How Wafer Level Burn In Test Enhances Semiconductor Reliability
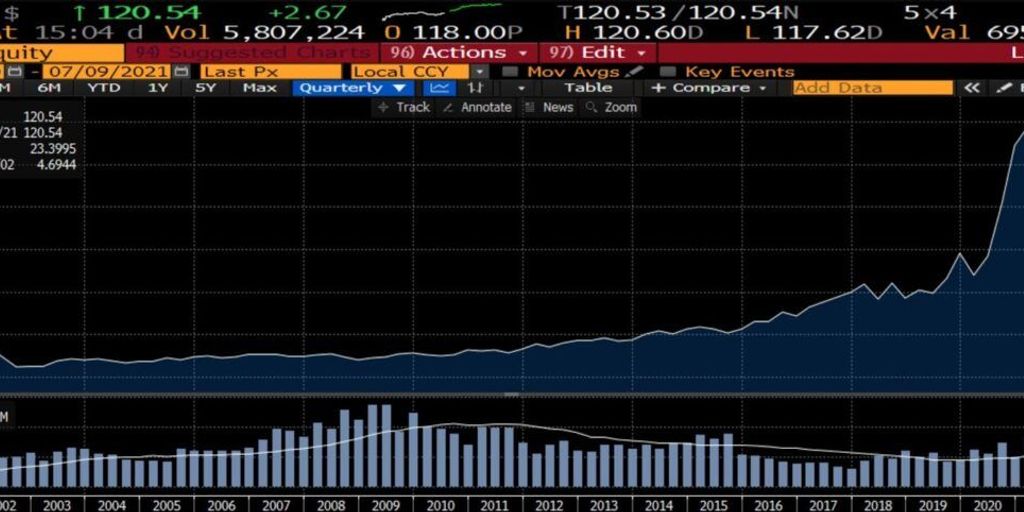
In the rapidly evolving semiconductor industry, ensuring the reliability of integrated circuits is paramount. Wafer Level Burn In (WLBI) testing has emerged as a critical process in semiconductor manufacturing, offering a robust solution to identify and mitigate potential defects at an early stage. This article delves into the significance, benefits, technical aspects, and challenges of WLBI testing, comparing it with traditional methods and exploring its impact on mobile and handheld devices. Additionally, we will discuss how incorporating WLBI testing into quality assurance programs can enhance overall product reliability and customer satisfaction.
Key Takeaways
- Wafer Level Burn In testing is essential for early detection of defects in semiconductor manufacturing, enhancing overall product reliability.
- Implementing WLBI testing can lead to significant cost savings by identifying issues before packaging and reducing the need for extensive post-production testing.
- WLBI testing improves yield analysis by providing detailed insights into defect densities and potential failure mechanisms.
- Despite its benefits, WLBI testing faces challenges such as defect density issues and technological constraints that need to be addressed.
- Incorporating WLBI testing into quality assurance programs can significantly enhance process control, benchmarking, and compliance, leading to higher customer satisfaction.
The Importance of Wafer Level Burn In Test in Semiconductor Manufacturing
Wafer Level Burn In (WLBI) testing is a critical process in semiconductor manufacturing, ensuring the reliability and performance of semiconductor devices. Burn-in testing remains one of the keystones for providing statistically driven confidence to many aspects of semiconductor manufacturing. This process allows manufacturers to identify and eliminate early-life failures, thereby enhancing the overall quality and reliability of the final product.
Key Benefits of Implementing Wafer Level Burn In Test
Enhanced Reliability
Wafer Level Burn In Test (WLBI) significantly enhances the reliability of semiconductor devices. By identifying and segregating potential early high failure rate populations, WLBI ensures that only the most reliable products reach the market. This process is crucial for delivering a statistically more reliable product population to customers.
Cost Efficiency
Implementing WLBI can lead to substantial cost savings. A key feature in their selection of our fox solution is its proven ability to cost-effectively implement their target burn-in and stabilization requirements. By conducting burn-in tests at the wafer level, manufacturers can reduce the costs associated with packaging and testing individual dies, leading to more efficient production processes.
Improved Yield Analysis
WLBI provides valuable data that can be used for yield analysis. This data helps manufacturers understand the performance characteristics of their products and identify any out-of-character performance indicators. Properly designed burn-in testing may be used on the application-specific deliverable components in order to trigger out-of-character performance indicators without weakening properly functioning ones. This information is essential for improving overall yield and ensuring the quality of the final products.
Technical Aspects of Wafer Level Burn In Test
Test Procedures and Protocols
Wafer Level Burn In (WLBI) involves a series of rigorous test procedures designed to identify and eliminate defective semiconductor devices early in the manufacturing process. Burn-in is typically the first test step after assembling the probed and sawed wafer die into packages. The procedures include subjecting the wafers to elevated temperatures and electrical stress to accelerate potential failure mechanisms.
Equipment and Tools
The equipment used in WLBI is specialized and highly advanced. Aehr Test Systems, a Fremont-based supplier of semiconductor test and burn-in equipment, has received an initial customer order for a FOX-NP wafer level system. This system is designed to handle the unique requirements of WLBI, including precise temperature control and high-throughput capabilities.
Data Analysis and Interpretation
Data analysis is a critical component of WLBI. The defect density of the product is measured on every wafer of every lot built as part of functional testing. This data helps in identifying low-yielding wafers or lots, which are likely to show higher defect densities and thus higher product fallout in reliability tests. The insights gained from this analysis are invaluable for improving overall yield and reliability.
