An Overview of Wafer Components in Modern Electronics
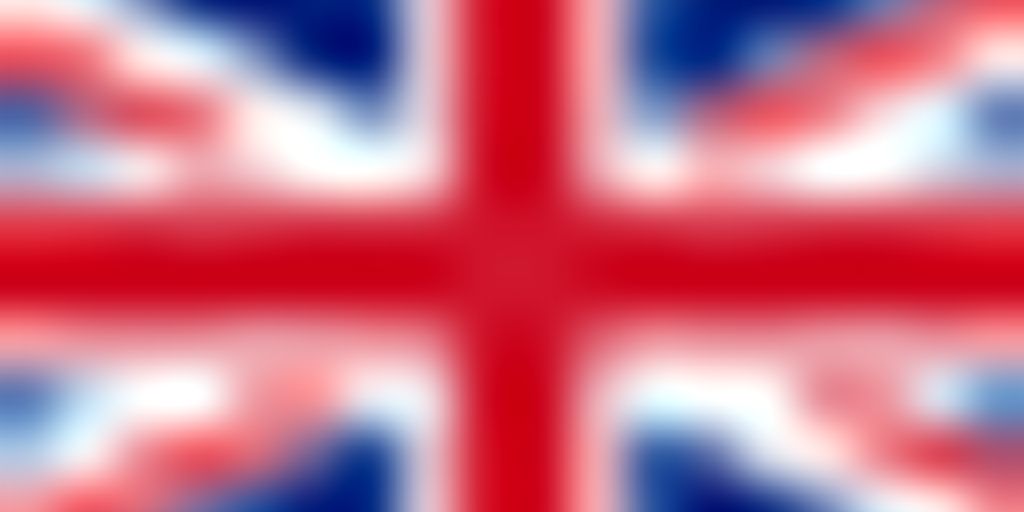
Modern electronics heavily depend on wafer components. These thin slices of material are the backbone of many devices, from smartphones to cars. This article will explore the importance, materials, processes, and future trends in wafer technology.
Key Takeaways
- Wafer components are essential for creating microelectronic devices.
- Silicon is the most commonly used material for wafers.
- Microfabrication processes include doping, etching, and thin-film deposition.
- Photolithography is a key technique in wafer production.
- Wafer technology is continually evolving with new materials and methods.
The Role of Wafer Components in Modern Electronics
Substrate for Microelectronic Devices
Wafer components serve as the foundation for microelectronic devices. They undergo various processes like doping, ion implantation, etching, and thin-film deposition. These steps are crucial for creating the tiny circuits that power our gadgets.
Foundation for Integrated Circuits
In the semiconductor industry, wafers are the base for integrated circuits (ICs). These ICs are essential for modern electronics, enabling compact designs and enhanced functionality in devices like smartphones and computers.
Importance in Semiconductor Manufacturing
Wafers are vital in semiconductor manufacturing. They are used to make microchips, which act as the brains of electronic devices. From smartphones to airplanes, almost every electronic device relies on these advanced IC chips.
Key Materials Used in Wafer Components
Silicon Wafers
Silicon is the most common material used for wafers in the electronics industry. It can withstand high temperatures, is abundant, and has the right semiconductor properties. Silicon wafers serve as the foundation for integrated circuits and semiconductor devices.
Compound Semiconductors
Other materials used in wafer manufacturing include Silicon Germanium (SiGe), Sapphire (Al2O3), Gallium Arsenide (GaAs), Gallium Nitride (GaN), Diamond, Zinc Oxide (ZnO), Silicon Carbide (SiC), and Indium Phosphide (InP). These materials are chosen based on the specific needs of the semiconductor device being produced.
Emerging Materials
New materials are being explored for wafer production to meet the demands of advanced technologies. These emerging materials aim to improve performance, efficiency, and sustainability in semiconductor device fabrication.
Microfabrication Processes for Wafer Components
Microfabrication is the process of creating tiny structures on a very small scale. This process is essential for making modern electronics. It involves several steps to turn a simple wafer into a complex integrated circuit (IC).
Photolithographic Patterning in Wafer Production
Basics of Photolithography
Photolithography is a crucial step in creating the tiny patterns on semiconductor devices. It starts by coating the wafer with a light-sensitive material called photoresist. A mask, which acts like a stencil, is placed over the wafer. Ultraviolet light is then shone onto the wafer, hardening the photoresist in the shape of the circuit design. The areas not exposed to light stay soft and can be washed away, leaving the desired pattern.
