A Deep Dive into Semiconductor Manufacturing: Processes and Technologies
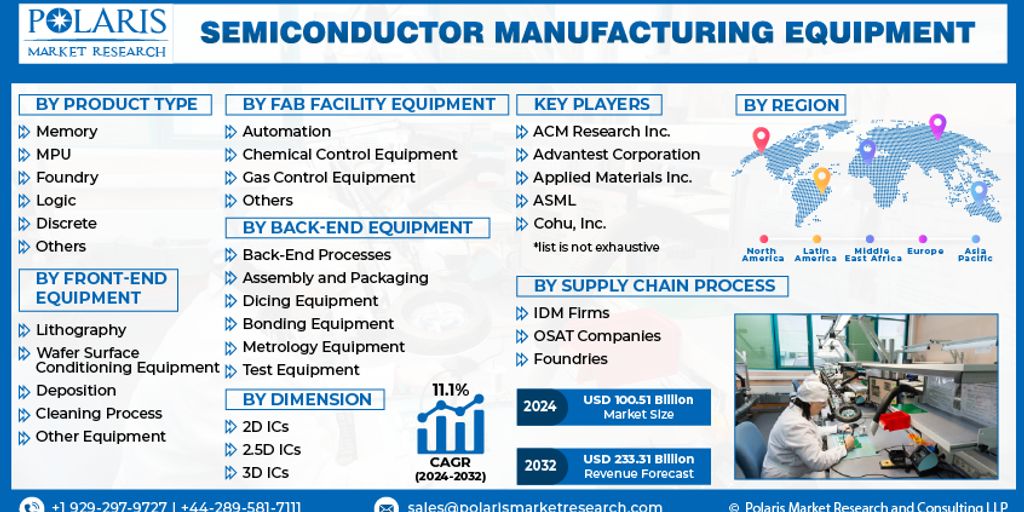
Semiconductor manufacturing is the backbone of modern technology. It involves turning raw materials into the tiny chips that run our electronic devices. This article will explore the history, processes, and future of semiconductor manufacturing. We’ll also look at the challenges faced by the industry and the latest technological innovations.
Key Takeaways
- Semiconductor manufacturing is essential for modern electronics, providing the chips that power devices like smartphones and computers.
- The industry has evolved significantly, driven by Moore’s Law and advancements in fabrication techniques.
- Key processes in chipmaking include wafer fabrication, photolithography, etching, and doping.
- Materials like silicon and rare earth elements are crucial for making semiconductors, with ongoing research into new materials.
- Challenges such as maintaining cleanroom standards and managing supply chains are critical for the industry’s success.
The Evolution of Semiconductor Manufacturing
Historical Milestones in Chipmaking
The journey of semiconductor manufacturing began in the mid-20th century. The invention of the transistor in 1947 marked a significant milestone. This was followed by the development of the integrated circuit in 1958, which revolutionized electronics. Over the decades, the industry has seen numerous advancements, each contributing to the miniaturization and increased power of semiconductor devices.
Impact of Moore’s Law
Moore’s Law has been a guiding principle in the semiconductor industry. It predicts that the number of transistors on a microchip will double approximately every two years. This has driven the relentless pursuit of smaller, more powerful, and more efficient chips. The impact of Moore’s Law is evident in the exponential growth of computing power and the reduction in cost per transistor.
Advancements in Fabrication Techniques
The evolution of semiconductor manufacturing is also marked by significant advancements in fabrication techniques. Early methods were relatively simple, but modern techniques involve complex processes like photolithography, etching, and doping. These advancements have enabled the production of chips with billions of transistors, pushing the boundaries of what is possible in electronics.
Key Processes in Semiconductor Manufacturing
Wafer Fabrication
The journey of semiconductor manufacturing starts with wafer fabrication. Thin silicon wafers are transformed into semiconductor devices through various processes. These include photolithography, etching, and doping. This stage is the foundation for all semiconductor production.
Photolithography and Etching
Photolithography is a process where light is used to transfer a geometric pattern from a photomask to a light-sensitive chemical photoresist on the wafer. Etching follows, where the exposed parts of the wafer are removed to create the desired patterns. This step is crucial for defining the intricate circuits on the chip.
Doping and Ion Implantation
Doping involves adding impurities to the silicon wafer to change its electrical properties. Ion implantation is a precise method of doping, where ions are accelerated and embedded into the wafer. This process is essential for creating the semiconductor’s conductive regions.
Materials Used in Semiconductor Manufacturing
Silicon and Its Alternatives
Silicon has been the backbone of the semiconductor industry since the early 1960s. It has virtually replaced germanium as the primary material for device fabrication. However, other materials like gallium arsenide and silicon carbide are also gaining traction due to their unique properties.
Role of Rare Earth Elements
Rare earth elements play a crucial role in semiconductor manufacturing. These elements, such as neodymium and yttrium, are essential for producing high-performance chips. They are often used in small quantities but are vital for the functionality of the devices.
