Advancements in Wafer Level Package Technology
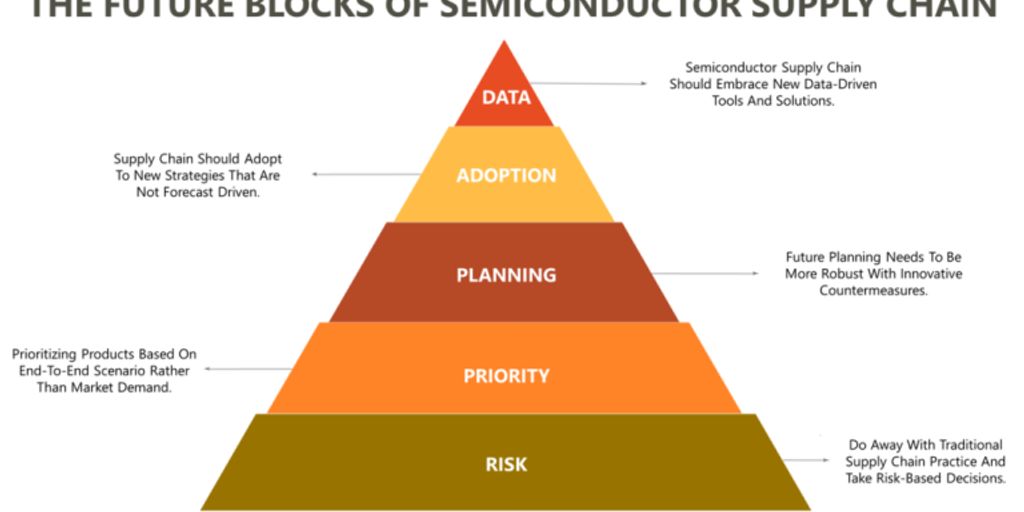
Wafer-Level Packaging (WLP) has revolutionized the semiconductor industry by enabling the packaging of dies while they are still on the wafer. This method contrasts with traditional packaging, where individual chips are packaged after dicing. WLP technologies, such as Fan-Out Wafer-Level Packaging (FOWLP) and Fan-In Wafer-Level Packaging (FIWLP), offer numerous benefits, including reduced chip size, streamlined manufacturing, and improved performance. As the demand for cost-effective and high-performance solutions grows, advancements in WLP continue to push the boundaries of what is possible in semiconductor technology.
Key Takeaways
- Wafer-Level Packaging allows for the packaging of dies while still on the wafer, contrasting with traditional methods.
- Key technologies in WLP include Fan-Out Wafer-Level Packaging (FOWLP) and Fan-In Wafer-Level Packaging (FIWLP).
- WLP offers benefits such as reduced chip size, streamlined manufacturing, and improved performance.
- Innovations in WLP are driven by the integration of multiple dies and advanced interposer and substrate techniques.
- Future trends in WLP include emerging applications, market growth, and a detailed technological roadmap.
Understanding Wafer-Level Packaging
Definition and Basics
Wafer-level packaging (WLP) is the technology of packaging the die while it is still on the wafer. Protective layers and electrical connections are added to the substrate before dicing. This method contrasts with traditional packaging, where wafers are diced into individual chips before packaging.
Differences from Traditional Packaging
Traditional packaging involves several steps after dicing, including attaching the die to a package substrate, wire bonding, and encapsulation. In contrast, WLP streamlines the process by integrating these steps at the wafer level, leading to reduced manufacturing time and cost.
Benefits of Wafer-Level Packaging
- Miniaturization: WLP allows for smaller package sizes, which is crucial for modern electronic devices.
- Performance: Enhanced electrical performance due to shorter interconnects.
- Cost-Effective: Reduced material usage and simplified manufacturing process.
- Reliability: Improved thermal and mechanical performance.
Key Technologies in Wafer-Level Packaging
Fan-Out Wafer-Level Packaging (FOWLP)
Fan-Out Wafer-Level Packaging (FOWLP) is a technology that allows for higher levels of integration and improved thermal performance. By redistributing the I/O pads, FOWLP enables more external connections without increasing the die size. This makes it ideal for applications requiring high performance and miniaturization.
Fan-In Wafer-Level Packaging (FIWLP)
Fan-In Wafer-Level Packaging (FIWLP) focuses on keeping the I/O pads within the die area, making it a cost-effective solution for many applications. This technology is particularly useful for devices where space is a constraint but performance cannot be compromised.
Wafer-Level Chip-Scale Packaging (WLCSP)
Wafer-Level Chip-Scale Packaging (WLCSP) is a technique where the packaging is done at the wafer level, resulting in a package that is almost the same size as the die. This method is highly efficient and is widely used in mobile and consumer electronics. WLCSP offers several advantages, including reduced package size, lower cost, and improved electrical performance.
Innovations Driving Wafer-Level Packaging
Integration of Multiple Dies
The integration of multiple dies into monolithic systems is a significant innovation in wafer-level packaging. This approach allows for enhanced performance and functionality by combining different types of dies, such as processors, memory, and sensors, into a single package. This integration meets the increasing demand for cost-effective performance in top-end applications.
Advanced Interposer and Substrate Techniques
Advanced interposer and substrate techniques are crucial for the success of wafer-level packaging. These techniques involve using high-density interposers and substrates to improve electrical performance and thermal management. Key advancements include:
- High-density interposers
- Improved thermal management
- Enhanced electrical performance
Heterogeneous Integration
Heterogeneous integration refers to the combination of different types of semiconductor technologies within a single package. This innovation enables the integration of diverse functionalities, such as analog, digital, and RF components, leading to more versatile and powerful devices. Heterogeneous integration is driving the next wave of miniaturization and performance improvements in semiconductor devices.
