Exploring the Benefits of Wafer Level Package Solutions
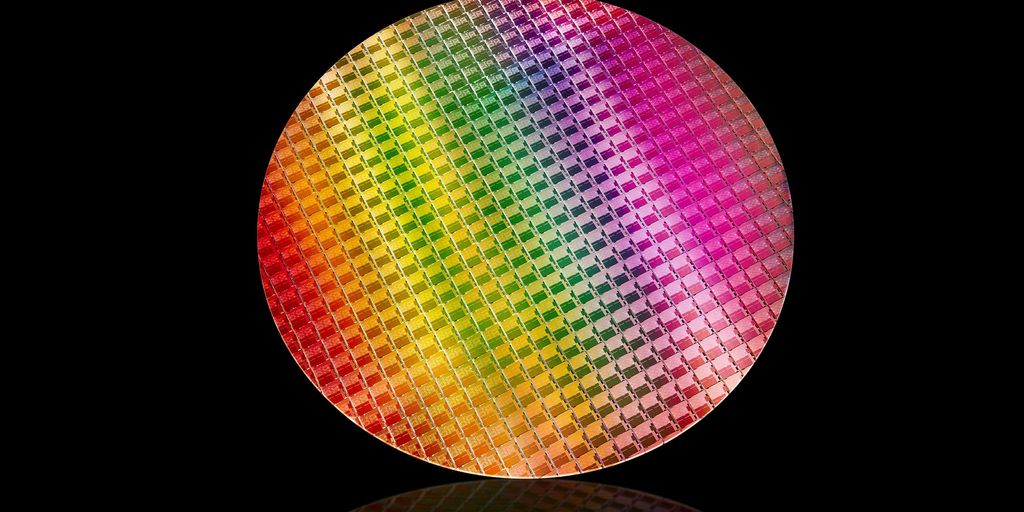
Wafer Level Packaging (WLP) is a cutting-edge method in the world of electronics. It merges the benefits of flip chip and traditional surface mount technologies. Over the past few years, WLP has seen a significant rise in use, both in the number of products and the quantities produced. However, like any technology, it faces its own set of challenges, particularly in terms of reliability at different levels.
Key Takeaways
- Wafer Level Packaging combines the best of flip chip and surface mount technologies.
- WLP is increasingly used in various products, showing significant growth in recent years.
- The technology helps reduce power consumption and improve reliability in electronic devices.
- Despite its advantages, WLP faces challenges like size limitations and reliability issues.
- Future trends in WLP include emerging technologies and innovations in materials.
Understanding Wafer Level Packaging Technology
Key Components of Wafer Level Packaging
Wafer Level Packaging (WLP) involves packaging the wafer directly after the front-end process is completed. This method contrasts with traditional IC packaging, where the wafer is first diced into individual chips and then packaged. WLP technology offers significant advantages in terms of cost and production efficiency. Key components include redistribution layers, passivation layers, and solder bumps.
How Wafer Level Packaging Differs from Traditional Methods
In traditional methods, wafers are diced into individual chips before packaging. In WLP, most or all packaging steps are performed at the wafer level, only dicing the wafer into individual chips at the end. This approach reduces handling and increases throughput, making it a more efficient process.
Evolution of Wafer Level Packaging
WLP has evolved significantly over the years. Initially, it was used for simple applications, but advancements in technology have expanded its use to more complex and high-performance devices. The integration of flip chip and surface mount technologies has further enhanced its capabilities, making it a preferred choice in various industries.
Advantages of Wafer Level Packaging
Reduced Power Consumption
Wafer level packaging (WLP) is known for its ability to reduce power consumption in electronic devices. By expanding the space available for electrical connections, it allows for better thermal management and improved electrical performance. This means devices can run more efficiently and use less energy.
Enhanced Reliability
One of the key benefits of WLP is its enhanced reliability. The technology minimizes the distance that electrical signals need to travel, which reduces the chances of signal loss or interference. This results in more dependable and longer-lasting electronic products.
Cost-Effectiveness in Manufacturing
WLP is also cost-effective in manufacturing. The process allows for batch manufacturing, which significantly lowers production costs. Additionally, the potential of enabling wafer test and burn-in further reduces expenses by identifying defects early in the production process.
Applications of Wafer Level Packaging
Consumer Electronics
Wafer level packaging (WLP) is widely used in consumer electronics. Its small size and high performance make it ideal for smartphones, tablets, and wearables. These devices benefit from the reduced power consumption and enhanced reliability that WLP offers.
Automotive Industry
In the automotive industry, WLP is crucial for advanced driver-assistance systems (ADAS), infotainment systems, and engine control units. The technology helps in achieving compact designs and robust performance, which are essential for modern vehicles.
Medical Devices
Medical devices also leverage WLP for its precision and reliability. It is used in devices like pacemakers, hearing aids, and diagnostic equipment. The compact size and high reliability of WLP make it suitable for medical applications where space and performance are critical.
Challenges in Wafer Level Packaging
Size Limitations
One of the main challenges in wafer level packaging (WLP) is the size limitation. WLPs are often restricted by the size of the wafer itself, which can limit the overall dimensions of the final package. This can be a significant drawback for applications requiring larger packages.
