An In-Depth Look at the Wafer Semiconductor Process
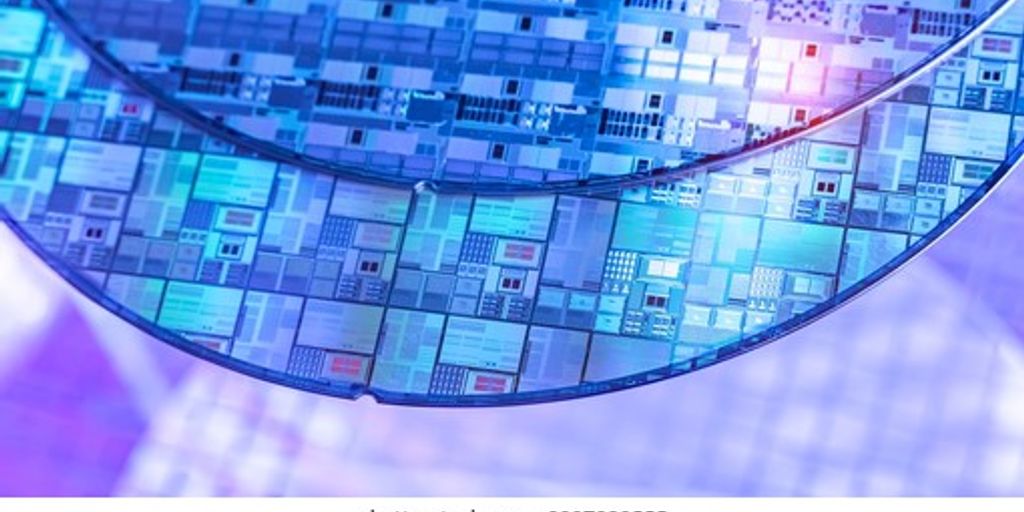
Have you ever wondered how your favorite gadgets are made? The answer lies in the wafer semiconductor process. This is the journey from raw materials to the tiny microchips that power our devices. Let’s dive into the steps and techniques involved in this fascinating process.
Key Takeaways
- The wafer semiconductor process starts with creating a silicon ingot and ends with testing and quality control.
- Defect-free wafers are crucial for the proper functioning of semiconductor devices.
- Front-end wafer processing includes steps like oxidation, lithography, etching, and doping.
- Wafer backgrinding and thinning are important for making the wafers thin enough for modern devices.
- Future trends in wafer semiconductor processes include new technologies and sustainable practices.
The Basics of Wafer Semiconductor Process
Understanding Silicon Wafers
Silicon wafers are the foundation of semiconductor manufacturing. These thin, flat discs are made from high-purity single-crystal silicon. They provide the necessary electrical properties for electronic devices. The quality of these wafers directly impacts the performance and reliability of the final product.
Key Materials Used in Wafer Fabrication
The wafer manufacturing process is intricate and includes various additional steps, such as ingot growth, slicing, edge grinding, and lapping. High-purity silicon is the primary material used, but other materials like silicon carbide and gallium arsenide are also important.
Importance of Defect-Free Wafers
Any defects in the wafers can cause the semiconductor to malfunction. Therefore, wafers must be very thin and very smooth, with no defects. This ensures that the electronic components built on them function correctly.
Steps Involved in Wafer Manufacturing
Creating the Silicon Ingot
The wafer manufacturing process begins with the creation of a silicon ingot. This involves melting silicon and then slowly cooling it. The cooling process must be carefully controlled to ensure the silicon forms correctly. Any defects in this step can cause the semiconductor to malfunction.
Slicing and Polishing the Wafer
Once the silicon ingot is ready, it is sliced into thin wafers. These wafers are then polished to create a smooth surface. The wafers must be very thin and smooth, with no defects, as any imperfections can lead to issues in later stages.
Epitaxial Layer Deposition
In this step, a thin layer of silicon is deposited onto the wafer. This layer is crucial for the subsequent steps in the wafer fabrication process. The wafer fabrication process involves a series of meticulous and controlled steps, including photolithography, etching, doping, and thin film deposition.
Front-End Wafer Processing Techniques
Front-end wafer processing, also known as wafer processing (also called front end), is a critical stage in semiconductor device fabrication. This stage involves several key techniques that transform a simple silicon wafer into a complex platform for electronic components.
Oxidation and Lithography
Oxidation and lithography are foundational steps in wafer processing. Oxidation involves growing a thin layer of silicon dioxide on the wafer’s surface, which acts as an insulator. Lithography uses light to transfer intricate circuit patterns onto the wafer, ensuring high precision and quality in the final product.
Etching and Doping
Etching is the process of removing specific areas of material from the wafer to create the desired patterns. Doping involves adding impurities to the silicon to change its electrical properties. Both steps are crucial for defining the electronic pathways on the wafer.