Challenges and Solutions in Wafer-Level Packaging
One of the primary challenges in wafer-level packaging is addressing I/O limitations. As devices become more complex, the need for higher input/output (I/O) counts increases. Innovative solutions such as through-silicon vias (TSVs) and redistribution layers (RDLs) are being developed to overcome these limitations.
Cost-effective manufacturing remains a significant hurdle. The progress in wafer and package level defect inspection is crucial to reducing costs. The imaging challenges come from the significantly higher ratio of scanned area to required measurement resolution. For a 300mm wafer, the ratio is on order of millions to one. Implementing advanced automation and process control can help mitigate these costs.
Ensuring the reliability of wafer-level packaged devices is essential. Testing methodologies must evolve to keep pace with the advancements in packaging technology. This includes developing new testing protocols and equipment capable of handling the unique demands of wafer-level packaging. Regular reliability assessments and stress tests are also critical to ensure long-term performance.
Future Trends in Wafer-Level Packaging
Emerging Applications
Wafer-level packaging (WLP) is increasingly being adopted in various emerging applications, including the Internet of Things (IoT), wearable devices, and automotive electronics. These applications benefit from the miniaturization of devices and enhanced performance that WLP offers. As technology advances, we can expect to see even more innovative uses for WLP in fields such as healthcare and augmented reality.
Market Growth and Projections
The wafer-level packaging market is expected to grow at a rate of 21.0% for the forecast period of 2021 to 2028. This growth is driven by the impending need for circuit miniaturization in microelectronic devices. The global interposer and fan-out wafer level packaging (FOWLP) market size is expected to increase at an impressive rate. This market, which is expected to see significant advancements, will play a crucial role in shaping the future of semiconductor packaging.
Technological Roadmap
The future of WLP will likely see advancements in 2.5D and 3D packaging technologies. These advanced semiconductor packaging technology trends will enable higher performance and greater integration of multiple dies. Additionally, innovations in materials and processes will further enhance the capabilities of WLP, making it a key technology in the semiconductor industry.
Impact of Wafer-Level Packaging on Semiconductor Industry
Performance Improvements
Wafer-Level Packaging (WLP) has significantly enhanced the performance of semiconductor devices. By reducing the distance that electrical signals must travel, WLP minimizes signal loss and improves speed. This results in faster and more efficient devices, which is crucial for applications requiring high performance.
Miniaturization of Devices
One of the most notable impacts of WLP is the miniaturization of electronic devices. The technology allows for more components to be packed into a smaller space, which is essential for modern gadgets like smartphones and wearables. This trend towards circuit miniaturization is driving the demand for WLP.
Economic Implications
The adoption of WLP has significant economic implications for the semiconductor industry. It enables cost-effective manufacturing by reducing material usage and simplifying the assembly process. Additionally, the market for wafer-level packaging is expected to grow at a rate of 21.0% from 2021 to 2028, highlighting its economic potential.
Aspect | Impact |
---|---|
Performance | Enhanced speed and efficiency |
Size | Miniaturization of devices |
Economics | Cost-effective manufacturing and market growth |
The new center for advanced wafer-level packaging applications and development will expand domestic semiconductor manufacturing and drive advancements in the field.
Conclusion
The advancements in wafer-level packaging (WLP) technology have revolutionized the semiconductor industry, enabling the production of smaller, more efficient, and higher-performing electronic devices. By integrating multiple dies into monolithic systems and evolving into advanced forms like Fan-Out Wafer-Level Packaging (FOWLP) and Fan-In Wafer-Level Packaging (FIWLP), WLP continues to address the limitations of traditional packaging methods. As the demand for cost-effective performance in high-end applications grows, the industry is poised to meet these challenges through continuous innovation. Companies like Brewer Science are at the forefront of this evolution, anticipating future technological needs and paving the way for the next generation of semiconductor solutions. The future of wafer-level packaging is bright, promising further miniaturization, streamlined manufacturing processes, and enhanced chip functionality.
Frequently Asked Questions
What is Wafer-Level Packaging (WLP)?
Wafer-level packaging is the technology of packaging the die while it is still on the wafer. Protective layers and electrical connections are added to the substrate before dicing, unlike traditional methods where wafers are diced into individual chips before packaging.
How does Wafer-Level Packaging differ from traditional packaging?
In traditional packaging, the wafer is diced into individual chips which are then packaged. In wafer-level packaging, the die is packaged while still on the wafer, which streamlines manufacturing and allows for smaller package sizes.
What are the benefits of Wafer-Level Packaging?
Wafer-level packaging allows for reduced chip size, streamlined manufacturing processes, and easier testing of chip functionality. It also addresses limitations in the number of I/O connections through advanced methods like FOWLP and FIWLP.
What are the key technologies in Wafer-Level Packaging?
Key technologies include Fan-Out Wafer-Level Packaging (FOWLP), Fan-In Wafer-Level Packaging (FIWLP), and Wafer-Level Chip-Scale Packaging (WLCSP). Each of these technologies offers different benefits and addresses specific challenges in chip packaging.
What innovations are driving advancements in Wafer-Level Packaging?
Innovations such as the integration of multiple dies into monolithic systems, advanced interposer and substrate techniques, and heterogeneous integration are driving advancements in wafer-level packaging.
What are the challenges and solutions in Wafer-Level Packaging?
Challenges include addressing I/O limitations, cost-effective manufacturing, and ensuring testing and reliability. Solutions involve continuous innovation in packaging technologies and processes to meet these challenges effectively.