The Complete Process of Silicon Manufacturing: From Quartz to Chip
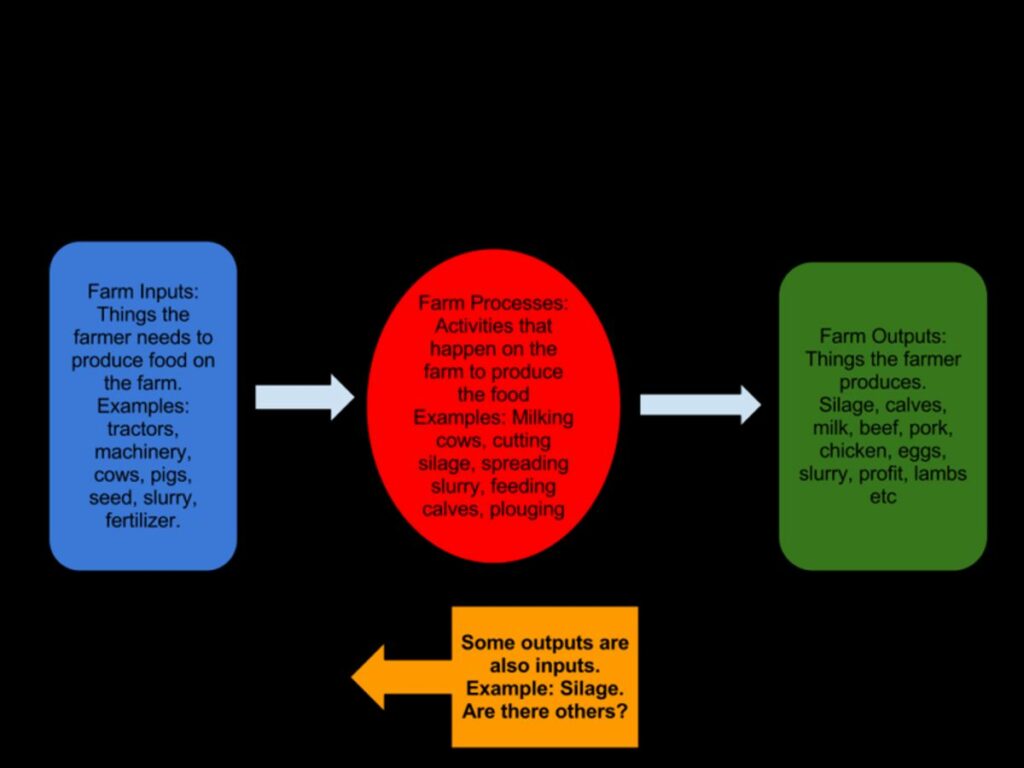
The journey of transforming quartz sand into sophisticated silicon chips is a testament to human ingenuity and technological prowess. This intricate process begins with the extraction of silicon from quartz sand and spans numerous meticulous steps, including purification, doping, and layering, to create the complex integrated circuits at the heart of modern electronics. Over approximately 14 weeks and up to 700 processing steps, raw materials are meticulously transformed in highly controlled environments, culminating in the production of essential components that power a myriad of technological advancements.
Key Takeaways
- The silicon manufacturing process starts with the extraction of silicon from quartz sand, requiring significant chemical purification to achieve the necessary purity.
- Silicon wafers, the foundation of microchips, are created through complex procedures such as the Czochralski process, which grows single-crystal silicon ingots.
- Wafer fabrication involves precise steps like doping, photolithography, and etching to pattern the electrical circuits on the silicon substrate.
- Quality control is paramount, with multiple testing phases, including Electrical Die Sorting (EDS) and final testing, to ensure the functionality and reliability of the chips.
- The semiconductor production process is a global endeavor, relying on an intricate supply chain and international collaboration to source materials and components.
The Foundation of Silicon Chips: From Quartz to Pure Silicon
The Journey from Sand to Silicon
The transformation of quartz sand into high-purity silicon is a remarkable alchemy central to the tech industry. Silicon dioxide, abundant in quartz sand, is the primary raw material used in semiconductor manufacturing. Through mining and purification, this compound is refined to achieve the necessary purity for electronic applications.
The process begins with the extraction of silicon from quartz, which involves a series of chemical reactions to remove impurities. The result is silicon with a purity of over 99.9%, a crucial prerequisite for the subsequent steps in chip production. This purified silicon is then prepared for doping, where specific elements are introduced to alter its electrical properties.
