The Importance of Wafer Reliability Tests in Semiconductor Production
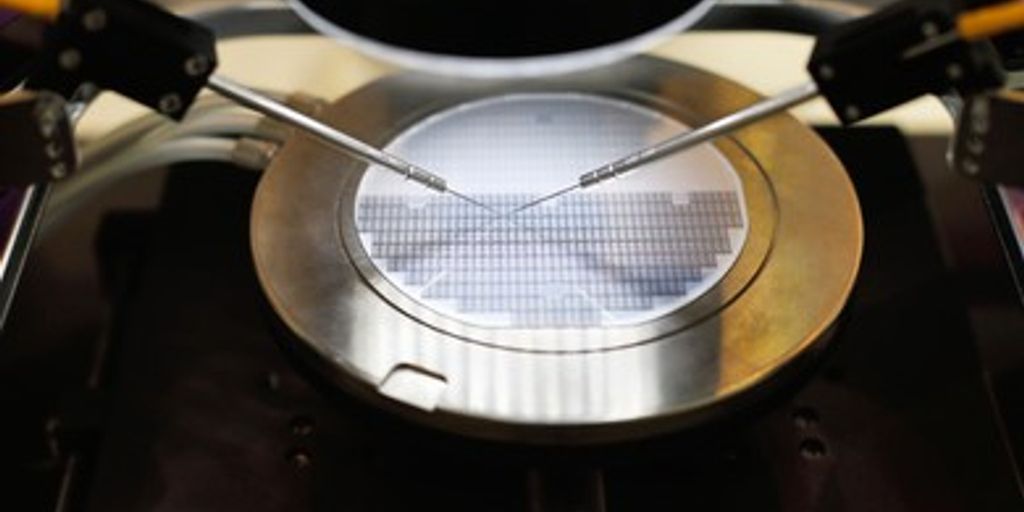
In semiconductor manufacturing, making sure wafers are reliable is super important. Wafer reliability tests check how long and how well semiconductor devices will work under different conditions. These tests are a key part of the manufacturing process. They help find and fix problems early, which means better products in the end. By including these tests, companies can make sure they are delivering high-quality products, which builds trust with customers.
Key Takeaways
- Wafer reliability tests are essential for predicting the lifespan and performance of semiconductor devices.
- These tests help identify and fix defects early in the manufacturing process.
- Reliability tests ensure consistent quality, which is crucial for building customer trust.
- Using best practices in testing, like thorough procedures and accurate data analysis, leads to better products.
- New technologies, such as automation, are making wafer reliability testing faster and more reliable.
The Role of Wafer Reliability Tests in Semiconductor Manufacturing
Wafer reliability tests are essential in the semiconductor manufacturing process. These tests help predict how long devices will last and how well they will perform under different conditions. By understanding how wafers will act in real-world situations, manufacturers can ensure their products work well for a long time.
Predicting Lifespan and Performance
Wafer reliability tests are crucial for predicting the lifespan and performance of semiconductor devices. By simulating different conditions, manufacturers can foresee potential issues and address them early. This proactive approach helps in enhancing the overall quality and durability of the products.
Identifying and Fixing Defects Early
One of the main benefits of wafer reliability tests is the early identification and rectification of defects. This represents a transformative step in the evolution of test wafers, allowing manufacturers to fix problems before they escalate. Early detection not only saves time and resources but also ensures that the final product is free from defects.
Ensuring Consistent Quality
Consistency in quality is paramount in semiconductor manufacturing. Wafer reliability tests play a significant role in maintaining this consistency. By regularly conducting these tests, manufacturers can monitor and control the production process, ensuring that each wafer meets the required standards. This continuous monitoring helps in delivering high-quality products consistently.
Building Customer Trust Through Wafer Reliability Tests
Guaranteeing High-Quality Products
Wafer reliability tests are essential in the semiconductor industry value chain. By ensuring that semiconductor devices are reliable and perform well in different situations, manufacturers show they care about quality. This means the final products are less likely to fail, giving customers peace of mind and steady performance over time.
Providing Peace of Mind
When manufacturers do thorough testing, customers know the products are reliable. This builds trust and improves the company’s reputation. Reliable wafer tests guarantee that the products will work as expected. This assurance is crucial for customers who depend on these products for their own applications.
Enhancing Customer Confidence
By detecting and fixing issues early, manufacturers can ensure that their products are dependable, which in turn enhances customer satisfaction and trust. High-quality wafer testing builds customer trust and improves market reputation. Good testing practices include thorough procedures, accurate data analysis, and ongoing improvements.
