Understanding Wafer Size in Semiconductor Fabrication
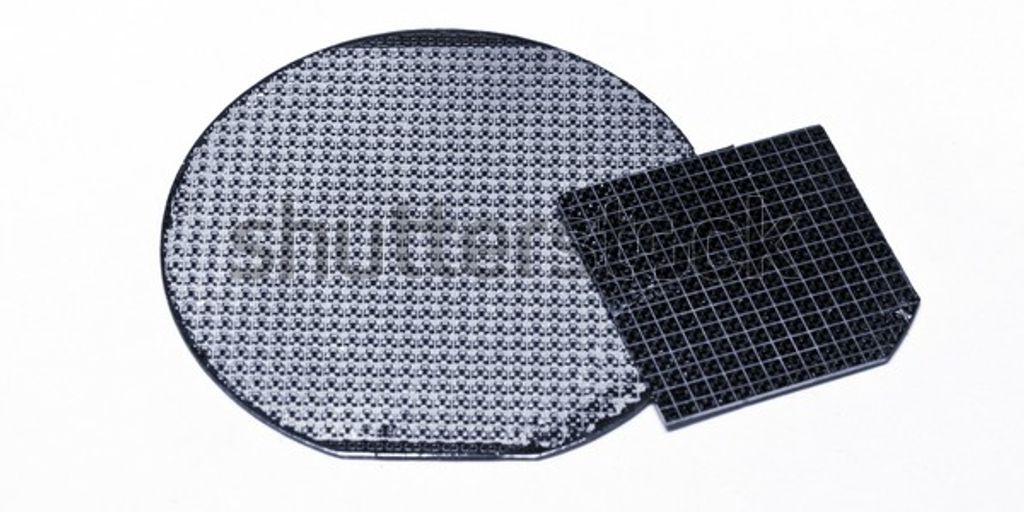
In the world of semiconductor fabrication, the size of silicon wafers plays a crucial role. Over the years, the diameter of these wafers has increased significantly to meet the demands of modern technology. From the early days of small 25mm wafers to the current standard of 300mm, and the potential future shift to 450mm, understanding wafer sizes is vital for anyone interested in the field.
Key Takeaways
- Wafer sizes have evolved from 25mm to the current standard of 300mm, with 450mm being the next potential milestone.
- Larger wafer sizes allow for more semiconductor devices to be produced from a single wafer, increasing efficiency and reducing costs.
- The transition to larger wafers involves significant technological and economic challenges, including manufacturing difficulties and the need for new equipment.
- Current standard wafer sizes range from 100mm to 300mm, with research ongoing for 450mm wafers.
- Increasing wafer sizes is driven by the need to reduce costs and meet market demand, despite the challenges involved.
Historical Evolution of Wafer Sizes
Early Developments in Wafer Sizes
The historical trend of the size of the silicon wafer has seen significant changes over the decades. Initially, wafers were as small as 25mm in diameter. By the 1960s, 2-inch (50mm) wafers became the norm, followed by 3-inch (75mm) wafers in the early 1970s. The 4-inch (100mm) wafers emerged around 1975 and quickly became the standard.
Transition to 300mm Wafers
The shift to larger wafers continued with the introduction of 5-inch (125mm) and 6-inch (150mm) wafers in the 1980s. By the 1990s, 8-inch (200mm) wafers were widely used. The most significant change came in the early 2000s with the adoption of 300mm wafers. This transition reduced the price per die by about 30-40%, making production more cost-effective.
Future Prospects: 450mm Wafers
Looking ahead, the industry is exploring the potential of 450mm wafers. These larger wafers could further enhance production efficiency and reduce costs. However, there are significant technological challenges to overcome before they can become mainstream.
Importance of Wafer Size in Semiconductor Fabrication
Impact on Production Efficiency
A larger wafer diameter allows for the production of more semiconductor devices from a single wafer, which boosts productivity and efficiency. If foundries were still using 1-inch wafers today, they wouldn’t be able to meet the high demand for smartphones, tablets, and PCs.
Cost Implications
Increasing wafer size can lead to significant cost savings. Larger wafers mean more chips per wafer, reducing the cost per chip. However, the initial investment in new equipment and technology to handle larger wafers can be substantial.
Technological Challenges
Scaling up wafer sizes is not a simple task. It requires re-engineering silicon wafer manufacturing technologies and significant capital investment. The process involves overcoming numerous technical hurdles to ensure the quality and reliability of the larger wafers.
Current Standard Wafer Sizes
Common Sizes in Use Today
In semiconductor device fabrication, wafers come in various sizes. The most common sizes are 2-inch (51 mm), 4-inch (100 mm), 6-inch (150 mm), and 8-inch (200 mm). Over time, the size of wafers has increased, with 300mm diameter wafers being the standard in high-volume manufacturing today.
Advantages of 300mm Wafers
The shift to larger wafers, like the 300mm size, has brought several benefits. Larger wafers allow more dies per wafer, which helps in reducing costs. Even small increases in wafer size can significantly boost yields due to the extra surface area available.
Research on 450mm Wafers
Looking ahead, research is ongoing into 450mm wafers. These larger wafers could further enhance production efficiency and reduce costs, but they also come with their own set of challenges. The industry continues to explore the potential of these massive wafers for future semiconductor fabrication needs.
