Wafer SiC: The Future of Power Electronics
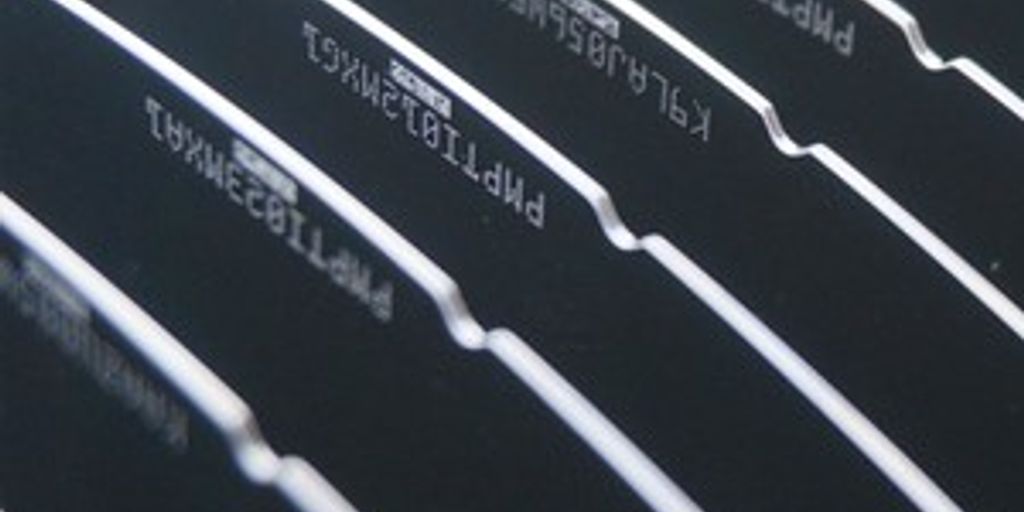
Silicon Carbide (SiC) wafers are set to revolutionize the world of power electronics. Unlike traditional silicon, SiC offers unique properties that make it ideal for high-power and high-efficiency applications. From electric vehicles to industrial machinery, SiC wafers are becoming the backbone of modern technology. This article explores the unique properties, applications, technological advancements, and future trends of SiC wafers, while also addressing the challenges in their adoption.
Key Takeaways
- Silicon Carbide (SiC) wafers offer superior performance compared to traditional silicon, especially in high-power applications.
- SiC’s unique properties, like wide bandgap and high thermal conductivity, make it ideal for advanced power electronics.
- SiC is increasingly used in electric vehicles, industrial machinery, and railcars, driving innovation in these fields.
- Technological advancements in SiC wafer production are making these wafers more efficient and cost-effective.
- Despite the benefits, challenges like cost and manufacturing scalability need to be addressed for wider adoption.
The Unique Properties of Wafer SiC
Silicon Carbide (SiC) wafers are transforming the semiconductor industry due to their exceptional properties. These wafers are made from a single crystal of SiC, a compound semiconductor where silicon and carbon atoms form a strong, three-dimensional network. This unique structure is the key to SiC’s outstanding characteristics.
Wide Bandgap Advantages
One of the most notable features of SiC wafers is their wide bandgap. A wide bandgap creates a high hurdle for electrons to overcome, resulting in two key benefits:
- High-Temperature Stability: Low intrinsic carrier concentrations mean SiC devices can operate at elevated temperatures without significant leakage currents, making them ideal for demanding environments.
- High Voltage Operation: The wide bandgap allows SiC devices to handle higher voltages compared to traditional silicon devices.
High Thermal Conductivity
SiC wafers also boast high thermal conductivity, which is crucial for power electronics. This property allows for efficient heat dissipation, ensuring that devices remain cool even under high power loads. This makes SiC an excellent choice for applications that require reliable performance over a wide range of temperatures.
High Breakdown Electric Field
Another significant advantage of SiC wafers is their high breakdown electric field strength. SiC can withstand electric fields ten times stronger than those silicon can handle. This means that SiC-based devices can be made smaller and more efficient, as they can operate at higher voltages without breaking down.
Applications of Wafer SiC in Power Electronics
Silicon carbide (SiC) wafers are transforming power electronics, offering superior performance and efficiency. Their unique properties make them ideal for various applications.
Electric Vehicles
SiC is suitable for high-voltage applications ranging up to several hundred volts and can withstand high temperatures in EV powertrains. This makes SiC perfect for electric vehicles (EVs), where efficiency and durability are crucial. SiC-based components help in reducing energy losses and improving the overall range of EVs.
Industrial Machinery
In industrial settings, SiC wafers are used in motor drives and power converters. They enable machines to operate more efficiently and at higher temperatures. This leads to lower energy consumption and reduced cooling requirements, making industrial processes more cost-effective.
Railcars
Rail transportation benefits from SiC technology by enhancing the efficiency and reliability of power systems. SiC components can handle higher voltages and temperatures, which is essential for the demanding conditions in railcars. This results in more reliable and efficient rail systems.
Technological Advancements in SiC Wafer Production
The latest advancements in SiC processing have significantly improved the production of silicon carbide wafers. These innovations are crucial for meeting the growing global demand for high-performance power electronics.
