Understanding Wafer Size: What You Need to Know
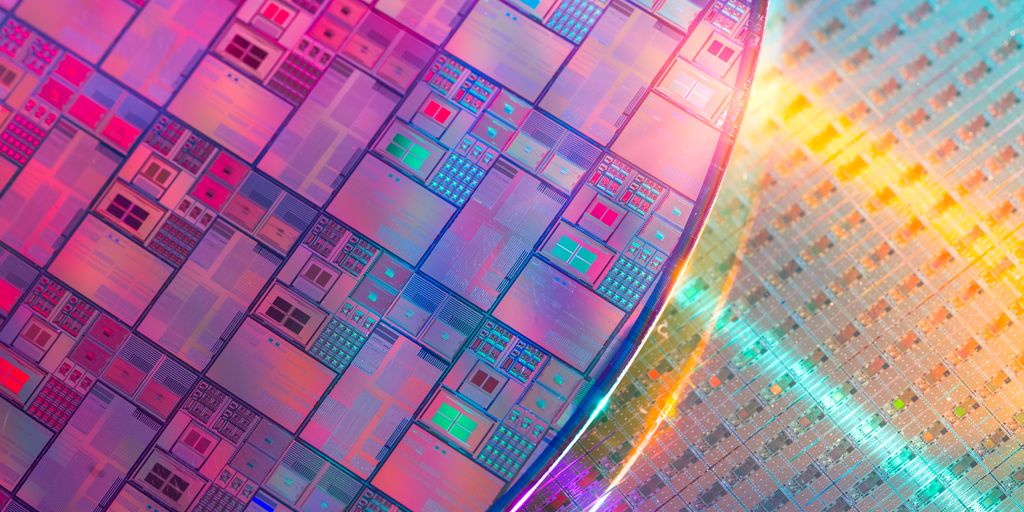
When it comes to making semiconductors, the size of the wafer is super important. Bigger wafers can make more chips, which helps make things like smartphones and computers work better and faster. But there are a lot of details to understand about wafer sizes, like how they are measured and what challenges come with making them bigger. This article will help you understand everything you need to know about wafer sizes.
Key Takeaways
- Larger wafers can produce more semiconductor devices, boosting productivity and efficiency.
- Common wafer sizes include 150mm, 200mm, 300mm, and 450mm, with each size having specific uses and benefits.
- The industry has shifted from measuring wafers in inches to millimeters to ensure better accuracy and consistency.
- Increasing wafer size comes with technical and economic challenges that need to be addressed.
- The thickness of the wafer also plays a crucial role in determining the performance of semiconductor devices.
The Importance of Wafer Size in Semiconductor Manufacturing
Wafer size plays a crucial role in the semiconductor industry. A larger wafer diameter enables producing more semiconductor devices from a single wafer, enhancing productivity and efficiency. If foundries still produced 1-inch wafers today, they wouldn’t be able to support the volume of smartphones, tablets, and PCs. The industry has invested heavily over the last 30 years to increase wafer sizes, moving from 1-inch wafers to the current standard of 300mm, which is 11.8 times larger. There are plans to move towards a 450mm wafer size, which is 1.5 times larger than the 300mm wafers.
Impact on Productivity and Efficiency
Larger wafers mean more chips can be made at once, which boosts productivity and lowers costs. This is essential for meeting the high demand for electronic devices.
Common Misconceptions About Wafer Measurements
One common mistake is thinking that a 300mm wafer is 12 inches, but it’s actually slightly less. Understanding these measurements is key to grasping the scale of production.
Future Trends in Wafer Size
The industry is looking to further increase wafer sizes to 450mm. This shift will require significant technological advancements and investment but promises even greater efficiency and productivity.
Common Wafer Sizes and Their Applications
In semiconductor manufacturing, wafer sizes play a crucial role in determining the efficiency and productivity of the process. The most common wafer size is 300mm, but researchers are working to make 450mm wafers more practical and thus more common. Currently, wafer sizes range from 25.4mm to 450mm.