Best Practices in Wafer Reliability Testing
Thorough Testing Procedures
To ensure the highest standards, it’s important to follow detailed testing steps. These steps should cover everything from the first material check to the final product test. This careful approach helps find potential problems early, making sure only the best wafers move forward.
Accurate Data Analysis
Understanding the test data correctly is key. Accurate data interpretation helps in making the right decisions about the wafers. This means looking at the data closely and understanding what it tells about the wafer’s quality and performance.
Ongoing Improvements
Always look for ways to make the testing process better. This could mean using new tools or methods to improve accuracy and reliability. By continuously improving, manufacturers can keep up with new challenges and ensure their products are top-notch.
Technological Advancements in Wafer Reliability Testing
Automation in Testing
As semiconductor devices become smaller and more complex, new testing methods are emerging to keep up. Automation in testing is one of the key advancements, allowing for faster and more accurate results. Automated tools can handle repetitive tasks, reducing human error and increasing efficiency.
Advanced Stress Testing Techniques
Traditional stress-driven methods are now joined by advanced techniques that offer quicker and more precise outcomes. For instance, machine learning algorithms are being used to predict potential failure points more efficiently. This not only speeds up the testing process but also improves the accuracy of the results.
Real-Time Monitoring
Real-time monitoring is another significant advancement. It allows for continuous observation of wafer performance during the testing phase. This helps in identifying issues as they occur, enabling immediate corrective actions. Real-time data collection and analysis ensure that the wafers meet the required standards before moving to the next production stage.
Impact of Wafer Reliability Tests on Market Reputation
Building a Strong Market Presence
Wafer reliability tests are essential for establishing a strong market presence. By ensuring that semiconductor devices are dependable, manufacturers can stand out from the competition. This commitment to quality attracts new customers and helps retain existing ones.
Ensuring Product Reliability
Reliable products are less likely to fail, which means customers can trust them to perform well over time. Wafer reliability tests help predict how long and how well semiconductor devices will work under different conditions. This not only boosts customer confidence but also enhances the manufacturer’s reputation.
Meeting Industry Standards
Meeting industry standards is crucial for any manufacturer. Wafer reliability tests ensure that products comply with these standards, which is vital for market acceptance. By adhering to these standards, companies can avoid potential issues and maintain a good standing in the industry.
Integration of Wafer Reliability Tests in Manufacturing Workflow
Streamlining the Testing Process
Integrating wafer reliability tests into the manufacturing workflow is crucial for maintaining a steady flow of information. This proactive approach to quality control ensures that insights from the tests can be quickly applied, leading to immediate improvements. By embedding these tests into the process, manufacturers can detect issues early and make necessary adjustments on the fly.
Collaborative Efforts Between Teams
Successful integration of wafer reliability tests requires collaboration between different teams. Engineers, quality control specialists, and production managers must work together to ensure that the tests are effectively implemented. This teamwork helps in maintaining a continuous flow of information and enables a proactive approach to quality control.
Continuous Monitoring and Feedback
Continuous monitoring and feedback are essential for the effective integration of wafer reliability tests. By constantly monitoring the results and providing feedback, manufacturers can make ongoing improvements to their processes. This ensures that the final products meet the highest standards of quality and reliability.
Conclusion
In conclusion, wafer reliability tests are essential for making sure semiconductor devices are dependable and long-lasting. These tests help spot and fix issues early, leading to better products. By including these tests in the manufacturing process, companies can ensure their products are top-quality. This not only satisfies customers but also helps the company build a strong reputation in the market. Reliable products mean happy customers and a solid market standing.
Frequently Asked Questions
What are wafer reliability tests?
Wafer reliability tests check how long and how well semiconductor devices will work under different conditions. They help find any problems early.
Why are wafer reliability tests important in manufacturing?
These tests make sure that every wafer meets high standards. This helps catch defects early and ensures the final products are reliable.
How do wafer reliability tests build customer trust?
By ensuring that semiconductor devices are reliable and perform well, these tests show customers that the manufacturer cares about quality. This leads to products that are less likely to fail, giving customers peace of mind.
What are some best practices in wafer reliability testing?
Good practices include thorough testing procedures, accurate data analysis, and ongoing improvements. These steps help ensure that the tests are effective and the products are of high quality.
How has technology improved wafer reliability testing?
New technologies like automation and real-time monitoring have made wafer reliability testing faster and more reliable. Advanced stress testing techniques also help in better predicting the performance of semiconductor devices.
What impact do wafer reliability tests have on market reputation?
Reliable wafer tests help build a strong market presence by ensuring that products meet industry standards and customer expectations. This leads to a better reputation and higher customer confidence.