Understanding Wafer Processing in the Semiconductor Industry
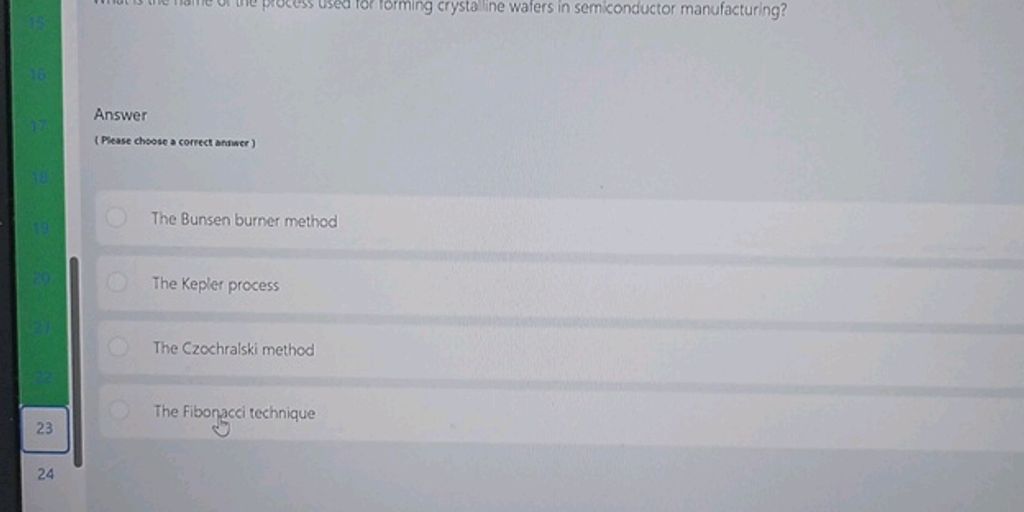
In the world of semiconductors, wafer processing is a crucial step in creating the tiny chips that power our devices. This process is divided into two main parts: front-end and back-end. Front-end processing involves turning a blank wafer into a complete one with microchips, while back-end processing prepares these chips for use by cutting, packaging, and testing them. Understanding these steps is key to grasping how our modern electronics are made.
Key Takeaways
- Wafer processing is divided into front-end and back-end stages.
- Front-end processing includes techniques like photolithography, chemical vapor deposition, and ion implantation.
- Back-end processing involves wafer dicing, packaging, and quality assurance testing.
- Wafer cleaning is essential throughout the semiconductor manufacturing process.
- Advanced techniques like chemical-mechanical planarization and wafer thinning are crucial for modern semiconductor devices.
Front-End Wafer Processing Techniques
Front-end wafer processing is the initial phase in semiconductor manufacturing, where microchips are created on a blank wafer. This stage involves several meticulous and controlled steps to ensure the precision and functionality of the final product.
Back-End Wafer Processing and Assembly
Wafer Dicing and Die Preparation
In the back-end process, the wafer is divided into individual chips through a method called dicing. This step is crucial as it prepares the chips for further assembly. Precision is key to ensure that each chip is cut accurately without damage.
Packaging and Encapsulation
Once the chips are diced, they are connected to a metal frame using metal wires, a process known as wire bonding. Afterward, the chips are enclosed in a protective material, usually epoxy resin, to shield them from moisture and physical harm. This step is essential for the durability and reliability of the final product.
Testing and Quality Assurance
The final stage involves rigorous testing to ensure each chip functions correctly. Quality assurance processes are implemented to detect any defects. Only the chips that pass these stringent tests are deemed ready for market. This ensures that the end products meet high standards of performance and reliability.
The Role of Wafer Cleaning in Semiconductor Manufacturing
Wafer cleaning is a crucial step in semiconductor manufacturing. It ensures that any leftover particles or contaminants are removed, which could otherwise disrupt the manufacturing process. This is achieved through a series of chemical baths and rinse cycles.
Pre-Cleaning Procedures
Before the main cleaning process begins, wafers undergo pre-cleaning to eliminate larger particles and organic residues. This step is essential to prepare the wafer for more thorough cleaning stages.
Chemical Cleaning Solutions
Chemical agents are used to remove all types of contamination, from ultra-fine particles to tiny amounts of organic or metallic residues. These agents are effective in ensuring the wafer surface is pristine.
Post-Cleaning Inspection
After cleaning, wafers are inspected to ensure no contaminants remain. This step is vital for maintaining the quality and functionality of the semiconductor devices. Even slight contamination can cause defects in the circuit, making this inspection a critical part of the process.