Innovations in Semiconductor Materials
The quest for better performance has led to innovations in semiconductor materials. Companies are exploring new materials with unique properties to enhance the efficiency and performance of semiconductor components. This includes the development of advanced alloys and composites that can withstand higher temperatures and offer better electrical conductivity.
Challenges in Semiconductor Manufacturing
Maintaining Cleanroom Standards
Keeping cleanrooms free from contaminants is crucial in semiconductor manufacturing. Even the tiniest particles can ruin a chip. Maintaining these standards requires constant monitoring and advanced filtration systems. This process is both costly and complex.
Yield and Defect Management
Ensuring high yield and managing defects are ongoing challenges. Manufacturers must identify and fix defects quickly to avoid wasting materials and time. This involves sophisticated testing and quality control measures.
Supply Chain Issues
The global semiconductor supply chain is fragile and can be easily disrupted. Events like natural disasters or geopolitical tensions can halt production. This can lead to shortages in various industries, from electronics to automotive.
High R&D Costs
Developing new semiconductor technologies demands significant investment in research and development. This financial burden can be a major hurdle for companies, especially smaller ones.
Environmental Impact
Semiconductor manufacturing requires huge amounts of water to form ultrapure water, impacting the local environment and needing innovation and scrutiny. Companies are increasingly focusing on sustainability to reduce energy consumption and waste. Innovative technologies and practices are being developed to minimize the environmental impact of semiconductor production.
Technological Innovations in Semiconductor Manufacturing
AI and Machine Learning Applications
Artificial intelligence (AI) and machine learning (ML) are revolutionizing semiconductor manufacturing. These technologies help in predicting equipment failures, optimizing production processes, and improving yield rates. AI-driven analytics can identify patterns and anomalies that human operators might miss, leading to more efficient and reliable manufacturing.
Quantum Computing Implications
Quantum computing holds the promise of solving complex problems much faster than classical computers. This technology requires new types of semiconductors that can handle quantum bits or qubits. Researchers are exploring advanced materials like gallium carbide to meet these needs. The development of quantum semiconductors could lead to breakthroughs in various fields, from cryptography to drug discovery.
3D Chip Stacking
3D chip stacking is an innovative technique that involves stacking multiple layers of chips vertically. This method increases the density of transistors and improves performance without increasing the chip’s footprint. It also reduces power consumption and heat generation, making devices more efficient. Companies are investing heavily in this technology to stay competitive in the ever-evolving semiconductor industry.
The Future of Semiconductor Manufacturing
Emerging Trends and Predictions
As we look to the future, semiconductor manufacturing will continue to play a pivotal role in shaping our technological landscape. From the devices we hold in our hands to the systems that power our cities, the silicon innovators will remain at the forefront of technological advancement, propelling us into an increasingly interconnected and advanced world.
Sustainability and Green Manufacturing
Semiconductor manufacturing firms are increasingly focusing on sustainability, aiming to reduce energy consumption and waste. Innovative technologies and practices are being developed to minimize the environmental impact of semiconductor production.
Global Market Dynamics
The market for semiconductor devices is predicted to grow at a CAGR of 9.4 percent between 2020 and 2025. A growing number of foundries and consumer demand will encourage market sales, while both the IoT and AI sectors will generate demand for increased miniaturization, forcing changes to both semiconductor R&D and the manufacturing process.
Conclusion
In conclusion, semiconductor manufacturing is a fascinating and complex field that plays a crucial role in our everyday lives. From the tiny silicon wafers to the intricate processes of photolithography and etching, each step is vital in creating the powerful chips that drive our technology. As we continue to innovate and improve these processes, the future of semiconductor manufacturing looks bright, promising even more advanced and efficient devices. Understanding these processes not only gives us a greater appreciation for the technology we use daily but also highlights the incredible human ingenuity behind it all.
Frequently Asked Questions
What is semiconductor manufacturing?
Semiconductor manufacturing is the process of creating integrated circuits and other electronic components on a semiconductor material, usually silicon. This involves several steps like wafer fabrication, photolithography, and doping.
Why is silicon commonly used in semiconductor manufacturing?
Silicon is widely used because it is abundant, relatively inexpensive, and has excellent electrical properties that make it ideal for creating electronic components.
What is Moore’s Law?
Moore’s Law is the observation that the number of transistors on a microchip doubles approximately every two years, leading to an increase in computing power and a decrease in cost.
What are cleanroom standards in semiconductor manufacturing?
Cleanroom standards are strict guidelines to keep the manufacturing environment free from dust and other contaminants. This is crucial because even tiny particles can ruin semiconductor devices.
How does photolithography work?
Photolithography is a process used to transfer patterns onto a semiconductor wafer. It involves coating the wafer with a light-sensitive material, exposing it to light through a mask, and then etching the exposed areas.
What are some challenges in semiconductor manufacturing?
Some challenges include maintaining cleanroom standards, managing defects and yield, and dealing with supply chain issues.