Reliability Issues
Reliability is another critical concern. WLPs can face first and second-level reliability issues, which can affect the long-term performance of the device. Factors such as thermal cycling, mechanical stress, and environmental conditions can all impact the reliability of WLPs.
Integration Challenges
Integrating multiple chips and components into a single WLP can be complex. This includes challenges like embedding passives, hermetic sealing, and gap filling. These integration issues can complicate the manufacturing process and affect the overall performance of the package.
Future Trends in Wafer Level Packaging
Emerging Technologies
The landscape of packaging technology is undergoing a transformative shift, spearheaded by the revolutionary wafer-level packaging (WLP) approach. This paradigm shift is driven by ingenious thin wafer handling (TWH) technologies that have paved the way for a new era of innovation. The integration of various high-performance materials within WLP has not only facilitated greater throughput and cost efficiency but has also enabled manufacturers to achieve a reduction in form factor.
Market Growth Projections
Wafer level packaging (WLP) has acquired significant interest and focus in the last ten years as the semiconductor industry continues to push for higher performance generation after generation primarily driven by mobile and consumer segments. As Moore’s Law continues to slow down due to increasing difficulty in manufacturing sub 7 nm and below technologies, back-end packaging processes become ever important in addressing the need for low latency, higher bandwidth, and cost-effective semiconductor devices.
Innovations in Materials
Wafer Level Packages are one of the most advanced packaging concepts. It combines the advantages of flip chip with conventional surface mount technologies. In recent years, we have seen a tremendous growth in the application of Wafer Level Packages, both in quantities as well as in the number of products where they are implemented. The technology is, however, not without its challenges with 1st and 2nd level reliability issues. For instance, the limit on the size of Wafer Level Packages has to do with the integration of multichip, chip passives, embedded passives, hermetic sealing on the wafer level, gap filling, and overall long-term reliability.
Wafer Level Packaging vs. Other Packaging Solutions
Comparison with Flip Chip Technology
Wafer Level Packaging (WLP) and Flip Chip Technology are both advanced methods used in semiconductor packaging. WLP combines the benefits of flip chip with traditional surface mount technologies. While Flip Chip offers high performance and reliability, WLP provides additional advantages such as reduced manufacturing costs and the ability to test and burn-in at the wafer level. This makes WLP a preferred choice for many applications, especially in consumer electronics.
Surface Mount Technology vs. Wafer Level Packaging
Surface Mount Technology (SMT) has been a staple in electronics manufacturing for decades. However, WLP offers several improvements over SMT. For instance, WLP allows for smaller package sizes and better electrical performance. Additionally, WLP can be more cost-effective in high-volume production due to its batch manufacturing process. This makes it an attractive option for industries looking to optimize both performance and cost.
Benefits Over Traditional Packaging Methods
Traditional packaging methods, such as wire bonding, have been used for many years but come with limitations like larger package sizes and higher power consumption. WLP addresses these issues by offering smaller, more efficient packages. Moreover, WLP enables higher levels of integration, which is crucial for modern electronic devices. This results in products that are not only more compact but also more reliable and energy-efficient.
Supply Chain Considerations for Wafer Level Packaging
Key Suppliers and Manufacturers
In the world of wafer level packaging, having reliable suppliers and manufacturers is crucial. Companies across the supply chain must have a dedication to quality because at each step, precision is key. Leading suppliers often provide not just materials but also essential technologies and support.
Logistics and Distribution
Efficient logistics and distribution are vital for the success of wafer level packaging. The components, once diced from the wafer, need to be shipped and assembled onto substrates or printed wiring boards (PWBs) using standard surface mount technology (SMT). This process ensures that the final products are ready for the market without delays.
Quality Control and Testing
Quality control and testing are indispensable in reducing risk in the semiconductor supply chain. Advanced packaging methods require rigorous testing to ensure reliability and performance. This step is essential to maintain the high standards expected in the industry.
Conclusion
Wafer Level Packaging (WLP) is a game-changer in the world of electronics. It merges the benefits of flip chip and traditional surface mount technologies, making devices smaller, lighter, and more reliable. Despite some challenges, like size limits and reliability issues, the technology continues to grow. WLP is crucial for the future of electronics, offering low-cost manufacturing and the ability to test wafers early. As we keep pushing the boundaries of technology, WLP will play a key role in developing new, advanced devices.
Frequently Asked Questions
What is Wafer Level Packaging (WLP)?
Wafer Level Packaging (WLP) is a method where the packaging of the wafer is done right after the front-end process is finished. Then, the wafer is cut and separated into individual chips.
What are the main benefits of WLP?
WLP helps in reducing power use and improving reliability. This makes it perfect for making electronic products that are lighter, thinner, smaller, and cheaper.
How does WLP differ from traditional packaging methods?
Unlike traditional methods, WLP packages the wafer as a whole before cutting it into chips. This can save time and cost in manufacturing.
What are the common applications of WLP?
WLP is used in many areas like consumer electronics, cars, and medical devices. It helps make these products smaller and more efficient.
What challenges does WLP face?
WLP has some challenges like size limits, reliability issues, and problems with integrating different parts. These need to be solved for better performance.
What is the future of WLP?
The future looks bright for WLP with new technologies, market growth, and innovations in materials. These will help WLP to become even more efficient and widely used.