Chemical-Mechanical Planarization (CMP) in Wafer Processing
Chemical-Mechanical Planarization (CMP) is a crucial step in wafer processing. It involves polishing the wafer’s surface using a mixture of chemicals and abrasive particles. This process ensures the wafer is flat and smooth, which is essential for the next steps in semiconductor manufacturing. CMP is used multiple times during the front-end manufacturing process.
Advanced Techniques in Wafer Thinning
Mechanical Grinding Methods
Mechanical grinding is a common method used to thin wafers. This process involves using a diamond saw to slice the wafer into thin pieces. The wafer is then polished to create a smooth, flat surface. This step is crucial for the subsequent processes of semiconductor manufacturing. Mechanical grinding is efficient and cost-effective, making it a popular choice in the industry.
Chemical Etching Techniques
Chemical etching is another method used to thin wafers. This technique involves using chemical solutions to remove layers from the wafer. The process is highly controlled and can achieve very thin wafers. Chemical etching is often used in combination with mechanical grinding to achieve the desired wafer thickness.
Applications of Thinned Wafers
Thinned wafers have a variety of applications in the semiconductor industry. They are used in the production of microchips, sensors, and other electronic devices. Thinned wafers are also essential for advanced packaging techniques, such as 3D stacking. WaferPro’s industry-leading thinning processes are pushing the limits of silicon wafer thinness, enabling the production of smaller and more efficient devices.
Photolithography: The Heart of Wafer Processing
Photolithography is a key step in transferring circuit designs onto wafers. It starts with coating the wafer with a light-sensitive material called photoresist. A mask, which acts like a stencil of the circuit design, is then placed over the wafer. Ultraviolet light is shone onto it, hardening the photoresist in the pattern of the circuit design, while the unexposed areas remain soft.
Wafer Fabrication Materials and Their Properties
Silicon Wafer Characteristics
Silicon is the most common material used for wafer fabrication. It can withstand high temperatures, is abundant, and has the right semiconductor properties. Silicon wafers provide a stable, uniform surface for building intricate electronic circuits. They are essential for creating integrated circuits, which are the functional units of semiconductor devices.
Alternative Semiconductor Materials
While silicon is widely used, other materials are also important in wafer fabrication. These include:
- Silicon Germanium (SiGe)
- Sapphire (Al2O3)
- Gallium Arsenide (GaAs)
- Gallium Nitride (GaN)
- Diamond
- Zinc Oxide (ZnO)
- Silicon Carbide (SiC)
- Indium Phosphide (InP)
Each of these materials has unique properties that make them suitable for specific applications in the semiconductor industry.
Material Purity and Its Importance
The purity of the materials used in wafer fabrication is crucial. Impurities can affect the performance and reliability of the semiconductor devices. High-purity materials ensure that the wafers have the necessary properties for the manufacturing process. This is why recognizing the properties of different semiconductor materials and ensuring their purity is a key part of the semiconductor wafer fabrication process.
Conclusion
In wrapping up, wafer processing is a vital part of the semiconductor industry. From the initial stages of creating a blank wafer to the final steps of cutting and packaging, each process is crucial. We explored how wafers are made, polished, and cleaned, and how they are transformed into the microchips that power our devices. Understanding these steps helps us appreciate the complexity and precision involved in making the technology we use every day. We hope this article has provided a clear and helpful overview of wafer processing. Stay tuned for more insights into the fascinating world of semiconductor manufacturing!
Frequently Asked Questions
What is the difference between front-end and back-end wafer processing?
Front-end wafer processing involves creating microchips on a blank wafer, while back-end processing includes cutting the wafer into dies and packaging them for protection.
What is photolithography in semiconductor manufacturing?
Photolithography is a process where a wafer is coated with a light-sensitive material and then exposed to light through a mask to create patterns on the wafer.
Why is wafer cleaning important in semiconductor manufacturing?
Wafer cleaning removes particles and contaminants that could affect the performance of the microchips, ensuring high-quality and reliable semiconductor devices.
What materials are commonly used in Chemical-Mechanical Planarization (CMP)?
CMP uses a mixture of chemicals and abrasive particles to polish the wafer, creating a smooth and flat surface necessary for subsequent manufacturing steps.
How are thinned wafers used in the semiconductor industry?
Thinned wafers are used in applications where space is limited, such as in smartphones and other compact electronic devices.
What is the role of ion implantation in wafer processing?
Ion implantation introduces impurities into the wafer to change its electrical properties, which is essential for creating different components of a microchip.