150mm Wafers: Uses and Benefits
150mm wafers, also known as 6-inch wafers, are widely used in the semiconductor industry. They offer a good balance between cost and performance, making them suitable for a variety of applications. These wafers are often used in the production of microcontrollers, sensors, and other small-scale devices.
200mm Wafers: Industry Standards
200mm wafers, or 8-inch wafers, have become an industry standard due to their larger size and increased capacity. They are commonly used in the manufacturing of integrated circuits and other electronic components. The larger size allows for more chips to be produced per wafer, increasing overall productivity.
300mm and 450mm Wafers: The Future of Semiconductors
300mm wafers, also known as 12-inch wafers, are currently the most common size in the industry. They offer significant advantages in terms of productivity and efficiency, as more chips can be produced per wafer. Researchers are now focusing on developing 450mm wafers, which could further revolutionize the industry by allowing even more chips to be produced per wafer, thus increasing productivity and reducing costs.
How Wafer Size Affects Device Performance
Wafer size plays a significant role in determining the performance of semiconductor devices. Larger wafers can produce more chips, which boosts productivity and efficiency. This is crucial for meeting the high demand for modern electronics like smartphones and tablets.
Influence on Computing Power
The size of the wafer directly impacts the computing power of the devices made from it. For instance, a chip designed for a gaming computer will have different requirements compared to one for a smartphone. Larger wafers allow for more powerful chips, enhancing overall device performance.
Role in Different Technologies
Different technologies require different wafer sizes. For example, high-performance computing devices may need larger wafers to meet their processing needs, while smaller devices like sensors might use smaller wafers. This flexibility allows manufacturers to tailor wafer sizes to specific technological needs.
Scalability and Limitations
While larger wafers offer many benefits, they also come with challenges. Scaling up wafer size can lead to technical difficulties and increased costs. However, the benefits often outweigh these challenges, making larger wafers a popular choice in the industry.
The Evolution of Wafer Size Measurement
Transition from Inches to Millimeters
During the 1980s and 1990s, wafer sizes were commonly measured in inches. For example, 6-inch (150mm) wafers were standard. However, as the industry progressed, there was a shift towards using millimeters for more precise measurements. Today, 300mm wafers are the norm, and this change has allowed for a significantly larger wafer size, improving productivity and efficiency.
Accuracy and Precision in Measurements
Accurate wafer size measurement is crucial for the semiconductor industry. Even a small error can lead to significant issues in production. The transition to millimeters has helped in avoiding rounding errors and ensuring consistency across the industry. This precision is vital for maintaining the quality and performance of semiconductor devices.
Technological Innovations in Measurement Techniques
Over the years, there have been numerous technological advancements in wafer measurement techniques. These innovations have made it possible to measure wafers with greater accuracy and precision. As a result, the industry has been able to produce larger wafers, such as the 300mm and 450mm wafers, which are now becoming more common. These advancements have also contributed to reducing the cost per die, making semiconductor manufacturing more cost-effective.
Challenges in Increasing Wafer Size
Increasing wafer size is not a trivial process. As a matter of fact, silicon wafer manufacturing technologies were re-engineered in order to achieve the technology necessary to increase the wafer size during the years. It is difficult to grasp the amount of capital invested in the size growth innovation. My guess is around a triple-digit Billion USD.
Larger wafer sizes are prone to defects such as contamination and warpage. Careful process optimization is important for leveraging the utmost benefits of the wafer size in use for improved yield and production efficiency.
A unit of wafer fabrication step, such as an etch step, can produce more chips proportional to the increase in wafer area, while the cost of the unit fabrication step goes up more slowly than the wafer area. This was the cost basis for increasing wafer size. Conversion to 300 mm wafers from 200 mm wafers began in early 2000, and reduced the price per die for about 30–40%. Larger diameter wafers allow for more die per wafer.
The issue has to do with something about 450mm wafers that aren’t practical due to mechanical issues, it seems like increasing the area that gets processed simultaneously is a slightly different goal than increasing the area of the wafer itself.
