Revolutionizing the Electronics Industry: Advances in Semiconductor Production
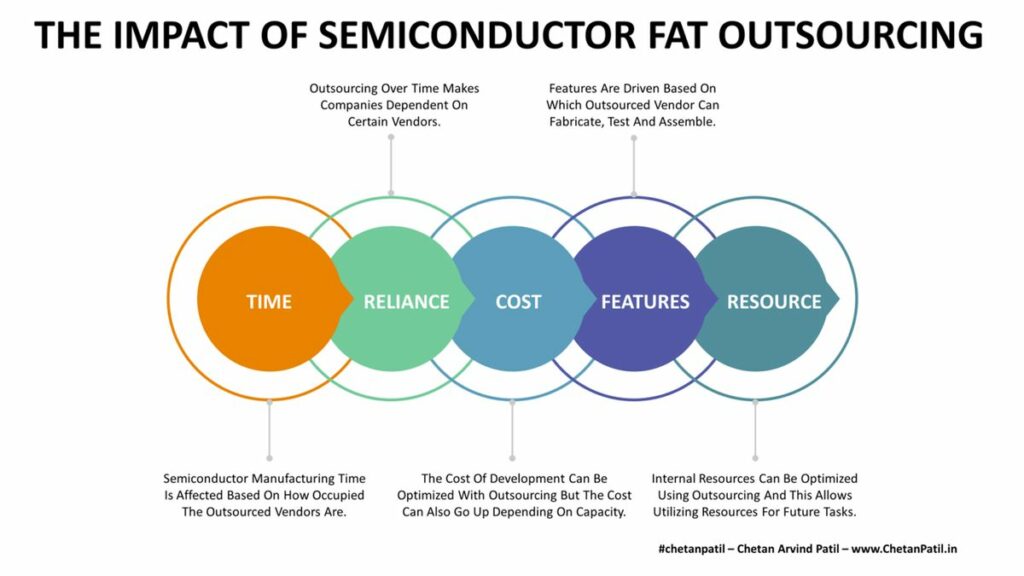
The electronics industry is on the cusp of a new era with groundbreaking advances in semiconductor production. As we transition from traditional lean manufacturing to smart manufacturing, the industry is leveraging data analytics, artificial intelligence, and cutting-edge fabrication techniques to meet the increasing demands for more complex and efficient semiconductor devices. This article explores the evolution of manufacturing practices, the latest innovations in fabrication, and the challenges and opportunities that lie ahead in semiconductor production, all of which are significantly influenced by global sales trends.
Key Takeaways
- The transition from Lean to Smart Manufacturing marks a significant shift in semiconductor production, focusing on data-driven processes and advanced technologies to enhance efficiency and quality.
- Innovative etching methods such as RIE and plasma etching have revolutionized semiconductor fabrication, allowing for more precise and controlled manufacturing of smaller, more complex devices.
- Modern semiconductor production faces the challenge of balancing cost, quality, and speed, while navigating the intricacies of advanced devices and considering environmental sustainability.
- Recent trends in global semiconductor sales, showing a slight increase, influence production strategies and necessitate strategic adjustments to align with market fluctuations.
- The future of semiconductor manufacturing will be shaped by the industry’s ability to embrace Smart Manufacturing, driving further advancements and enabling the creation of sophisticated technologies.
The Evolution from Lean to Smart Manufacturing
The Legacy of Lean Manufacturing in Semiconductors
Lean Manufacturing has undoubtedly revolutionized the semiconductor industry, establishing principles that have become deeply ingrained in manufacturing practices. By focusing on eliminating waste, streamlining processes, and enhancing flow, Lean Manufacturing has enabled semiconductor manufacturers to achieve significant cost reductions, improve production times, and enhance product quality. These gains have been instrumental in fueling the growth and innovation of the semiconductor industry.
In the dynamic and ever-evolving world of semiconductor manufacturing, the pursuit of efficiency and quality has been an enduring challenge. For decades, lean manufacturing processes have helped semiconductor companies stay alive in the challenge industry with high demand. However, as the demands of the semiconductor industry continue to grow, so does the need for a more comprehensive approach.
The imperative for Smart Manufacturing is clear. While Lean Manufacturing has played a pivotal role in advancing the semiconductor industry, the challenges and opportunities we face today demand a more comprehensive and transformative approach. The rapid pace of technological advancements, the increasing complexity of semiconductor devices, and the growing demand for data-driven insights necessitate a shift towards Smart Manufacturing.