Crystal Growth Techniques
One of the key areas of progress is in crystal growth techniques. Manufacturers are now able to produce larger SiC wafers, reaching up to 200mm in diameter. This increase in size allows for more devices to be integrated onto a single chip, enhancing production efficiency and reducing costs.
Epitaxial Growth Methods
Epitaxial growth methods have also seen substantial improvements. These methods are essential for creating high-quality SiC layers on substrates, which are vital for the performance of power devices. Advances in this area have led to better control over layer thickness and uniformity, resulting in more reliable and efficient devices.
Packaging Solutions
Innovative packaging solutions are another important advancement. Effective packaging is crucial for protecting SiC devices from environmental factors and ensuring their long-term reliability. New packaging technologies are being developed to handle the unique properties of SiC, such as its high thermal conductivity and breakdown electric field, further enhancing device performance and lifespan.
Comparing SiC and Silicon in Power Devices
Efficiency Gains
Silicon Carbide (SiC) devices are known for their high-speed switching properties and low power loss. This makes them more efficient than traditional silicon devices. SiC’s ability to handle higher voltages and temperatures translates to better performance in power electronics.
Power Density
SiC has a higher power density compared to silicon. This means that devices made with SiC can be smaller and lighter, which is especially important in applications like electric vehicles and industrial machinery. The reduced size and weight can lead to cost savings and improved system performance.
Reliability
SiC is more reliable than silicon in high-power and high-temperature environments. Its superior thermal conductivity allows it to dissipate heat more effectively, reducing the risk of overheating and failure. This makes SiC a better choice for applications that require long-term stability and durability.
Future Trends in SiC Wafer Technology
Research and Development
The future development and adoption of SiC wafer technology are expected to accelerate, driven by ongoing research in crystal growth techniques, epitaxial growth methods, and packaging solutions. These advancements aim to meet the increasing demand for energy-efficient and high-power applications. Constant innovations and developments in SiC wafer technology are anticipated to drive market growth in the coming years.
Market Growth
The industry is poised to capitalize on technological advancements and innovations to meet the needs of a growing global demand for SiC wafers. Today, with the semiconductor industry expanding at an unprecedented rate, the demand for high-quality wafers is paramount to meet the growing needs of various applications. In this landscape, Silicon Carbide (SiC) wafers emerge as indispensable components, poised to catalyze the next phase of semiconductor innovation.
Sustainability Impact
As the backbone of advanced power electronics and beyond, SiC wafers represent not only the foundation but also the frontier of cutting-edge semiconductor technology. These wafers are shaping the trajectory of future developments, with a significant focus on sustainability. The market is anticipated to grow in the forecast period, driven by the need for more sustainable and energy-efficient solutions in power electronics.
Challenges in Adopting SiC Wafers
Cost Factors
One of the main challenges in adopting SiC wafers is the high cost associated with their manufacturing process. SiC devices are more expensive to produce than traditional silicon-based counterparts due to the complex fabrication process and lower economies of scale. This high upfront cost can be a barrier, especially in price-sensitive markets like consumer electronics and automotive applications.
Manufacturing Scalability
Another significant challenge is the limited availability of SiC substrates and wafer sizes. While silicon wafers are widely available in large diameters, SiC substrates are less common and typically smaller. This leads to higher production costs and limits scalability. The shortage of large-size SiC wafers hampers mass production and impedes the commercialization of SiC technology in high-volume applications, such as electric vehicles and renewable energy systems.
Integration with Existing Systems
Integrating SiC wafers with existing systems also presents challenges. The different applications of SiC wafers require varying design complexities, which can hinder market adoption. Additionally, the process to manufacture these SiC wafers is becoming increasingly complex, making it difficult to keep costs low while achieving better efficiency. This complexity can slow down the integration of SiC technology into current systems, affecting its widespread adoption.
Conclusion
Silicon Carbide (SiC) wafers are paving the way for the future of power electronics. They offer better performance and efficiency than traditional silicon-based devices. With their unique properties, such as the ability to handle higher voltages and temperatures, SiC wafers are transforming industries like electric vehicles and industrial machinery. As technology advances and the demand for energy-efficient solutions grows, SiC wafers will continue to play a crucial role in shaping the future of power electronics. Their impact is already being felt, and their potential is vast, promising a more efficient and sustainable world.
Frequently Asked Questions
What is a SiC wafer?
A SiC wafer is a thin slice of silicon carbide, a material known for its high thermal conductivity, wide bandgap, and high breakdown electric field. These properties make it ideal for power electronics.
Why is SiC better than silicon for power electronics?
SiC is better than silicon because it can handle higher voltages, temperatures, and frequencies. This makes devices more efficient and reliable.
Where are SiC wafers used?
SiC wafers are used in electric vehicles, industrial machinery, and railcars. They help make these systems more efficient and powerful.
What are the challenges of using SiC wafers?
Some challenges include high costs, manufacturing scalability, and integrating them with existing systems. Overcoming these hurdles is crucial for wider adoption.
How are SiC wafers made?
SiC wafers are made using advanced crystal growth and epitaxial growth methods. These techniques ensure the wafers have the right properties for high-performance applications.
What is the future of SiC wafer technology?
The future looks bright with ongoing research and development, market growth, and a focus on sustainability. SiC wafers are expected to play a key role in next-generation power electronics.