Innovations in Wafer Production: Shaping the Future of Semiconductor Manufacturing
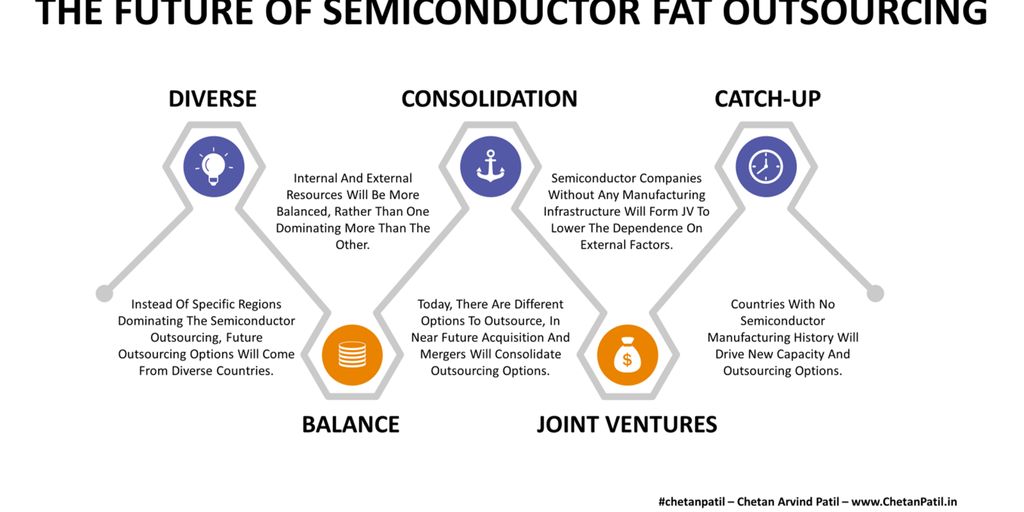
In the ever-evolving landscape of silicon wafer manufacturing, several key production trends are shaping the future of the semiconductor industry. Innovations such as increasing wafer diameter, improving surface quality, developing new crystal growth methods, and exploring alternative materials are steering the industry towards greater efficiency, higher quality, and broader technological horizons. As these trends continue to evolve, they promise to keep the industry at the cutting edge of technology, driving innovation and transforming the electronic landscape.
Key Takeaways
- Increasing wafer diameter enhances production efficiency and reduces costs.
- Improving surface quality is crucial for better semiconductor performance.
- Innovative crystal growth methods are addressing challenges and providing new solutions.
- Alternative materials are being explored to expand the capabilities of semiconductor devices.
- Nanotechnology and automation are playing pivotal roles in advancing wafer manufacturing.
Increasing Wafer Diameter: Enhancing Production Efficiency
In the ever-evolving landscape of silicon wafer manufacturing, several key production trends are shaping the future of the semiconductor industry. One of the most significant trends is the increasing wafer diameter. As technology advances, the industry is moving towards larger wafers, enabling more chips to be produced from a single wafer. This shift not only enhances production efficiency but also helps in reducing costs, making semiconductor technology more accessible.
Benefits of Larger Wafers
One of the key innovations in silicon wafer technology is the transition to larger wafer sizes. Larger wafer sizes, such as 300mm and beyond, offer several advantages, including increased productivity, higher device yield, and cost reduction. The larger surface area of these wafers allows for the integration of more devices, leading to higher performance and functionality.
Technological Advances Enabling Larger Diameters
The widespread adoption of 300mm wafers is one of the critical advancements expected in silicon wafer manufacturing by 2024. These larger wafers provide more surface area for chip production, allowing for increased efficiency and economies of scale. Furthermore, the industry is exploring alternative materials such as silicon carbide (SiC) and gallium nitride (GaN) wafers, which offer superior performance in specific applications, including power electronics and RF devices.
Impact on Cost Reduction
Increasing wafer diameter not only enhances production efficiency but also significantly reduces costs. The ability to produce more chips from a single wafer means lower material costs and higher throughput. This cost reduction is crucial for making semiconductor technology more accessible and driving further innovation in the industry.
Improving Surface Quality in Wafer Production
Simultaneously, there’s a relentless pursuit of improving surface quality. Achieving near-perfect surface conditions is paramount, as even the smallest defect can impair the performance of a semiconductor device. Innovations in surface treatment processes, including more refined polishing and etching techniques, are driving the production of wafers with unprecedented levels of smoothness and defect-free surfaces, thereby boosting the reliability and performance of semiconductor chips.
Innovative Crystal Growth Methods
The development of new methods of crystal growth is at the forefront of research in the field. Scientists and engineers are constantly exploring innovative techniques to grow silicon crystals more efficiently and with even greater purity. These advancements aim to produce crystals with optimal electrical properties for semiconductor applications, ensuring the continued miniaturization and enhancement of electronic devices.
Alternative Materials in Wafer Production
Another significant trend is the development of novel materials for wafer manufacturing. While silicon remains the dominant material, there is growing interest in alternative materials such as gallium nitride (GaN) and silicon carbide (SiC). These materials offer unique properties that make them suitable for specific applications, such as power electronics and high-frequency devices. The integration of these materials with silicon wafers opens up new possibilities for advanced device design and performance.