Embracing Smart Manufacturing: The New Paradigm
The shift towards Smart Manufacturing signifies a transformative leap in the electronics industry. By harnessing digital technologies, this new paradigm fosters an interconnected manufacturing landscape. The integration of smart sensors and real-time analytics not only elevates efficiency but also enhances production processes, allowing for predictive maintenance and proactive decision-making.
Key benefits semiconductor manufacturers can expect from embracing Smart Manufacturing include:
- Real-time monitoring and control of production processes
- Enhanced predictive maintenance capabilities
- Improved product quality and consistency
- Increased responsiveness to market changes and customer demands
The imperative for adopting Smart Manufacturing stems from the need to address today’s challenges, such as the rapid pace of technological advancements and the increasing complexity of semiconductor devices. This approach is not just about keeping pace; it’s about setting the stage for future innovation and maintaining a competitive edge in a fast-evolving market.
The Role of Data Analytics and AI in Smart Manufacturing
The integration of data analytics and artificial intelligence (AI) in Smart Manufacturing marks a significant leap forward in the semiconductor industry. These technologies enable a more intelligent and interconnected manufacturing environment, where real-time monitoring and predictive maintenance become the norm. By harnessing the vast amounts of data generated by manufacturing equipment, companies can achieve unprecedented levels of efficiency and product quality.
Key benefits of incorporating AI and data analytics into Smart Manufacturing include:
- Real-time data insights for optimized process control
- Predictive maintenance capabilities to minimize downtime
- Enhanced product quality through early detection of issues
However, the transition to Smart Manufacturing is not without its challenges. Manufacturers must navigate the complexities of integrating new technologies with existing systems and manage the cybersecurity risks associated with a more connected manufacturing landscape. The journey is complex, but the potential rewards for those who successfully implement Smart Manufacturing strategies are substantial, offering a competitive edge in a rapidly evolving industry.
Cutting-Edge Techniques in Semiconductor Fabrication
Advances in Etching: RIE and Plasma Etching
The semiconductor industry has witnessed a significant transformation with the advent of advanced etching techniques. Reactive Ion Etching (RIE) and plasma etching stand at the forefront of this evolution, enabling the creation of intricate patterns essential for modern electronic components. These methods have replaced older, less precise techniques, offering greater control over the etching process and yielding higher-quality results.
RIE and plasma etching are pivotal for the mass production of next-generation semiconductors, including two-dimensional (2D) materials like molybdenum disulfide (MoS2). The ability to etch at a large scale, uniformly, and without defects is crucial for the industry’s move towards more advanced devices. The table below highlights the comparative advantages of these etching methods:
Technique | Precision | Material Compatibility | Defect Rate |
---|---|---|---|
RIE | High | Broad | Low |
Plasma | Very High | Selective | Very Low |
As the industry gears up for the next generation of chips, selective etch tools are being deployed to cater to new memory and logic devices. The precision and selectivity of these tools are essential for meeting the stringent requirements of modern semiconductor fabrication.
The Rise of Lights Out Manufacturing
The concept of Lights Out Manufacturing represents a transformative approach in the semiconductor industry, where factories are fully automated, operating with minimal human oversight. This technique is not just a futuristic vision but a reality that’s increasingly being adopted, as it promises to enhance productivity, quality, and sustainability while reducing costs.
Key benefits of Lights Out Manufacturing include:
- Increased efficiency: Automation allows for continuous production without the constraints of human labor schedules.
- Consistency and quality: Machines can maintain precise control over production processes, leading to fewer errors and higher quality products.
- Safety: With fewer humans on the factory floor, the risk of workplace accidents is significantly reduced.
- Scalability: Automated systems can be quickly adjusted to changes in production volume or design.
Despite these advantages, transitioning to a fully automated manufacturing environment is not without its challenges. Companies must invest in advanced technologies and ensure seamless integration with existing systems. Moreover, the shift requires a strategic approach to manage the workforce transition and upskill employees for new roles in the automated landscape.
Innovations in Pattern Transfer and Lithography
The relentless pursuit of miniaturization in the semiconductor industry has led to groundbreaking innovations in pattern transfer and lithography. Advanced techniques such as extreme ultraviolet (EUV) lithography and multi-patterning are now at the forefront, pushing the boundaries of what’s possible in semiconductor device manufacturing.
