Wafer Level Burn-In: Enhancing Reliability and Performance
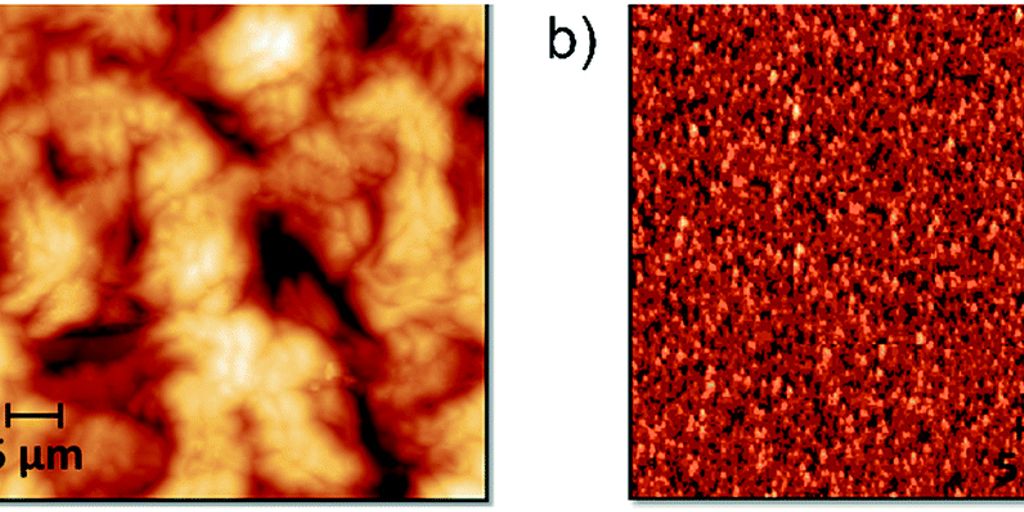
Wafer Level Burn-In (WLBI) testing is a key method used to boost the reliability of semiconductor devices. By finding and removing potential early failures, WLBI ensures that only the most reliable products make it to the market. This process not only gives manufacturers confidence in their production but also offers a certification of reliability to customers. As semiconductor devices get smaller and more complex, WLBI becomes even more important in keeping high standards.
Key Takeaways
- WLBI testing helps find and remove defective semiconductor dies early, improving overall product reliability.
- It provides manufacturers with better control over their production processes and helps certify the reliability of their products.
- WLBI testing uses advanced methods and automation to enhance efficiency and support the design of more complex semiconductors.
- The key benefits of WLBI include improved reliability, cost savings, and better yield from semiconductor manufacturing.
- Implementing WLBI comes with challenges like technical complexities, cost, and scalability issues, but it remains crucial for future advancements.
Understanding Wafer Level Burn-In Testing
Definition and Purpose
Wafer Level Burn-In (WLBI) testing is a crucial step in making semiconductors. It helps make sure that the tiny parts inside electronics work well and last a long time. WLBI testing focuses on finding and fixing problems early. This way, the final products are more reliable.
Historical Context
WLBI has been around for a while. Companies like Motorola started using it back in 1998. They worked with other companies to make the testing better. Over the years, the methods have improved a lot, making the tests more accurate and faster.
Current Industry Standards
Today, WLBI testing follows strict rules. These rules make sure that every chip on a wafer gets tested the same way. The tests use high temperatures and electrical stress to find any weak spots. This helps in making sure that the final products are of high quality and reliable.
Enhancing Semiconductor Reliability with WLBI
Wafer Level Burn-In (WLBI) testing is a crucial methodology in enhancing the reliability of semiconductors. By identifying and segregating potential early failures, WLBI ensures that only the most reliable products reach the market. This process not only provides manufacturers with confidence in their process control but also offers a pedigree certificate of reliability to customers. As semiconductor devices continue to shrink in size and grow in complexity, the importance of WLBI in maintaining high standards of quality and reliability cannot be overstated. Incorporating WLBI into the semiconductor manufacturing process is essential for meeting the fast-paced demands of modern technology markets.
Technological Advancements in WLBI
Innovative Testing Methods
Recent advancements in Wafer Level Burn-In (WLBI) have introduced new software solutions that enhance the testing process. For example, Renesas’s acquisition of Altium has led to improved digital integration with physical production lines. This shift towards digitalization promises to streamline WLBI procedures and improve overall outcomes.