The journey from sand to silicon is not only a testament to human ingenuity but also a complex, multi-step endeavor. It includes up to 700 processing steps and can take approximately 14 weeks to complete, culminating in the creation of a microchip that is indispensable for a myriad of devices.
Purification and Transformation into Polycrystalline Silicon
The transformation from quartz to polycrystalline silicon is a pivotal step in the silicon manufacturing process. After the initial purification, the material undergoes further refinement to achieve the desired purity levels necessary for semiconductor applications. This stage is crucial as it sets the foundation for the quality of the final silicon wafers.
The process begins with the purified silicon melt, which is derived from quartz sand. This melt is carefully cooled and solidified to form polycrystalline silicon, also known as polysilicon. The polysilicon is then cast into large, cylindrical ingots. These ingots are the raw material for the subsequent steps in the wafer manufacturing process.
To ensure the highest quality, the fabrication of silicon wafers takes place in a highly controlled clean room environment. This minimizes the introduction of impurities that could affect the performance of the final microchips. The ingots are eventually sliced into thin, circular wafers, ready for the intricate patterning and layering processes that will transform them into the complex architecture of microchips.
The Czochralski Process: Growing Single-Crystal Silicon Ingots
The Czochralski (CZ) process is pivotal in the transformation of molten silicon into the single-crystal ingots that are the foundation of all silicon chips. This method involves dipping a small seed crystal into the molten silicon and slowly drawing it out, allowing the crystal structure to grow uniformly around the seed. The result is a cylindrical ingot, or boule, that possesses the perfect lattice structure necessary for high-quality semiconductor devices.
Once the boule is formed, it is carefully cooled and then sliced into thin, circular wafers. These wafers are the starting point for the intricate layers of circuitry that will eventually form the microchip. The process is not only a marvel of precision engineering but also a testament to the scalability of semiconductor manufacturing. As the demand for more powerful chips grows, the industry has seen a trend towards larger wafers, which allow for more chips to be produced from a single ingot, representing a cost-effective approach for transitioning to larger wafer production.
The following table outlines the typical dimensions of wafers produced using the CZ process, reflecting the industry’s shift towards larger diameters:
Wafer Diameter (mm) | Thickness (mm) | Chips per Wafer (approx.) |
---|---|---|
200 | 0.725 | 100 – 200 |
300 | 0.775 | 400 – 700 |
450 | 0.925 | 1000 – 1500 |
It’s clear that the CZ process is a cornerstone of the semiconductor industry, enabling the mass production of the silicon wafers that are essential for today’s technology.
Wafer Fabrication: The Heart of Semiconductor Manufacturing
Slicing Ingots into Thin Wafers
Once the ingots are formed through the CZ process, they are ready to be transformed into the foundational elements of semiconductor devices: the wafers. Silicon ingot cutting into delicate wafers is a critical step that sets the stage for the intricate circuitry that will later be etched onto their surface. The ingots are carefully sliced into thin, circular wafers, ensuring that each slice maintains the perfect crystalline structure necessary for high-quality electronics.
The size of the wafer is a significant factor in semiconductor manufacturing. Larger wafers allow for more chips to be produced from a single slice, optimizing the output and reducing waste. The process of slicing is not only about precision but also about maximizing the yield of the ingot. The goal is to fabricate as many dies as possible from each wafer, with each die potentially becoming an individual chip or component.
In the clean room environment of a wafer fabrication facility, the wafers undergo further processing. Here, they are subjected to a series of treatments that prepare them for the complex task of circuit patterning. This includes cleaning, polishing, and priming the surface to receive the intricate designs that will define their functionality as electronic components.
Surface Preparation and Cleaning
Before the intricate process of patterning can begin, the silicon wafers must be immaculately cleaned to ensure the removal of any contaminants that could interfere with the subsequent manufacturing steps. This stage is critical as even the smallest particle can ruin the functionality of the final chip. The cleaning process typically involves a series of steps, each designed to remove different types of impurities.
WaferPro’s comprehensive guide highlights several essential cleaning methods, such as solvent cleaning to dissolve organic residues, RCA cleaning for removing organic and ionic contaminants, and more advanced techniques like ozone, megasonic, and cryogenic cleaning. Each method targets specific contaminants:
- Solvent Cleaning: Targets organic residues
- RCA Cleaning: Removes organic and ionic impurities
- Ozone Cleaning: Oxidizes and volatilizes organic contaminants
- Megasonic Cleaning: Dislodges particles using high-frequency sound waves
- Cryogenic Cleaning: Uses extreme cold to fracture and remove contaminants
After cleaning, the wafers are dried and inspected for cleanliness before moving on to the doping and photolithography stages, where the real magic of semiconductor manufacturing begins.
