Understanding Wafer Level Reliability: What You Need to Know
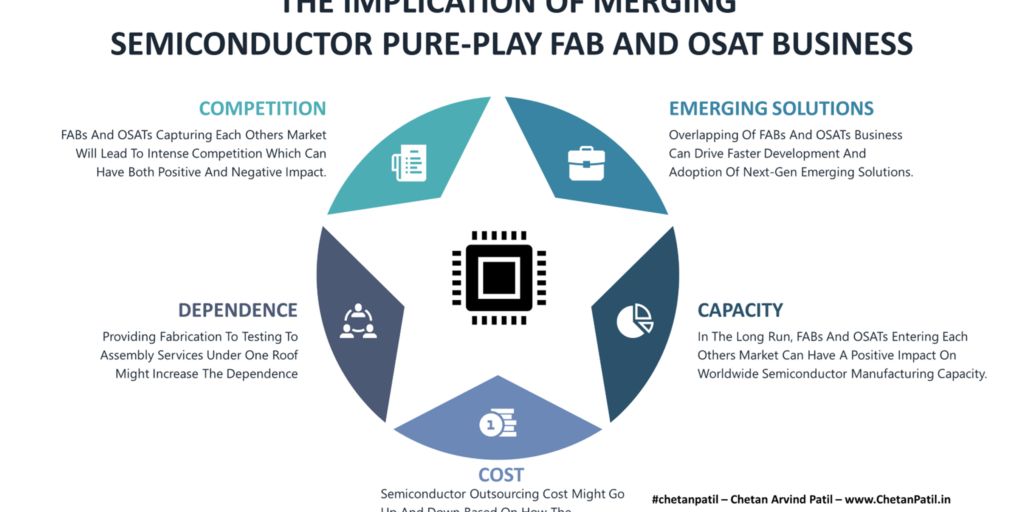
Wafer Level Reliability (WLR) testing is an essential aspect of semiconductor manufacturing, providing insights into process variability and material degradation. As technology advances and chip complexity increases, the demand for more reliable and cost-effective testing methods grows. This article delves into the significance of WLR, the techniques employed, the challenges faced, and its impact on Integrated Circuit (IC) development. Additionally, we explore future trends and applications of WLR across various industries.
Key Takeaways
- WLR testing provides critical feedback for process control and material reliability in semiconductor manufacturing.
- Fast, highly parallel, and modular testing solutions are essential for reducing test time and costs.
- Challenges such as scalability and cost-effectiveness require innovative approaches and advanced test tools.
- Data-driven process improvements enabled by WLR can accelerate IC production cycles.
- Future trends in WLR include evolving design scales, new materials, and integration into R&D processes.
Importance of Wafer Level Reliability in Semiconductor Manufacturing
Reducing Costs and Time
Wafer Level Reliability (WLR) tests are essential in semiconductor manufacturing as they provide fast feedback process control information. This allows manufacturers to make data-driven decisions around process improvements, ultimately reducing costs and accelerating production cycles.
Enhancing Process Control
WLR tests measure the variation in the materials comprising the semiconductor device. This measurement is crucial for enhancing process control, ensuring that the crystal quality of silicon wafers directly affects the properties of the finished product.
Improving IC Performance
By providing insights into variability in processes and degradation, WLR tests help in improving the performance of integrated circuits (ICs). This is particularly important as ICs continue to become smaller and chip complexity increases, necessitating reliable performance for mission-critical applications.
Techniques and Methods in Wafer Level Reliability Testing
Fast Feedback Process Control
Wafer Level Reliability (WLR) test techniques can be used to provide fast feedback process control information regarding the reliability of the product of a semiconductor process. The purpose of WLR tests is the measurement of variation in the materials comprising the semiconductor device. This fast feedback is crucial for identifying and addressing issues early in the manufacturing process, thereby reducing costs and improving yield.
Highly Parallel Testing Approaches
Current approaches often make tradeoffs between channel count and flexibility, but a parallel per pin approach is necessary to address both. This method allows for simultaneous testing of multiple channels, significantly increasing throughput and efficiency. Highly parallel testing approaches are essential for meeting the increased demands from new technology trends and chip complexity.
Modular and Software-Connected Solutions
Evolving design scales and new materials are making WLR testing more critical than ever. Instrument manufacturers are responding with new reliability test tools that are faster, more sensitive, and highly flexible. These tools often feature modular designs and are connected via software, allowing for easy integration into existing manufacturing processes. This modularity and connectivity help drive down the cost of testing while enhancing its effectiveness.
Challenges and Solutions in Wafer Level Reliability Testing
Scalability Issues
As semiconductor manufacturing evolves, manufacturers are quickly approaching a challenge of scale. Traditional approaches to wafer level reliability testing are becoming longer and more expensive. To address this, test teams need to adopt solutions that help mitigate these issues. One effective approach is the use of highly parallel, modular, software-connected solutions, which dramatically reduce test time at lower costs.
Cost-Effective Testing Methods
Increased demands from new technology trends and chip complexity drive engineers to look for methods to increase reliability test data while decreasing cost. Current approaches often make tradeoffs between channel count and flexibility. However, a parallel per pin approach is necessary to address both. This method allows for more efficient testing without sacrificing measurement accuracy.