Lastly, the use of alternative materials is emerging as a pivotal trend. While silicon remains the backbone of the industry, the exploration and integration of new semiconductor materials promise to unlock new capabilities and increase the performance of electronic devices. These materials could offer superior electrical, thermal, or optical properties, opening the door to new technologies and applications previously deemed unattainable.
Novel materials and substrates with improved mechanical stability have been explored, ensuring enhanced durability and reliability. Surface treatment methods have also been refined to enhance wafer quality and reliability.
Additionally, developing new materials and processes for ultra-thin wafer manufacturing is an area of active exploration, aiming to enhance the performance and capabilities of next-generation semiconductor devices.
Nanotechnology’s Role in Wafer Manufacturing
Nanotechnology has emerged as a force in wafer manufacturing, unlocking new possibilities and propelling the industry into a future defined by innovation and excellence. From enhancing collaboration and knowledge exchange to enabling new functionalities, expanding the frontier of materials science, promoting collaboration and knowledge exchange within the semiconductor industry, and driving advancements in manufacturing automation and process control, nanotechnology holds the potential to revolutionize the field.
Automation in Wafer Handling
Benefits of Automated Wafer Handling
Automated wafer handling offers several key advantages:
- Enhanced Effectiveness: Wafer automation reduces the possibility of human mistakes and speeds up production cycles, increasing throughput and shortening turnaround times.
- Improved Accuracy: Robotic systems guarantee uniform wafer handling and placement, lowering the possibility of errors and raising yield rates overall.
- Increased Safety: Automation minimizes human interaction with hazardous materials, ensuring a safer working environment.
Technological Innovations in Automation
Modern robotics and automation technology have revolutionized wafer handling. Key innovations include:
- Robotic Arms: These are used for precise wafer placement and transfer.
- Automated Guided Vehicles (AGVs): These transport wafers between different stages of production with high accuracy.
- Vacuum Handlers: These ensure secure and contamination-free wafer handling.
Future of Automation in Semiconductor Manufacturing
The future of wafer handling automation looks promising with several trends on the horizon:
- Increased Integration with AI: AI can further optimize wafer handling processes by predicting and mitigating potential issues.
- Enhanced Connectivity: IoT-enabled devices will allow for real-time monitoring and control of wafer handling systems.
- Scalability: Future systems will be more scalable, allowing manufacturers to easily adapt to changing production demands.
Manufacturers that embrace wafer handling automation will gain a competitive edge in the rapidly evolving industry.
Challenges in Ultra-Thin Wafer Manufacturing
Issues in Producing Ultra-Thin Wafers
Manufacturing ultra-thin silicon wafers presents several significant challenges. One major obstacle is the delicate nature of the wafers, making handling and fragility issues paramount. Additionally, attaining precise thickness and uniformity during the thinning process is complex. Controlling wafer warpage, bowing, and reducing defects and impurities are key challenges to overcome.
Innovative Solutions for Thin Wafer Production
Significant advancements have been made in equipment and tooling to address the challenges associated with ultra-thin silicon wafer manufacturing. Specialized wafer handling and support systems have been developed to cater to the fragility of ultra-thin wafers. Cutting-edge thinning equipment with higher precision and automation capabilities aids in achieving the desired thickness and uniformity. Advanced surface treatment and cleaning technologies ensure optimum wafer quality.
Future Research Directions
The industry has witnessed remarkable innovations that tackle the challenges associated with ultra-thin silicon wafer manufacturing. Advanced wafer thinning techniques, including grinding, etching, and polishing, have been developed for precise thickness control. Thin film transfer technologies, such as bonding and layer transfer, offer alternative approaches to obtaining ultra-thin wafers. Future research will likely focus on further enhancing these techniques and exploring new methods to improve wafer quality and production efficiency.
Conclusion
Together, these trends in silicon wafer manufacturing—increasing wafer diameter, improving surface quality, developing new crystal growth methods, and the use of alternative materials—are steering the semiconductor industry towards a future of greater efficiency, higher quality, and broader technological horizons. As these trends continue to evolve, they promise to keep the industry at the cutting edge of technology, driving innovation and transforming the electronic landscape. The continuous advancements in nanotechnology, automation, and ultra-thin wafer production are not only addressing current challenges but also opening new avenues for future applications. By embracing these innovations, the semiconductor industry is poised to achieve unprecedented levels of performance and sustainability, ensuring its pivotal role in the advancement of global technology.
Frequently Asked Questions
What are the benefits of increasing wafer diameter in semiconductor manufacturing?
Increasing wafer diameter allows more chips to be produced from a single wafer, enhancing production efficiency and reducing costs.
How does improving surface quality impact semiconductor performance?
Improving surface quality reduces defects, leading to better performance and reliability of semiconductor devices.
What are some innovative crystal growth methods used in wafer production?
New techniques such as molecular beam epitaxy and chemical vapor deposition are being used to achieve higher purity and better control in crystal growth.
Why are alternative materials being explored in wafer production?
Alternative materials offer potential benefits such as higher electron mobility, better thermal conductivity, and the ability to operate at higher frequencies, which can improve overall device performance.
How is nanotechnology revolutionizing wafer manufacturing?
Nanotechnology enhances manufacturing precision, improves surface treatment processes, and enables new functionalities in semiconductor devices.
What are the challenges in producing ultra-thin wafers and how are they being addressed?
Producing ultra-thin wafers poses challenges such as maintaining structural integrity and reducing defects. Innovative solutions like advanced thinning techniques and thin film transfer technologies are being developed to address these issues.