Doping: Modifying Electrical Properties
Doping is a critical step in semiconductor manufacturing, where impurities are introduced into the pure silicon to alter its electrical properties. This deliberate process is essential for creating the p-type or n-type semiconductor materials required for different components of the microchip.
The type and amount of dopant determine the electrical characteristics of the semiconductor. For instance, adding boron creates p-type silicon, which has an abundance of positive charge carriers (holes), while adding phosphorus results in n-type silicon, with an excess of negative charge carriers (electrons).
Here is a simple list of common dopants and the type of semiconductor they produce:
- Boron (B) – creates p-type silicon
- Phosphorus (P) – creates n-type silicon
- Arsenic (As) – also creates n-type silicon
- Antimony (Sb) – another n-type dopant
The precision in doping is paramount, as it directly affects the performance and efficiency of the final semiconductor devices.
Photolithography: Patterning the Silicon Wafer
Photolithography is a pivotal step in the semiconductor manufacturing process, where precision and control are paramount. It involves using light to transfer a pattern onto a substrate, typically a silicon wafer. The process begins with a photosensitive material, known as the resist, which is applied to the wafer’s surface. When exposed to ultraviolet light through a patterned mask, the resist undergoes a chemical change, allowing the desired circuit pattern to be imprinted onto the wafer.
The following list outlines the key stages of photolithography:
- Application of the photoresist layer
- Alignment of the photomask above the wafer
- Exposure to ultraviolet light to transfer the pattern
- Development of the photoresist to reveal the pattern
- Etching of the exposed areas to create the circuitry
This meticulous process is repeated multiple times, with each iteration adding to the complexity of the microchip. The goal is to fabricate increasingly tighter and smaller designs, maximizing the number of dies that can be produced from a single wafer. The larger the wafer, the more chips it can yield, enhancing the efficiency of the production process.
Layering and Patterning: Constructing the Microchip Architecture
Oxidation and Deposition Processes
The transformation of a silicon wafer into a functional microchip involves critical steps of oxidation and deposition. Oxidation is the process where the wafer is exposed to oxygen or steam to grow a layer of silicon dioxide on its surface. This layer serves as an insulator and a base for further deposition processes.
Deposition techniques, such as Chemical Vapor Deposition (CVD) and Physical Vapor Deposition (PVD), are employed to add various materials onto the wafer. These materials can include metals, insulators, and semiconductors, which are layered to form the intricate circuitry of the chip. The precision of these processes is paramount, as they define the electrical properties and functionality of the final product.
Here is a simplified list of the steps involved in the oxidation and deposition stages:
- Surface cleaning of the silicon wafer to ensure purity.
- Oxidation to grow the silicon dioxide layer.
- Deposition of different materials to build the chip’s architecture.
- Annealing to strengthen the deposited layers.
- Repeating the process for multiple layers as required by the chip design.
Etching Techniques for Precise Circuit Patterns
Etching is the process of carving intricate patterns onto the silicon wafer, a crucial step in defining the microchip’s architecture. Dry etching stands out for its ability to produce precise and complex patterns, essential for the miniaturization of electronic components. This technique employs reactive gases to remove selected areas of material, guided by the pattern established during photolithography.
The etching process not only shapes the tiny circuits but also influences the performance and yield of the final chips. As the industry strives for smaller and tighter designs, the role of etching becomes increasingly significant. The larger the wafer, the more chips can be yielded, making the efficiency of etching a pivotal factor in semiconductor manufacturing.
Here’s a glimpse into the types of etching used in the industry:
- Wet Etching: Involves chemical solutions to remove material.
- Dry Etching: Utilizes plasma or reactive gases for precision.
- Plasma Etching: A form of dry etching that offers high anisotropy.
- Reactive Ion Etching (RIE): Enhances directionality and pattern fidelity.
Ion Implantation and Metallization
Ion implantation is a pivotal step in semiconductor device fabrication, where ions are accelerated and directed into the silicon wafer to change its electrical properties. This process introduces specific impurities, or dopants, into the silicon to achieve the desired conductivity. Furnace annealing or rapid thermal annealing (RTA) is often employed post-implantation to activate the dopants and repair the silicon lattice.