Advanced Test Tools
Evolving design scales and new materials are making wafer level reliability testing more critical than ever. Instrument manufacturers are responding with new reliability test tools that are faster, more sensitive, and highly flexible. These tools help drive down the cost of testing and provide fast feedback process control information regarding the reliability of semiconductor products.
Impact of Wafer Level Reliability on IC Development
Upstream Testing Benefits
Wafer level reliability (WLR) testing allows IC manufacturers to test further upstream in the manufacturing process. This eliminates much of the time, production capacity, money, and material lost if the packaged device fails. The turnaround time is significantly less because a wafer can be pulled directly off the line and tested without waiting for device packaging.
Data-Driven Process Improvements
WLR tests give manufacturers the ability to make data-driven decisions around process improvements throughout the development cycle. This accelerates the production of reliable, high-performance ICs. Manufacturers are quickly approaching a challenge of scale; traditional approaches will continue to get longer and more expensive, so test teams will need to adopt solutions that help mitigate that.
Accelerating Production Cycles
By integrating WLR testing into the production cycle, manufacturers can significantly reduce test time and improve overall efficiency. Highly parallel, modular, software-connected solutions dramatically reduce test time at lower costs, enabling faster production cycles and quicker time-to-market for new IC products.
Future Trends in Wafer Level Reliability Testing
Evolving Design Scales
Evolving design scales and new materials are making wafer level reliability testing more critical than ever. This trend is driving the demand for reliability testing and modeling much further upstream, especially into the R&D process. Instrument manufacturers are responding with new reliability test tools that are faster, more sensitive, and highly flexible to help drive down the cost of testing.
New Materials and Technologies
The introduction of new materials and technologies in semiconductor manufacturing necessitates advanced reliability testing methods. These new materials often have different failure mechanisms, requiring updated testing protocols to ensure reliability. The stress-driven, classical reliability methodologies will continue to be used to evaluate new processes and identify new, or variations of, known failure mechanisms.
Integration into R&D Processes
Wafer level reliability testing is increasingly being integrated into R&D processes to provide fast feedback on process control and material reliability. This integration allows for data-driven decisions around process improvements throughout the development cycle, accelerating the production of reliable, high-performance ICs. Traditional approaches are becoming longer and more expensive, so test teams will need to adopt highly parallel, modular, and software-connected solutions to dramatically reduce test time and costs.
Applications of Wafer Level Reliability in Various Industries
Wafer level reliability testing is crucial across various industries to ensure the quality and performance of semiconductor devices. Wafer inspection helps to confirm that the chips used in applications like automotive systems and aerospace technology are high in quality, safe, and reliable.
Automotive Industry
In the automotive industry, wafer level reliability testing is essential for the development of advanced driver-assistance systems (ADAS) and autonomous vehicles. These systems require highly reliable semiconductors to ensure safety and performance. The rigorous testing helps in identifying potential failures early in the development process, thereby reducing the risk of costly recalls and enhancing the overall safety of the vehicles.
Consumer Electronics
Consumer electronics, such as smartphones, tablets, and wearables, demand high reliability and performance from their semiconductor components. Wafer level reliability testing ensures that these devices can withstand everyday wear and tear, providing consumers with durable and long-lasting products. This testing is particularly important as devices become more complex and integrated, requiring more robust and reliable components.
Telecommunications
In the telecommunications industry, wafer level reliability testing is vital for the development of high-speed communication devices and infrastructure. As the demand for faster and more reliable communication networks grows, so does the need for highly reliable semiconductor components. This testing helps in ensuring that the components can handle the high data rates and environmental stresses associated with modern communication systems.
Conclusion
Wafer Level Reliability (WLR) testing is an indispensable tool in the semiconductor manufacturing process, providing critical insights into material variability and process degradation. As technology advances and chip complexity increases, the demand for more efficient and cost-effective reliability testing methods has never been higher. By adopting highly parallel, modular, and software-connected solutions, manufacturers can significantly reduce test times and costs while ensuring the production of reliable, high-performance integrated circuits (ICs). The shift towards WLR testing not only accelerates the development cycle but also minimizes the risks associated with packaged device failures. As the industry continues to evolve, the importance of WLR testing will only grow, making it a cornerstone of modern semiconductor manufacturing.
Frequently Asked Questions
What is wafer level reliability (WLR) testing?
Wafer level reliability (WLR) testing involves assessing the reliability of semiconductor devices at the wafer level, providing fast feedback on process control and material variations before packaging.
Why is WLR testing important in semiconductor manufacturing?
WLR testing is crucial as it helps reduce costs and time by identifying issues early, enhances process control, and improves the performance of integrated circuits (ICs).
What are some common methods used in WLR testing?
Common methods include fast feedback process control, highly parallel testing approaches, and modular, software-connected solutions that reduce test time and cost.
What challenges are associated with WLR testing?
Challenges include scalability issues, the need for cost-effective testing methods, and the development of advanced test tools to keep up with evolving design scales and new materials.
How does WLR testing impact IC development?
WLR testing benefits IC development by providing upstream testing advantages, enabling data-driven process improvements, and accelerating production cycles.
What future trends are expected in WLR testing?
Future trends in WLR testing include adapting to evolving design scales, integrating new materials and technologies, and incorporating testing into research and development (R&D) processes.