EUV lithography, in particular, has become a game-changer. It employs short-wavelength light to etch incredibly fine patterns onto silicon wafers, achieving features as minuscule as a few nanometers. This capability is vital for the production of next-generation microprocessors and other complex electronic components.
Another promising development is the adoption of nanoimprint lithography, especially in niche markets like photonics and biotech chips. After years of refinement, this technology is gaining traction due to its precision and cost-effectiveness. Additionally, collaborations are emerging to integrate novel technologies like inkjet techniques into high-volume semiconductor manufacturing, promising further advancements in efficiency and scalability.
Challenges and Opportunities in Modern Semiconductor Production
Balancing Cost, Quality, and Speed
In the semiconductor industry, the equilibrium between cost, quality, and speed is a delicate one. Manufacturers must navigate the intricate tradeoffs to remain competitive in a market that demands high-performance and reliable products at a reasonable cost. The ‘Hidden Costs And Tradeoffs In IC Quality‘ highlight the increasing difficulty in balancing reliability against cost as chip complexity surges and devices become more domain-specific.
The concept of ‘Taming Corner Explosion In Complex Chips’ refers to the challenge of managing the numerous variables, or ‘corners,’ in chip design. The cost of analysis and the risk of over-engineering margins to ensure quality can lead to a product that is either too expensive or not competitive. Conversely, insufficient analysis may result in reduced yield and reliability.
To address these challenges, some companies are adopting strategies like ‘Testing More To Boost Profits.’ By leveraging the growing availability of chip data, manufacturers aim to salvage and repurpose chips that do not meet initial specifications, thus finding a balance between cost recovery and maintaining quality standards.
Navigating the Complexity of Advanced Semiconductor Devices
The relentless pursuit of performance and efficiency in semiconductors has led to a significant increase in device complexity. Advanced packaging, once a beacon for massive improvements, now introduces a myriad of challenges that diverge from the well-trodden paths of Moore’s Law and the ITRS roadmap. This complexity is not just confined to the physical design but extends to software, manufacturing, and the integration of new materials.
The quality of semiconductor device models is essential for design success, particularly as the industry grapples with surging design complexity and shrinking market windows. As we cram more processors and memories onto a die or into a package, the number of unknowns soars, making it increasingly difficult to predict and manage the outcomes of design choices.
The move towards advanced packaging, such as 2.5D systems, offers a potential solution to reticle limits and yield challenges. However, this shift also brings its own set of business, organizational, and technical hurdles. Moreover, the disaggregation of chips complicates supply chain management, raising concerns about the origin and integrity of components in advanced devices.
Sustainability and Environmental Considerations
The semiconductor industry is at a pivotal juncture where sustainability has become as crucial as innovation. With the spotlight on energy consumption and waste reduction, companies are exploring innovative solutions to minimize environmental impact. The transition towards high sustainability is evident with the growth of solar photovoltaics (PV) as a significant power source, signaling a shift away from fossil fuels.
Efforts to create more sustainable semiconductor products include the development of fire-resistant sodium batteries and the use of lightweight materials like AL/Mg/AL laminates in production. These advancements not only contribute to the industry’s sustainability goals but also offer improved safety and efficiency.
The challenges in sustainable semiconductor production are multifaceted, ranging from reducing volatile organic compound (VOC) emissions to managing the energy-intensive nature of semiconductor fabrication. However, the opportunities to harness innovative technologies and materials present a promising pathway to a greener future in electronics manufacturing.
The Impact of Global Semiconductor Sales on Production Strategies
Analyzing Recent Sales Trends
The semiconductor industry has experienced significant fluctuations in recent years, with sales trends providing critical insights into the market’s health and future direction. The infamously cyclical semiconductor industry had a challenging year in 2023, with a downturn that echoed the historical patterns of volatility.
Recent data from the Semiconductor Industry Association (SIA) highlights a series of growth spurts and slowdowns. For instance, in February 2022, global semiconductor sales saw a remarkable year-to-year increase of 32.4%, with the Americas market leading at a 43.2% increase. However, by July, the growth rate had decelerated to 7.3% year-to-year, indicating a cooling off from the earlier surge.
The table below summarizes key sales trends observed in the semiconductor industry over the past year:
Month | Year-to-Year Sales Increase | Month-to-Month Sales Increase |
---|---|---|
February | 32.4% | 3.4% |
June | 29.2% | – |
July | 7.3% | – |
November | 7% | – |
These figures underscore the dynamic nature of semiconductor sales and the need for industry players to remain agile in response to market shifts.