Metallization and Planarization
Metallization involves depositing metal layers onto the wafer to form electrical connections between different components. Planarization is the process of smoothing the wafer’s surface to ensure uniformity and prevent defects. These steps are essential for creating reliable and efficient semiconductor devices.
Wafer Backgrinding and Thinning
Purpose of Wafer Thinning
Wafer backgrinding, also known as wafer thinning, is a crucial step in making semiconductors. This process ensures that only the proper amount of material is removed. Thinner wafers are important for creating smaller, lighter, and more power-efficient devices like smartphones and wearables. By reducing the wafer’s thickness, manufacturers can improve the final device’s performance and form factor.
Techniques for Backgrinding
The main method for wafer thinning is backgrinding. This involves mechanically grinding the backside of the wafer. The process includes several steps:
- Wafer Mounting: The wafer is mounted on a grinding chuck using a special adhesive.
- Grinding: A grinding wheel is used to remove material from the backside of the wafer.
- Quality Control: The wafer is inspected to ensure the correct thickness and surface quality.
Challenges in Wafer Thinning
There are several challenges in wafer thinning, such as wafer breakage and surface damage. To minimize these issues, manufacturers must carefully select the grinding wheel and optimize grinding parameters. Addressing these challenges is essential for producing high-quality, ultra-thin wafers used in compact electronic devices.
Evolution of Wafer Fabrication Technology
The wafer fabrication process has seen remarkable changes over the years. Since its inception, the process has evolved significantly, incorporating new technologies and methods to enhance efficiency and performance. These advancements have paved the way for the creation of more powerful and sophisticated integrated circuits (ICs).
Dicing and Assembly of Semiconductor Devices
Process of Dicing Wafers
After testing, wafers are sliced into individual chips in a process called dicing. This is usually done with a precision diamond saw that cuts along the lines between the dies. Accurate dicing is crucial to ensure the chips are not damaged, as this can affect their performance and reliability.
Assembly of Individual Chips
Once diced, each chip is mounted into a protective package. This package provides a safe environment for the chip and helps connect it to the outside world. The packaging methods can vary widely depending on the application and the balance between cost and performance.
Testing and Quality Control
After assembly, the chips undergo rigorous testing to ensure they meet quality standards. Nonfunctional chips are marked and discarded. This step is vital to guarantee that only high-quality semiconductor devices reach the market.
Future Trends in Wafer Semiconductor Process
Emerging Technologies
The semiconductor industry is always changing, driven by the need for faster, smaller, and more energy-efficient devices. New technologies are constantly being developed to meet these demands. Some of the most exciting advancements include quantum computing, advanced AI chips, and 3D stacking of semiconductor devices. These innovations promise to revolutionize the way we think about and use technology.
Sustainability in Wafer Fabrication
As the world becomes more aware of environmental issues, the semiconductor industry is also focusing on sustainability. Companies are working on reducing waste, using less energy, and finding eco-friendly materials. This not only helps the planet but can also lower costs in the long run. Efforts include recycling water used in the fabrication process and developing biodegradable materials for certain components.
Future Challenges and Opportunities
While there are many exciting advancements, there are also challenges to overcome. One major issue is the increasing complexity of semiconductor devices, which makes manufacturing more difficult and expensive. However, this also opens up opportunities for innovation. Companies that can find ways to simplify the process or make it more cost-effective will have a significant advantage. Another challenge is the global supply chain, which can be disrupted by political or economic issues. Finding ways to make the supply chain more resilient will be crucial for future success.
Conclusion
The wafer semiconductor process is a fascinating journey from raw silicon to the tiny chips that power our everyday devices. This complex process, involving multiple steps like oxidation, lithography, and etching, requires precision and skill. Understanding this process helps us appreciate the incredible technology behind our smartphones, computers, and other gadgets. As technology continues to advance, the methods and materials used in wafer fabrication will keep evolving, leading to even more powerful and efficient electronic devices. By learning about this process, we gain a deeper appreciation for the innovation and hard work that goes into making the modern world possible.
Frequently Asked Questions
What is a silicon wafer?
A silicon wafer is a thin slice of silicon that serves as the base for building electronic circuits. It’s used in making microchips and other semiconductor devices.
Why are defect-free wafers important?
Defect-free wafers are crucial because any imperfection can cause the semiconductor device to fail, affecting its performance and reliability.
How is a silicon ingot created?
A silicon ingot is made by melting silicon and then cooling it slowly in a controlled manner to form a solid, cylindrical piece of silicon.
What is wafer thinning?
Wafer thinning, also known as backgrinding, is the process of making wafers thinner to meet the demands for smaller and more efficient electronic devices.
What is photolithography?
Photolithography is a process used to transfer patterns onto the wafer’s surface. It involves using light to create intricate designs needed for electronic circuits.
How has wafer fabrication technology evolved?
Wafer fabrication technology has advanced through the use of larger wafers, better photolithography techniques, and new materials, leading to more powerful and efficient electronic devices.