Following implantation, metallization is the next critical phase. It involves the deposition of metal layers to form the interconnections between the various components of the integrated circuit. Copper is a common choice for these interconnections due to its excellent electrical conductivity. The process of adding copper interconnects is intricate, requiring precision to ensure the functionality and reliability of the final semiconductor device.
The table below summarizes the key steps and their purposes in the ion implantation and metallization stages:
Step | Purpose |
---|---|
Ion Implantation | Introduce dopants to modify electrical properties |
Annealing | Activate dopants and repair silicon lattice |
Metallization | Deposit metal layers for electrical interconnections |
Testing and Packaging: Ensuring Quality and Functionality
Electrical Die Sorting (EDS) Testing
After the intricate process of layering and patterning the microchip architecture, the next critical phase is Electrical Die Sorting (EDS) Testing. This step is pivotal in ensuring that each chip functions according to the predefined criteria before they are cut from the silicon wafer and packaged. EDS testing employs automated test equipment to apply electrical signals to the chip and measure the output, effectively screening for defects.
The EDS testing process is part of a broader suite of semiconductor tests, which include:
- Wafer Testing (Wafer Sort): Testing individual chips while still part of the silicon wafer.
- Package Testing (Final Test): Conducted after packaging to check for final-stage defects.
- Burn-In Testing: Exposing chips to stress conditions to identify early failures.
Collaborations in the industry, such as the one between Japanese chip maker Rohm and venture company Quanmatic, aim to enhance the EDS process. By integrating quantum technology into chipmaking, they strive to push the boundaries of semiconductor testing, ensuring that only devices meeting the highest standards of performance, functionality, and reliability reach the market.
Assembly and Packaging of Integrated Circuits
Once the semiconductor testing phase is complete, the dies that have passed all the rigorous checks are ready for the final stage of semiconductor device fabrication: assembly and packaging. This process is crucial as it encapsulates the die in a supporting case that prevents physical damage and shields it from environmental factors, ensuring the longevity and reliability of the integrated circuits.
The assembly process involves several steps, starting with the attachment of the die to a substrate or lead frame. Then, wire bonding connects the die to the package’s leads. Next, encapsulation materials are used to protect the die, with options ranging from plastic molding to ceramic or metal housing, depending on the application requirements. Finally, the individual packages are cut apart, ready to be integrated into various devices.
The choice of packaging material and the method of encapsulation are determined by factors such as cost, heat dissipation, size constraints, and the intended application of the IC. The table below summarizes the common packaging materials and their typical uses:
Material | Typical Use |
---|---|
Plastic | Consumer electronics |
Ceramic | High-performance computing |
Metal | Industrial applications |
Final Testing and Quality Assurance
After the assembly and packaging of integrated circuits, the final testing phase plays a pivotal role in ensuring that the chips meet the rigorous demands of various applications. This stage is the last line of defense against potential defects that could impact consumers and industries dependent on these semiconductor devices. The process involves several types of tests:
- Wafer Testing (Wafer Sort): This involves testing individual chips while they are still part of the silicon wafer.
- Package Testing (Final Test): Conducted after the chips have been packaged to identify any final-stage defects.
- Burn-In Testing: Chips are subjected to stress conditions to weed out early failures.
Efficient utilization of test equipment is crucial, as it represents a significant investment. Balancing the need for thorough testing with cost and time constraints is a continuous challenge. The advancement of testing methodologies, such as the integration of AI and machine learning, aims to enhance the efficiency and effectiveness of this essential process. The final verification step compares all metrics against the established quality standards. Only those wafers that meet or exceed these specifications are shipped to customers.
The Global Supply Chain of Semiconductor Production
Raw Material and Component Sourcing
The intricate web of global supply chains is a defining feature of modern semiconductor production. Raw materials and specialized components are sourced from a multitude of countries, each contributing a unique piece to the semiconductor puzzle. For instance, the journey of a silicon carbide chip may begin in a factory in New Hampshire, but it will rely on inputs from across the world before it becomes part of the vehicles on American roads and beyond.