Why Millimeters Matter: The Precision of Wafer Size
When it comes to wafer size, precision is key. Measuring in millimeters instead of inches helps avoid rounding errors, ensuring that the size is exactly right. This level of accuracy is crucial for the semiconductor industry, where even a tiny mistake can lead to big problems.
Avoiding Rounding Errors
Using millimeters helps prevent rounding errors that can occur when using inches. For example, a 300mm wafer is often mistakenly rounded up to 12 inches, but it’s actually 11.8 inches. This small difference can have a significant impact on the manufacturing process.
Ensuring Consistency Across the Industry
Standardizing measurements in millimeters ensures consistency across the industry. This uniformity is essential for global collaboration and quality control. When everyone uses the same measurement system, it’s easier to maintain high standards and avoid misunderstandings.
Benefits of Millimeter Precision
The precision of millimeter measurements offers several benefits:
- Improved accuracy: Millimeters provide a more exact measurement, reducing the risk of errors.
- Better quality control: Consistent measurements help maintain high standards in production.
- Enhanced productivity: Accurate measurements lead to more efficient manufacturing processes.
In summary, using millimeters for wafer size measurements is not just a matter of preference; it’s a necessity for ensuring the highest level of precision and quality in semiconductor manufacturing.
The Role of Wafer Thickness in Semiconductor Performance
Determining Optimal Thickness
The thickness of a wafer is crucial for its mechanical strength. It must be thick enough to support its own weight without cracking during handling. Different materials, like silicon, have varying thickness requirements. The right thickness ensures the wafer can withstand stress and heat during manufacturing.
Impact on Device Capabilities
Wafer thickness affects the electrical properties and handling characteristics of the wafer. Thinner wafers are often preferred for integrated circuit (IC) packaging because they offer benefits like improved thermal conductivity and reduced warpage. However, they are more prone to stress-induced defects and require careful handling to avoid breakage.
Comparing Different Thicknesses
Here’s a quick comparison of the advantages and considerations for different wafer thicknesses:
Thickness Range | Advantages | Considerations |
---|---|---|
Smaller Thickness | – Improved thermal conductivity<br>- Reduced warpage<br>- Compaction and miniaturization | – Reduced mechanical strength<br>- Susceptibility to breakage |
Larger Thickness | – Enhanced mechanical integrity<br>- Lower vulnerability to stress-induced defects | – Less efficient thermal conductivity<br>- Increased warpage |
Finding the right balance between thickness and mechanical integrity is essential in wafer technology.
Conclusion
Understanding wafer size is crucial in the world of technology. Larger wafers mean more chips can be made at once, which boosts productivity and efficiency. This is why the industry has moved from small 1-inch wafers to larger sizes like 300mm and even 450mm. It’s important to measure wafers in millimeters for accuracy. As technology keeps advancing, wafer sizes will likely continue to grow, helping us make even more powerful and efficient devices.
Frequently Asked Questions
Why does wafer size matter?
A larger wafer allows more semiconductor devices to be made from a single wafer, boosting productivity and efficiency. If foundries still made 1-inch wafers today, they couldn’t support the volume of smartphones, tablets, and PCs.
What are the common wafer sizes and their inch equivalents?
Common wafer sizes include 150mm (5.9 inches), 200mm (7.9 inches), 300mm (11.8 inches), and 450mm (18 inches). Many people mistakenly round 300mm to 12 inches, which is incorrect.
How has wafer size changed over the years?
The semiconductor industry has invested a lot to increase wafer sizes over the last 30 years. While 1-inch wafers were once common, today’s standard is 300mm, and there are plans to move to 450mm wafers.
How does wafer size affect computing power?
The size of a wafer impacts its computing power and what it can fit into. For example, a chip for a gaming computer has different needs compared to one for a smartphone.
Why are wafers measured in millimeters now?
Wafers used to be measured in inches, but as they got smaller, it became less practical. Millimeters provide more accurate measurements and avoid rounding errors.
What are the challenges in increasing wafer size?
Increasing wafer size is complex and costly. It requires re-engineering manufacturing technologies and involves significant capital investment.