Automation and Efficiency
The integration of automated systems in WLBI has significantly increased efficiency. Advanced WLBI systems now apply electrical stress to semiconductor wafers at the wafer level, identifying defective dies early in the process. This early-stage testing saves time and resources by preventing defective chips from progressing further in the manufacturing process.
Impact on Semiconductor Design
WLBI’s technological advancements have also impacted semiconductor design. By identifying defects early, WLBI allows for adjustments in the design phase, leading to more reliable and efficient semiconductor devices. This proactive approach not only enhances product reliability but also boosts customer satisfaction.
Key Benefits of Wafer Level Burn-In
Reliability Enhancement
Wafer Level Burn-In (WLBI) significantly boosts the reliability of semiconductor devices. By catching defects early, manufacturers can ensure that only the most reliable products reach the market. This process is crucial for delivering a statistically more reliable product population to customers.
Cost Efficiency
WLBI helps in reducing production costs by identifying defects early in the manufacturing process. This early detection minimizes the need for extensive post-production testing and reduces the chances of costly recalls. By catching defects early, we help manufacturers improve the efficiency of their production lines and deliver higher-quality products to the market.
Yield Improvement
Implementing WLBI leads to improved yield analysis. By identifying and eliminating defective dies before they are packaged, manufacturers can ensure higher quality and performance of semiconductor products. This process not only enhances the overall yield but also ensures that the final products are of the highest quality.
Challenges in Implementing WLBI
Technical Complexities
Implementing Wafer Level Burn-In (WLBI) comes with its own set of technical challenges. The process requires precise control over various parameters to ensure accurate results. Even minor deviations can lead to significant errors, making the process highly sensitive. Additionally, the integration of WLBI into existing manufacturing lines can be complex, requiring specialized equipment and expertise.
Cost Implications
While WLBI offers numerous benefits, it also comes with high initial costs. The investment in specialized equipment and the need for skilled personnel can be substantial. Moreover, ongoing maintenance and calibration add to the overall expenses. Despite these costs, the long-term benefits often outweigh the initial investment, making it a worthwhile consideration for many manufacturers.
Scalability Issues
Scaling WLBI for mass production presents another set of challenges. The process needs to be efficient enough to handle large volumes without compromising on quality. This requires continuous monitoring and adjustments, which can be resource-intensive. Additionally, the variability in wafer sizes and types adds another layer of complexity to the scaling process.
Future Trends in Wafer Level Burn-In
The Wafer-level Test and Burn-in market is expected to witness significant growth in the coming years. Factors such as the increasing complexity of semiconductor devices, stringent quality requirements, and the demand for reliable testing and burn-in solutions drive market expansion. Continued investments in research and development, customization for specific device requirements, and integration with advanced data analytics and artificial intelligence technologies will shape the future outlook.
Conclusion
Wafer Level Burn-In (WLBI) testing plays a vital role in making sure semiconductor devices are reliable and perform well. By catching and removing faulty parts early, WLBI helps manufacturers deliver high-quality products to the market. This process not only boosts the confidence of manufacturers in their production methods but also assures customers of the product’s reliability. As technology continues to advance and devices become more complex, the importance of WLBI in maintaining high standards of reliability and performance cannot be overstated.
Frequently Asked Questions
What is Wafer Level Burn-In (WLBI)?
Wafer Level Burn-In (WLBI) is a testing process used on semiconductor wafers before they are cut into individual chips. It helps find and remove defective parts early, making sure that only the best products reach the market.
How does WLBI improve semiconductor reliability?
WLBI improves semiconductor reliability by catching faulty chips early in the manufacturing process. This reduces the chances of failures later on, making the final products more reliable.
What are the main benefits of using WLBI?
The main benefits of using WLBI include better reliability, cost savings, and higher production yields. By finding defects early, companies can save money and produce higher quality products.
What challenges come with implementing WLBI?
Some challenges of implementing WLBI include technical difficulties, high costs, and scalability issues. These challenges can make it tough for some companies to adopt WLBI fully.
How has technology improved WLBI?
Technology has improved WLBI by introducing new testing methods and automation. These advancements make the process faster and more efficient, helping companies keep up with the growing complexity of semiconductor devices.
What does the future hold for WLBI?
The future of WLBI looks promising with emerging technologies and increased market demand. Ongoing research and development are expected to bring even more improvements to the process.