Strategic Adjustments in Response to Market Fluctuations
In the face of market fluctuations, semiconductor companies are compelled to make strategic adjustments to maintain competitiveness and profitability. Supply chain resilience has become a focal point, with firms re-evaluating their supplier relationships and inventory strategies to better withstand disruptions.
To illustrate the strategic shifts, consider the following table outlining key areas of focus:
Focus Area | Description |
---|---|
Supplier Diversification | Reducing dependency on single sources and exploring alternative suppliers. |
Inventory Management | Implementing just-in-time (JIT) and safety stock strategies to optimize inventory levels. |
Production Flexibility | Enhancing the ability to scale production up or down in response to demand changes. |
Risk Management | Adopting advanced analytics to predict and mitigate potential supply chain risks. |
These adjustments are not only reactive but also proactive, as companies aim to anticipate changes and position themselves advantageously. The strategic use of data analytics and AI is pivotal in this regard, enabling firms to make informed decisions and adapt swiftly to the ever-evolving market landscape.
Long-term Implications for Semiconductor Manufacturing
The semiconductor industry is at a pivotal juncture, with long-term strategies being shaped by a confluence of factors. Global semiconductor market’s long-term outlook remains strong, despite short-term cyclical downturns. This optimism is underpinned by the industry’s continuous push towards Smart Manufacturing, which promises to unlock unprecedented levels of efficiency and innovation.
As companies explore new regions for expansion, they are influenced by three critical factors: supply chain security, sustainability, and subsidies. These factors not only drive the geographical diversification of semiconductor production but also ensure that new facilities are designed with the latest technological advancements in mind.
The table below summarizes the key drivers of long-term semiconductor manufacturing strategies:
Driver | Description |
---|---|
Supply Chain Security | Ensuring stable and secure access to materials and components. |
Sustainability | Minimizing environmental impact and adhering to green practices. |
Subsidies | Leveraging government incentives to offset initial setup costs. |
In conclusion, the semiconductor industry’s evolution is marked by a strategic blend of traditional manufacturing excellence and cutting-edge innovation. As manufacturers navigate the complexities of advanced semiconductor devices, they must balance cost, quality, and speed, all while maintaining a commitment to sustainability.
Conclusion
The semiconductor industry stands at the cusp of a transformative era, shaped by the relentless pursuit of efficiency and innovation. Lean Manufacturing has laid a robust foundation, streamlining processes and minimizing waste to meet the ever-increasing demands of electronic device production. Yet, the future beckons with the promise of Smart Manufacturing, a paradigm shift that leverages data analytics and advanced technologies to forge a more intelligent, interconnected, and agile manufacturing ecosystem. As semiconductor manufacturers embrace this evolution, they unlock unprecedented levels of efficiency, quality, and innovation. The journey from Lean to Smart Manufacturing is not just a testament to the industry’s adaptability but also a blueprint for its continued growth and the development of sophisticated technologies that will define the electronics landscape for years to come.
Frequently Asked Questions
How has Lean Manufacturing impacted the semiconductor industry?
Lean Manufacturing has revolutionized the semiconductor industry by eliminating waste, streamlining processes, and enhancing flow. This has led to significant cost reductions, improved production times, and better product quality, fueling growth and innovation in the industry.
What is Smart Manufacturing and why is it important for semiconductors?
Smart Manufacturing represents a transformative approach that leverages data and advanced technologies to make semiconductor production more intelligent, interconnected, and agile. It’s crucial for meeting the increasing complexity of semiconductor devices and the demand for data-driven insights.
What are some of the advanced techniques used in semiconductor fabrication?
Techniques such as reactive ion etching (RIE) and plasma etching have been developed for precise and controlled etching, which is vital for creating smaller and more complex electronic components.
What is ‘Lights Out’ manufacturing and how is it affecting the semiconductor industry?
Lights Out manufacturing is an automated production method that operates with minimal human intervention, enhancing productivity, improving quality, and reducing costs and environmental impact in the semiconductor industry.
What are the main challenges faced by modern semiconductor production?
The main challenges include balancing cost, quality, and speed, navigating the complexity of advanced semiconductor devices, and addressing sustainability and environmental concerns.
How do global semiconductor sales influence production strategies?
Global semiconductor sales trends necessitate strategic adjustments in production to respond to market fluctuations. These trends have long-term implications for manufacturing processes, investment decisions, and innovation in the semiconductor industry.