Advanced Patterning Techniques
As technology advances, so do the methods for photolithography. Techniques like extreme ultraviolet (EUV) lithography allow for even smaller and more precise patterns. Multiple patterning methods, such as double and quadruple patterning, are also used to achieve the fine details needed for modern electronics. These advanced techniques help in pushing the limits of how small and efficient devices can be.
Challenges and Solutions
Photolithography faces several challenges, including the need for extreme precision and the limitations of light wavelengths. One major issue is the diffraction limit, which makes it hard to create very small features. Solutions like using shorter wavelengths of light and improving mask design are being developed to overcome these hurdles. Additionally, new materials and better photoresists are being researched to enhance the process.
Wafer Dicing and Packaging
Dicing Methods
Wafer dicing involves slicing a wafer containing thousands of elements into small pieces, known as dies. Advanced processes can pack over a thousand dies onto a single 300mm wafer! The whole wafer is processed as a unit, but the goal is to separate and package these individual dies. Laser dicing is popular due to its superior precision.
Packaging Technologies
After dicing, the dies are placed onto a package or substrate in a process called die bonding. This step uses materials like Ag paste to affix the dies. Next, wire bonding connects the die to the external package or substrate using heat, pressure, and ultrasonic energy. This ensures the dies are securely attached and ready for integration into devices.
Impact on Device Performance
The quality of dicing and packaging directly affects device performance. Properly diced and packaged dies ensure reliable and efficient operation of the final integrated circuits (ICs). These ICs are then used in various electronics, from consumer gadgets to automotive systems.
Applications of Wafer Components in Various Industries
Consumer Electronics
Wafer components are essential in the consumer electronics industry. They are used to create microchips and sensors found in everyday devices like smartphones, tablets, and laptops. These components help make devices smaller and more efficient. The advancements in wafer materials, such as silicon, have significantly contributed to the development of modern technology.
Automotive Industry
In the automotive industry, wafer components play a crucial role in the production of various electronic systems. These include engine control units, infotainment systems, and advanced driver-assistance systems (ADAS). The use of semiconductor wafers ensures that these systems are reliable and perform well under different conditions.
Medical Devices
Wafer components are also vital in the medical field. They are used in the manufacturing of medical devices such as diagnostic equipment, imaging systems, and wearable health monitors. The high precision and reliability of semiconductor wafers make them ideal for use in critical medical applications.
Future Trends in Wafer Component Technology
Miniaturization and Efficiency
The semiconductor industry continues to find ways to pack more devices into smaller spaces on chips. This trend of miniaturization is crucial for enhancing the efficiency and performance of electronic devices. As we approach the physical and economic limits of current technologies, innovative solutions like multi-bridge channel FETs and carbon nanotube integration are becoming essential.
Integration with Emerging Technologies
Emerging technologies such as quantum computing and artificial intelligence are driving the need for advanced wafer components. These technologies require wafers that can support higher processing speeds and greater connectivity. Recent breakthroughs, like the integration of graphene with standard production methods, are paving the way for these advancements.
Sustainability and Environmental Impact
As the demand for electronic devices grows, so does the need for sustainable manufacturing practices. The future of wafer technology will likely focus on reducing waste and energy consumption. Efforts to improve the efficiency of production processes and the recyclability of materials are key to minimizing the environmental impact of wafer manufacturing.
Conclusion
In conclusion, semiconductor wafers are the unsung heroes of modern electronics. These thin slices of material are the foundation for the microchips that power everything from our smartphones to advanced medical devices. Understanding the role and processing of wafers helps us appreciate the complexity and precision involved in creating the technology we rely on every day. As technology continues to advance, the importance of these tiny but mighty components will only grow, driving innovation and shaping the future of electronics.
Frequently Asked Questions
What is a wafer in electronics?
A wafer in electronics is a thin slice of semiconductor material, like silicon, used to build microelectronic devices and integrated circuits.
Why is silicon commonly used for wafers?
Silicon is used because it is abundant, has excellent electrical properties, and can be easily manufactured into wafers.
What are compound semiconductors?
Compound semiconductors are materials made from two or more elements, like gallium arsenide, and are used for specialized electronic applications.
How are wafers made?
Wafers are made through processes like doping, ion implantation, etching, and thin-film deposition, followed by photolithographic patterning and dicing.
What is photolithography?
Photolithography is a process used to pattern parts of a wafer, which involves using light to transfer a geometric pattern from a photomask to a light-sensitive chemical photoresist on the wafer.
Why are wafers important in modern electronics?
Wafers are crucial because they serve as the foundation for microchips, which power everything from computers and smartphones to medical devices and cars.