Ensuring Quality with Wafer Level Reliability Testing
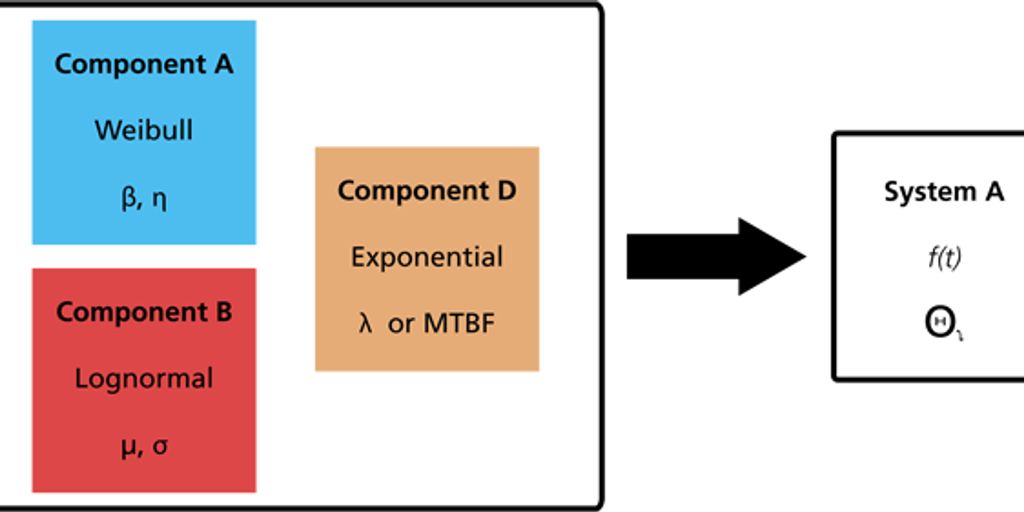
In the fast-paced world of semiconductor manufacturing, ensuring the durability of wafers is paramount. Wafer reliability testing plays a critical role in identifying potential failures and enhancing the longevity of electronic devices. This article delves into the various methods and strategies employed in wafer reliability testing, highlighting the importance of rigorous analysis and optimization to overcome the challenges faced in wafer-level packaging.
Key Takeaways
- Wafer Level Reliability Testing (WLRT) is essential for assessing the long-term durability and performance of semiconductor devices under various stress conditions.
- Advanced techniques such as thermal cycling analysis, finite element modeling, and warpage simulation are crucial for predicting and mitigating potential failures.
- Addressing challenges like structural failures, electromigration, and signal transmission crosstalk requires a multifaceted and analytical approach.
- Real-world case studies, such as those involving 28nm technology FPGA and TSV interposers, underscore the importance of comprehensive reliability testing.
- Integration of WLRT into the manufacturing workflow, including automated defect classification, is vital for ensuring consistent quality and reliability.
Understanding Wafer Level Reliability Testing
Wafer-level reliability testing (WLRT) is conducted to simulate the operational conditions that a semiconductor device might encounter during its lifespan. This includes exposure to temperature extremes, voltage stress, and other environmental factors. WLRT helps assess the long-term reliability and durability of the semiconductor, ensuring it meets stringent quality standards.
Methods and Techniques in Wafer Level Reliability Testing
Wafer level reliability testing (WLRT) is essential for ensuring the long-term reliability and durability of semiconductor devices. This section delves into the primary methods and techniques used in WLRT, each addressing different aspects of potential failures and performance issues.
Thermal Cycling Analysis
Thermal cycling analysis is a critical method used to simulate the operational conditions that a semiconductor device might encounter during its lifespan. This includes exposure to temperature extremes, which helps in assessing the device’s ability to withstand thermal stress and prevent structural failures.
Finite Element Modeling
Finite element modeling (FEM) is an analytical technique used to predict how a device will react to various physical forces. By creating a detailed simulation, FEM helps in understanding the mechanical behavior of the wafer under different conditions, thereby aiding in the design of more reliable semiconductor devices.
Warpage Simulation
Warpage simulation is used to predict and analyze the deformation of wafers during the manufacturing process. This technique is crucial for identifying potential issues related to mechanical stress and ensuring that the wafers remain flat and functional throughout their lifecycle.
Challenges in Wafer Level Reliability Testing
Wafer reliability testing is a critical component in the semiconductor manufacturing process, ensuring the longevity and performance of electronic devices. Throughout this section, we will explore the multifaceted challenges of structural failures, electromigration, and signal transmission crosstalk. The journey from raw materials to a finished semiconductor device is fraught with challenges, making the rigorous evaluation of wafers critical.
Real-World Applications and Case Studies
28nm Technology FPGA Study
In semiconductor manufacturing, case studies demonstrate the impact of best practices in wafer testing. One notable example is the 28nm Technology FPGA Study, which highlights the importance of advanced testing methodologies in ensuring device reliability. This study focuses on the challenges and solutions associated with testing at such a fine scale, providing valuable insights for future developments.
TSV Interposers and Interconnects
As the industry approaches the limits of Moore’s Law, advancements in interconnect technologies like Through-Silicon Vias (TSVs) are vital. This case study explores the reliability challenges and solutions in TSV interposers and interconnects, emphasizing their role in high-performance, miniaturized electronic devices. The ongoing development and refinement of these technologies will play a significant role in the future of electronic packaging.
Multi-Field Coupling Reliability
Another case study involves Nikon Metrology Inc., which illustrates the application of advanced optical technology in the semiconductor industry. Nikon’s camera and optics technology has been utilized for various applied research tasks, including inspecting and quality-controlling semiconductor wafers. This case study underscores the precision and efficiency of modern optical technologies in enhancing wafer reliability.