Challenges and Limitations of Wafer Level Burn In Test
Defect Density Issues
Wafer-level burn-in tests are typically impacted by random defects due to the fact that the tested element is a product die and thus has much more area than a small WLR structure. Defect density monitoring can therefore be done through yield analysis and does not require burn-in. This means that while wafer-level burn-in can identify early life failures, it may not be necessary for all products, especially those with low defect densities.
Technological Constraints
The implementation of wafer-level burn-in tests requires advanced equipment and tools, which can be a significant investment for manufacturers. Additionally, the complexity of the test procedures and protocols can pose challenges, particularly for smaller companies or those with limited technical expertise. The need for specialized knowledge and equipment can limit the widespread adoption of wafer-level burn-in tests.
Economic Considerations
While wafer-level burn-in tests can enhance reliability and reduce costs in the long run, the initial investment can be substantial. Manufacturers must weigh the benefits against the costs, considering factors such as the volume of production and the specific requirements of their products. For some, the economic burden may outweigh the potential advantages, making traditional burn-in methods more appealing.
Comparing Wafer Level Burn In Test with Traditional Burn In Methods
Efficiency and Accuracy
Wafer Level Burn In (WLBI) tests offer significant improvements in efficiency and accuracy compared to traditional burn-in methods. WLBI allows for the simultaneous testing of multiple dies on a wafer, reducing the time and resources required. Traditional methods, on the other hand, involve testing individual packaged dies, which is more time-consuming and less efficient.
Application-Specific Benefits
WLBI is particularly beneficial for mobile and handheld devices, where space and power efficiency are critical. Traditional burn-in methods may not be as effective in identifying defects in these application-specific scenarios. WLBI can help in early detection of potential issues, ensuring higher reliability and performance.
Case Studies and Examples
Several case studies highlight the advantages of WLBI over traditional methods. For instance, a study on System-on-Chip (SoC) devices showed a 20% improvement in yield and a 15% reduction in testing costs when WLBI was implemented. Another example is in the field of mobile processors, where WLBI helped in identifying defects that traditional methods missed, leading to a 10% increase in overall device reliability.
Impact of Wafer Level Burn In Test on Mobile and Handheld Devices
Wafer Level Burn In (WLBI) testing is becoming increasingly significant for mobile and handheld devices. As these devices continue to evolve, the demand for reliable and high-performing components has surged. In addition to the burn-in test, which contributes to mitigating extrinsic failure rates, various stress tests—including gate stress, high-temperature reverse bias, and others—are employed to ensure the robustness of these devices.
WLBI testing directly impacts the performance metrics of mobile and handheld devices. By identifying and segregating potential early high failure rate populations, manufacturers can deliver a statistically more reliable product population to the market. This process ensures that only components that meet stringent performance criteria make it to the final product, thereby enhancing overall device reliability.
The ultimate goal of implementing WLBI testing in the production of mobile and handheld devices is to improve customer satisfaction. By ensuring that the devices are less prone to early failures and perform consistently well, manufacturers can build trust and loyalty among their customer base. This not only helps in retaining existing customers but also attracts new ones, thereby driving market growth.
Incorporating Wafer Level Burn In Test in Quality Assurance Programs
Incorporating Wafer Level Burn In Test (WLBI) into quality assurance programs is essential for ensuring the reliability and performance of semiconductor devices. The known-good-die (KGD) program for the SiC portfolio is a prime example of how WLBI can be integrated to elevate quality assurance and deliver consistent, repeatable performance of key parameters. This program enables customers to obtain dies that meet stringent quality standards, thereby enhancing overall product reliability.
Conclusion
Wafer Level Burn-In (WLBI) testing is a crucial methodology in enhancing the reliability of semiconductors. By identifying and segregating potential early failures, WLBI ensures that only the most reliable products reach the market. This process not only provides manufacturers with confidence in their process control but also offers a pedigree certificate of reliability to customers. As semiconductor devices continue to shrink in size and grow in complexity, the importance of WLBI in maintaining high standards of quality and reliability cannot be overstated. Incorporating WLBI into the semiconductor manufacturing process is essential for meeting the fast-paced demands of modern technology markets.
Frequently Asked Questions
What is wafer level burn-in test?
Wafer level burn-in test is a reliability testing process performed on semiconductor wafers before they are diced into individual chips. This test helps identify and eliminate defective dies early in the manufacturing process, ensuring higher reliability and performance of the final products.
How does wafer level burn-in test enhance semiconductor reliability?
Wafer level burn-in test enhances semiconductor reliability by detecting and removing defective dies before they are packaged. This early detection helps in reducing the chances of failures in the field, thereby improving the overall reliability of semiconductor devices.
What are the key benefits of implementing wafer level burn-in test?
The key benefits of implementing wafer level burn-in test include enhanced reliability, cost efficiency, and improved yield analysis. This process helps in identifying defects early, reducing production costs, and ensuring higher quality and performance of semiconductor products.
What are the challenges associated with wafer level burn-in test?
The challenges associated with wafer level burn-in test include defect density issues, technological constraints, and economic considerations. Managing these challenges requires advanced testing protocols, sophisticated equipment, and a balance between cost and reliability.
How does wafer level burn-in test compare with traditional burn-in methods?
Wafer level burn-in test is generally more efficient and accurate compared to traditional burn-in methods. It allows for early detection of defects, reduces overall testing time, and is particularly beneficial for application-specific requirements. However, it may require more advanced equipment and protocols.
What is the impact of wafer level burn-in test on mobile and handheld devices?
Wafer level burn-in test has a significant impact on mobile and handheld devices by ensuring higher reliability and performance. As these devices demand high reliability due to their extensive use, implementing wafer level burn-in test helps in meeting market demands, improving performance metrics, and enhancing customer satisfaction.