The procurement of these materials and components is a complex process, involving numerous international players. Here’s a snapshot of where some key activities take place:
- Crystal boule manufacturing: New Hampshire, U.S., Norway, Taiwan
- Machine components: Germany, Japan, United States
- Wafer slicing: Czech Republic, Italy
- Chip manufacturing: South Korea, Taiwan
- Packaging operations: China, Vietnam, Malaysia
This global effort underscores the importance of international collaboration in the semiconductor industry. The Biden administration’s initiative to invest $39 billion to bolster domestic manufacturing highlights a strategic move to bring more of the supply chain back to the United States. However, the interdependence of nations in this sector is a testament to the complexity and scale of semiconductor production.
The Role of International Collaboration
The semiconductor industry is a testament to the power of global collaboration. Materials and expertise flow across borders, contributing to the intricate process of chip manufacturing. For instance, a single microchip can encapsulate materials from over 16 countries, involve 5 separate facilities, and traverse more than 10,000 miles before completion.
This international effort is not just about logistics; it’s about shared knowledge and technology. The Transatlantic Cooperation on Semiconductors and AI in 2024 highlights the importance of strategic partnerships. A coordination mechanism through the European Semiconductor Board exemplifies such collaboration, fostering dialogue and joint initiatives between various stakeholders.
The synergy between competition and cooperation, or ‘coopetition’, is increasingly prevalent in the semiconductor landscape. Companies and nations alike recognize that while they compete in the marketplace, they must also cooperate to advance technology and address common challenges. This delicate balance is crucial for the industry’s ongoing and future success.
From Local Factories to Global Markets
The semiconductor industry exemplifies the complexities of global manufacturing. The intricate journey of chip components reflects a supply chain that is deeply interconnected across continents. A single chip can embody the work and resources from multiple countries, emphasizing the impracticality of complete self-sufficiency in any one region.
For instance, a study highlights the extensive travel of chip components, which can cross borders up to 70 times and cover over 25,000 miles before reaching consumers. This global relay is not just about distance; it involves numerous facilities and a multitude of steps. Consider the following data:
- Materials sourced from over 16 countries
- Utilization of at least 5 separate facilities
- Travel exceeding 10,000 miles
- More than 2,000 manufacturing steps
- Approximately 6 months from start to finish
The financial and logistical demands of chip manufacturing encourage a reliance on international partnerships. Building a single facility can cost between $5 billion and $20 billion, which often leads companies to outsource production. The small and lightweight nature of chips further facilitates their global transit. As industry experts assert, the vision of a self-sufficient, localized semiconductor supply chain remains a challenging prospect, with global collaboration being an inevitable aspect of the process.
Conclusion
The journey from quartz sand to the sophisticated silicon chip is a testament to human ingenuity and technological prowess. This article has traversed the complete silicon manufacturing process, revealing the complexity and precision involved in each of the up to 700 steps required to produce a microchip. Over the course of approximately 14 weeks, raw silicon dioxide is transformed through meticulous processes into the integrated circuits that power our modern world. From the creation of pure silicon ingots to the intricate patterning of circuitry, each phase is crucial in ensuring the functionality and reliability of the final product. As we’ve seen, the semiconductor industry relies on a global network of suppliers and highly controlled clean room environments to maintain the high standards necessary for chip production. The result is a marvel of miniaturization that continues to drive technological advancements, making the humble sand beneath our feet a cornerstone of the digital age.
Frequently Asked Questions
What is the starting material for silicon chip manufacturing?
The starting material for silicon chip manufacturing is quartz sand, which is rich in silicon dioxide (SiO2). This sand undergoes a series of chemical reactions to extract and purify silicon to over 99.9% purity.
How long does the process of manufacturing a microchip take?
The process of manufacturing a microchip involves up to 700 processing steps and takes about 14 weeks to complete.
What is the Czochralski process used for in silicon manufacturing?
The Czochralski process is used to grow single-crystal silicon ingots from molten silicon. These ingots are essential for creating silicon wafers with a perfect lattice structure for transistors.
What role does ion implantation play in semiconductor manufacturing?
Ion implantation is utilized to introduce specific atoms into the silicon lattice, altering its conductivity to enable the flow of electricity, which is crucial for the functionality of transistors.
Why is the semiconductor manufacturing process conducted in clean rooms?
The semiconductor manufacturing process occurs in highly controlled clean room environments to ensure minimal impurities, as even microscopic contaminants can interfere with the intricate circuit patterns on silicon wafers.
How does the global supply chain impact semiconductor production?
Semiconductor production relies on a complex global supply chain for raw materials, machinery, and intellectual property, with contributions from dozens of foreign suppliers and factories, which is essential for the creation and distribution of silicon chips worldwide.