Optimizing Wafer Level Reliability Testing
Design Approaches for Thermo-Mechanical Reliability
To ensure the longevity and performance of electronic devices, it is crucial to adopt design approaches for thermo-mechanical reliability. These approaches focus on minimizing the impact of thermal and mechanical stresses on semiconductor wafers. By optimizing the design, manufacturers can significantly reduce the risk of structural failures and enhance the overall reliability of the wafers.
Process-Induced Stress Suppression
Process-induced stress is a common issue in semiconductor manufacturing. Implementing strategies to suppress these stresses can lead to improved wafer durability. Techniques such as adjusting process parameters and using stress-relief materials are effective in mitigating the adverse effects of process-induced stress.
Performance Optimization Strategies
Performance optimization is essential for achieving high reliability in wafer-level packaging. This involves a combination of rigorous analysis and optimization to identify potential failures and enhance the longevity of electronic devices. Key strategies include:
- Conducting thorough thermal cycling analysis
- Utilizing finite element modeling for stress prediction
- Implementing warpage simulation to assess structural integrity
By integrating these strategies, manufacturers can ensure the wafers meet the required reliability standards.
Integration of Wafer Level Reliability Testing in Manufacturing
Integrating wafer test analysis with the overall semiconductor manufacturing workflow is essential. This ensures that the insights gained from the analysis can be promptly and effectively implemented, leading to immediate improvements in the manufacturing process. The integration also helps in maintaining a continuous flow of information, enabling a proactive approach to quality control.
Automated defect classification systems play a crucial role in wafer level reliability testing. These systems use advanced algorithms and machine learning techniques to identify and categorize defects quickly and accurately. This automation significantly reduces the time and effort required for manual inspection, allowing for faster turnaround times and higher throughput.
Ensuring the long-term reliability of semiconductor devices is paramount. Reliability testing involves subjecting the wafers to various stress conditions and predicting their lifespan and performance under different scenarios. This practice helps in guaranteeing that the semiconductors will perform reliably in real-world conditions.
Future Trends in Wafer Level Reliability Testing
Advancements in Testing Technologies
The semiconductor industry is rapidly evolving, and advancements in testing technologies are crucial for improving wafer durability. Emerging trends like fan-out technologies, 3D IC memory interfaces, and advancements in wirebonding significantly impact wafer reliability testing methodologies. These advancements enable more precise and comprehensive testing, ensuring higher reliability and performance of semiconductor devices.
Emerging Challenges
As the complexity of semiconductor devices increases, new challenges in wafer level reliability testing arise. The focus is shifting towards multi-field coupling analysis and optimization of reliability for emerging packaging technologies. With advancements such as 2.5D and 3D packaging, and wafer-level packaging (WLP), the complexity of physical fields and the associated reliability concerns are increasing. Addressing these challenges requires innovative approaches and continuous research.
Predictions for the Industry
The future of wafer level reliability testing is poised to address new challenges and leverage emerging technologies. Key predictions for the industry include:
- Increased adoption of automated defect classification systems to enhance testing efficiency.
- Greater integration of reliability assurance processes within the manufacturing workflow.
- Continued focus on optimizing thermo-mechanical reliability and suppressing process-induced stress.
- Expansion of case studies and real-world applications to provide valuable insights for future research.
These trends and predictions highlight the dynamic nature of wafer level reliability testing and its critical role in the semiconductor industry’s future.
Conclusion
In summary, wafer reliability testing is a critical component in the semiconductor manufacturing process, ensuring the longevity and performance of electronic devices. Throughout this article, we have explored various methods and strategies, from thermal cycling analysis to finite element modeling, to address the multifaceted challenges of structural failures, electromigration, and signal transmission crosstalk. The research and case studies presented underscore the importance of a multi-field approach to wafer level reliability testing. As semiconductor devices continue to shrink in size and increase in complexity, the necessity for comprehensive and rigorous testing methodologies becomes even more paramount. By implementing advanced wafer level reliability testing techniques, semiconductor fabrication facilities can significantly enhance the quality, reliability, and performance of their products, ultimately leading to greater consumer satisfaction and technological advancement.
Frequently Asked Questions
What is wafer level reliability testing?
Wafer level reliability testing (WLRT) is a methodology used in semiconductor manufacturing to simulate the operational conditions a semiconductor device might encounter during its lifespan. This includes exposure to temperature extremes, voltage stress, and other environmental factors to assess the long-term reliability and durability of the semiconductor.
Why is wafer level reliability testing important in semiconductor manufacturing?
Wafer level reliability testing is crucial because it ensures the longevity and performance of electronic devices. By identifying potential failures early, it helps in enhancing the durability of the devices and ensures they meet stringent quality standards.
What are some common methods used in wafer level reliability testing?
Common methods include thermal cycling analysis, finite element modeling, and warpage simulation. These techniques help in evaluating the reliability of wafers by simulating various stress conditions and predicting potential failures.
What challenges are addressed by wafer level reliability testing?
Wafer level reliability testing addresses several challenges such as structural failures, electromigration issues, and signal transmission crosstalk. These challenges can significantly impact the performance and reliability of semiconductor devices if not properly managed.
How is wafer level reliability testing integrated into the manufacturing workflow?
Wafer level reliability testing is integrated into the manufacturing workflow through automated defect classification, workflow integration, and reliability assurance processes. These steps help in detecting and eliminating wafers with structural or material flaws, ensuring the dependability of the finished products.
What are the future trends in wafer level reliability testing?
Future trends in wafer level reliability testing include advancements in testing technologies, emerging challenges related to newer semiconductor materials and designs, and predictions for more sophisticated and accurate reliability assessment methods.