Technical Specifications of Semiconductor Wafers
Diameter and Thickness
Semiconductor wafers come in various diameters, ranging from 25mm to the current standard of 300mm. The thickness of these wafers typically varies between 500 to 900 micrometers, which is about the thickness of 5 to 10 human hairs.
Surface Quality
The surface of a semiconductor wafer must be extremely flat and smooth. This high level of polish is crucial for photolithography processes, which require precise etching of tiny components at nearly atomic scales.
Material Composition
Most semiconductor wafers are made from silicon, but other materials like gallium arsenide and silicon carbide are also used for specific applications. The choice of material impacts the wafer’s electrical properties and suitability for different types of semiconductor devices.
Economic Factors Driving Wafer Size Increase
Cost Reduction Strategies
Increasing the size of semiconductor wafers can significantly reduce production costs. Larger wafers allow more chips to be produced in a single fabrication step, which means the cost per chip decreases. For example, moving from 200mm to 300mm wafers reduced the price per chip by about 30-40%. This cost efficiency is a major driver for the industry to adopt larger wafers.
Investment in Wafer Size Innovation
Developing larger wafers requires substantial investment. The technology to manufacture bigger wafers has to be re-engineered, which involves significant capital. Estimates suggest that the investment in wafer size innovation could be in the triple-digit billion USD range. This high cost is justified by the long-term savings and efficiency gains.
Market Demand and Supply
The demand for more powerful and smaller electronic devices drives the need for larger wafers. As consumer electronics become more advanced, the semiconductor industry must keep up by producing more chips at a lower cost. Larger wafers help meet this demand by increasing production capacity and reducing costs, making it possible to supply the market with affordable, high-performance chips.
Challenges in Scaling Up Wafer Sizes
Scaling up wafer sizes presents several significant challenges. Manufacturing larger wafers requires advanced technology and substantial investment. The transition from smaller to larger wafers, such as moving from 200mm to 300mm, has already shown that the costs associated with this shift can be enormous, often reaching into the hundreds of billions of dollars.
Here are some key challenges faced in this process:
- Manufacturing Difficulties: As wafer sizes increase, maintaining precision in processes like patterning and etching becomes more complex. This is crucial because even minor errors can lead to significant defects in the final product.
- Equipment and Tooling Upgrades: Existing manufacturing tools may not be suitable for larger wafers. This means that companies must invest in new equipment, which can be a major financial burden.
- Quality Control Issues: Ensuring consistent quality across larger wafers is challenging. Larger wafers can have more defects, and identifying these defects can be more difficult, leading to potential losses in production.
In summary, while increasing wafer size can lead to greater efficiency and lower costs per chip, the challenges involved in scaling up are substantial and require careful consideration and planning.
Future Trends in Wafer Size Development
Emerging Technologies
The semiconductor industry is always pushing the boundaries of what’s possible. New technologies are being developed to make even larger wafers. These advancements could lead to more efficient production and lower costs. However, there are still many challenges to overcome, such as ensuring the quality and reliability of these larger wafers.
Industry Collaborations
To tackle the challenges of increasing wafer sizes, companies are working together more than ever before. Collaborations between different sectors of the industry are essential for sharing knowledge and resources. This teamwork helps to speed up innovation and bring new technologies to market faster.
Potential Market Shifts
As wafer sizes continue to grow, the market dynamics are also changing. Larger wafers can lead to lower costs per chip, which could make semiconductors more affordable. This shift could open up new opportunities in various industries, from consumer electronics to automotive applications. However, it also means that companies need to adapt quickly to stay competitive.
Conclusion
In summary, the size of silicon wafers plays a crucial role in the semiconductor industry. Over the years, the industry has moved from small 25mm wafers to much larger 300mm wafers, with plans to go even bigger. This increase in size helps make more chips from a single wafer, which lowers costs and boosts production. As technology keeps advancing, we can expect even larger wafers to become the norm, further driving innovation and efficiency in semiconductor fabrication.
Frequently Asked Questions
What are the common sizes of silicon wafers?
Silicon wafers come in different sizes, ranging from 25.4 mm (1 inch) to 300 mm (11.8 inches). The most common size used today is 300 mm.
Why is wafer size important in semiconductor fabrication?
Larger wafer sizes allow for more semiconductor devices to be made from a single wafer, which improves efficiency and productivity. This is important for meeting the high demand for devices like smartphones and computers.
What is the current standard wafer size in semiconductor fabs?
The current standard wafer size in most semiconductor fabs is 300 mm. There are ongoing efforts to develop 450 mm wafers for future use.
What are the challenges in increasing wafer size?
Increasing wafer size involves significant challenges, including the need for new manufacturing technologies, equipment upgrades, and strict quality control measures.
How does wafer size affect production costs?
Larger wafers can reduce production costs because they allow more chips to be made at once. However, the initial investment in new technology and equipment can be very high.
What future trends are expected in wafer size development?
Future trends in wafer size development include the adoption of 450 mm wafers, advancements in manufacturing technologies, and increased industry collaborations to meet market demands.