance of the devices but also increases their lifespan, making them more reliable for end-users.
Key Techniques in Wafer Level Reliability Testing
Fast Feedback Process Control
Wafer Level Reliability (WLR) tests are crucial for providing quick feedback on process control. These tests help measure the variation in materials that make up semiconductor devices. Fast feedback is essential for maintaining the reliability of the product during the semiconductor process. By identifying issues early, manufacturers can make necessary adjustments to improve overall production efficiency.
Parallel Per Pin Approach
As technology advances, the complexity of semiconductor devices increases. This complexity requires more parameters to be monitored and controlled. A parallel per pin approach is necessary to address both channel count and flexibility. This method allows for simultaneous testing of multiple pins, which helps in managing the increased demands from new technology trends and chip complexity.
Modular Testing Solutions
Modular testing solutions offer a flexible and scalable approach to WLR testing. These solutions can be easily adapted to different testing requirements, making them ideal for various stages of semiconductor manufacturing. By using modular components, manufacturers can customize their testing setups to meet specific needs, ensuring that they can keep up with the evolving demands of the industry.
Challenges in Implementing Wafer Level Reliability Tests
Scalability Issues
As semiconductor devices get smaller and more complex, the number of parameters that need monitoring increases. This makes it hard to scale traditional testing methods. Engineers face the challenge of managing more data without extending test times. Highly parallel and modular solutions are needed to keep up with these demands.
Cost Implications
Wafer level reliability tests can be expensive. The cost of equipment and the need for highly skilled personnel add up. As technology advances, the cost of testing is expected to rise. Finding ways to reduce these costs while maintaining test quality is crucial.
Technological Limitations
Current testing methods have their limits. They may not be able to keep up with new materials and evolving design scales. This can lead to incomplete or inaccurate data. Engineers must look for new tools and methods to overcome these limitations.
Advancements in Wafer Level Reliability Tools
As semiconductor devices get smaller and more complex, the need for better wafer level reliability tools has grown. New reliability test tools are now faster, more sensitive, and highly flexible. These tools help engineers meet the increased demands from new technology trends and chip complexity.
New Reliability Test Tools
The latest tools are designed to provide quick feedback on process control. They measure variations in the materials that make up semiconductor devices. This helps in making data-driven decisions for process improvements.
Software-Connected Solutions
Modern tools are often connected to software systems. This connection allows for real-time data analysis and quicker adjustments. It also helps in reducing the overall cost of testing.
Enhanced Sensitivity and Flexibility
Today’s tools are not only faster but also more sensitive. They can detect even the smallest defects, making them highly reliable. The flexibility of these tools means they can be used in various stages of production, from R&D to mass production.
Applications of Wafer Level Reliability Testing
R&D Process Integration
Wafer level reliability (WLR) testing is crucial in research and development (R&D) for integrating new processes. It helps engineers quickly identify and address potential issues before they escalate. This proactive approach ensures that new technologies are robust and reliable from the outset.
Mass Production Monitoring
In mass production, WLR testing plays a vital role in monitoring the consistency and quality of semiconductor devices. By testing wafers directly from the production line, manufacturers can detect and correct defects early, reducing waste and improving yield. This leads to more efficient production and higher-quality products.
Material Variation Measurement
WLR testing is also used to measure variations in the materials used in semiconductor devices. This is important for understanding how different materials behave under various conditions, which can impact the performance and reliability of the final product. By identifying these variations, manufacturers can make informed decisions about material selection and process adjustments.
Future Trends in Wafer Level Reliability
As semiconductor devices continue to shrink and become more complex, wafer level reliability testing is becoming increasingly important. This trend is driven by the need to ensure that these tiny, intricate devices perform reliably over their expected lifetimes. Here are some key trends shaping the future of wafer level reliability.
Evolving Design Scales
The ongoing reduction in the size of semiconductor devices, known as evolving design scales, is a major trend. As devices get smaller, the challenges associated with ensuring their reliability grow. This necessitates more advanced testing methods to catch potential issues early in the design process.
New Material Adoption
Another significant trend is the development of novel materials for wafer manufacturing. While silicon remains the dominant material, there is growing interest in using other materials that can offer better performance or lower costs. These new materials require different testing approaches to ensure they meet reliability standards.
Upstream Testing Demands
The demand for reliability testing is moving further upstream, especially into the R&D process. This shift allows engineers to identify and address potential reliability issues earlier in the development cycle, which can save time and reduce costs in the long run. Instrument manufacturers are responding with new tools that are faster, more sensitive, and highly flexible to meet these demands.
Case Studies on Wafer Level Reliability
SOI Wafer Bonding Defects
In the realm of Silicon-On-Insulator (SOI) technology, wafer bonding defects can significantly impact device performance. Identifying these defects early in the manufacturing process is crucial. Wafer level reliability tests help in detecting bonding issues, ensuring that only high-quality wafers proceed to the next production stage.
MEMS Hermeticity Testing
Micro-Electro-Mechanical Systems (MEMS) require airtight seals to function correctly. Hermeticity testing at the wafer level ensures that these tiny devices are free from leaks. This testing is vital for applications where even a small leak can lead to device failure.
Integrated Circuit Mass Production
For integrated circuits (ICs), mass production demands consistent quality and reliability. Wafer level reliability tests provide fast feedback on process variations, helping to maintain high standards. This approach is essential for meeting the rigorous demands of modern electronics manufacturing.
Conclusion
In conclusion, wafer level reliability (WLR) testing is essential for ensuring the performance and longevity of semiconductor devices. As technology advances and devices become more complex, the need for efficient and cost-effective testing methods grows. WLR testing provides valuable data that helps manufacturers improve their processes and produce high-quality, reliable integrated circuits. By adopting new, highly parallel, and flexible testing solutions, the industry can meet the increasing demands for reliability while keeping costs down. This approach not only speeds up production but also ensures that devices meet the high standards required for today’s applications.
Frequently Asked Questions
What is wafer level reliability testing?
Wafer level reliability (WLR) testing checks the quality and durability of semiconductor wafers before they are made into chips. It helps find problems early, saving time and money.
Why is wafer level reliability important in semiconductor manufacturing?
WLR is crucial because it helps ensure that the devices made from the wafers will work well and last long. It also helps manufacturers spot and fix issues early, improving efficiency and performance.
What are the key techniques used in wafer level reliability testing?
Some main techniques include fast feedback process control, parallel per pin approach, and modular testing solutions. These methods help in quickly identifying and addressing reliability issues.
What challenges are faced in implementing wafer level reliability tests?
Some challenges include scalability issues, high costs, and technological limitations. These can make it hard to implement WLR tests effectively.
How have tools for wafer level reliability testing advanced?
New tools are faster, more sensitive, and highly flexible. They also often come with software-connected solutions that make testing quicker and more efficient.
Where is wafer level reliability testing applied?
WLR testing is used in research and development, mass production monitoring, and measuring material variations. It helps ensure that products are reliable at every stage of manufacturing.