The Evolution of Semiconductor Foundry Technology: A Retrospective
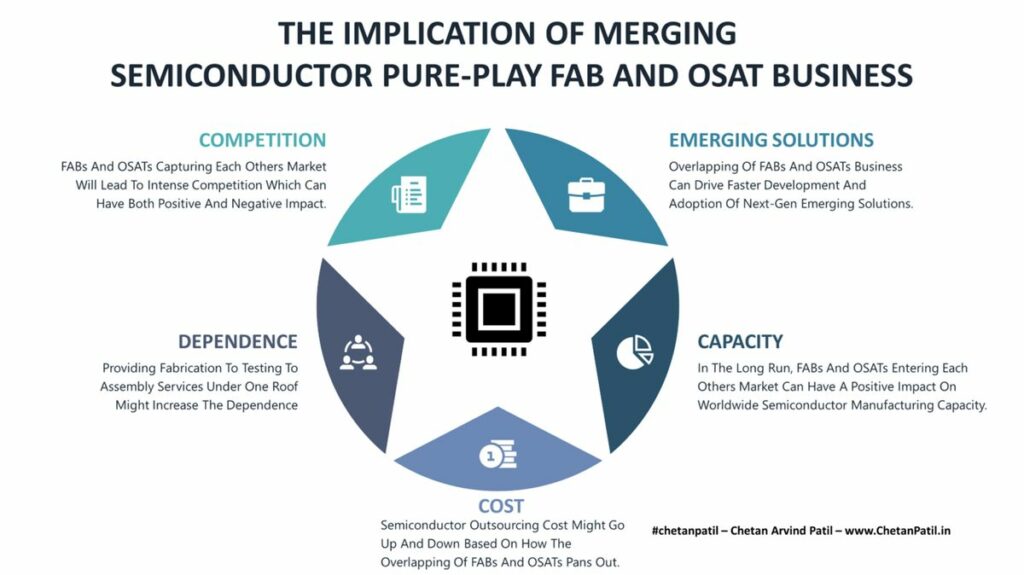
The semiconductor foundry landscape has undergone significant transformations over the years, driven by relentless innovation and the integration of emerging technologies. This article, ‘The Evolution of Semiconductor Foundry Technology: A Retrospective,’ delves into the historical milestones and the visionary individuals who have shaped the industry. Through expert insights and strategic developments, we explore how semiconductor manufacturing has evolved and what the future holds for this vital sector.
Key Takeaways
- The semiconductor foundry industry has witnessed a remarkable evolution, driven by pioneers like Mark Camenzind and Allen Rasafar, who have emphasized the importance of workplace culture and yield management, respectively.
- Software advancements have played a crucial role in foundry progress, with industry experts like Peter Bennet and Ron Lavallee discussing the significant costs associated with software changes, and Alex Peterson heralding the EDA 4.0 era.
- Emerging technologies such as EUV lithography, AI, and 3D structures are reshaping foundries, posing new challenges and opportunities for silicon wafer production, safety standards, and inspection methods.
- Strategic insights from leaders like Allen Rasafar and Dr. Dev Gupta highlight the learning opportunities between different sectors such as data center chipmakers and automotive, as well as the importance of chiplet IP standards.
- Security and reliability have become paramount in semiconductor manufacturing, with industry figures like Valerio Del Vecchio and David Leary emphasizing the integration of security in chip design and the need for improved reliability.
The Pioneers of Semiconductor Foundry Innovation
Mark Camenzind on Why IC Industry Is Great Place To Work
Mark Camenzind’s insights into the integrated circuit (IC) industry highlight a vibrant and dynamic field that offers a wealth of opportunities for professionals. The semiconductor sector is not just about the technology; it’s about the people who drive innovation forward.
The IC industry is characterized by its fast-paced environment and cutting-edge developments. Employees in this sector are constantly learning and growing, as they work on the forefront of technological advancements. The industry’s commitment to pushing boundaries ensures that no two days are the same, providing an exciting and fulfilling work experience.
- Innovation and Collaboration: The heart of the IC industry’s appeal.
- Career Growth: Opportunities abound for personal and professional development.
- Cutting-edge Technology: Employees work with the latest advancements.
- Dynamic Environment: The industry’s fast pace keeps work engaging.
Camenzind emphasizes that the industry’s drive for excellence is matched by its nurturing of talent, making it an ideal place for ambitious individuals looking to make a mark in the tech world.
Allen Rasafar on Managing Yield With EUV Lithography And Stochastics
In the intricate dance of semiconductor manufacturing, Extreme Ultraviolet (EUV) lithography has emerged as a pivotal technology for pushing the boundaries of what’s possible. Allen Rasafar, a notable figure in the field, sheds light on the complexities of managing yield in the era of EUV. Yield management, particularly with EUV, involves a delicate balance between the physics of light and the unpredictable nature of stochastics.
The introduction of EUV lithography has necessitated a reevaluation of existing computational models. As the industry moves towards High-NA EUV systems, the imperative for advanced computational lithography becomes clear. This shift is not just about embracing new equipment but also about adapting to the nuanced interplay of light and matter at these smaller scales. The table below highlights the contrast between traditional lithography and EUV:
Feature | Traditional Lithography | EUV Lithography |
---|---|---|
Light Source | Deep Ultraviolet (DUV) | Extreme Ultraviolet (EUV) |
Wavelength | 193 nm | 13.5 nm |
Resolution | Limited by light wavelength | Enhanced by shorter wavelength |
Mask Complexity | Less complex | More complex due to mask absorbers |
Rasafar’s insights point to a future where engineering expertise and artificial intelligence converge to optimize yields. This convergence is crucial for managing the stochastics inherent in EUV processes, which can lead to variations that impact the final product’s performance and reliability.
Art Scott on Rethinking Engineering Education In The U.S.
The semiconductor industry is facing a pivotal moment in its evolution, and with it, the need for a reimagined approach to engineering education becomes critical. Art Scott and other industry experts are advocating for a curriculum that is more aligned with the dynamic needs of semiconductor foundries. This includes a greater emphasis on practical skills, interdisciplinary learning, and the integration of AI/ML technologies into the educational framework.
To address these needs, several key changes have been proposed:
- Updating course content to include cutting-edge topics such as EUV lithography, advanced metrology, and the challenges of AI/ML integration.
- Enhancing industry-academia collaboration to ensure that the skills taught are directly applicable to the challenges faced in semiconductor manufacturing.
- Fostering a culture of continuous learning where engineers are encouraged to stay abreast of technological advancements and industry trends.
These changes are not just about keeping pace with technology; they are about ensuring that the U.S. remains at the forefront of semiconductor innovation. As the industry evolves, so too must the educational institutions that fuel its workforce.
The Intersection of Software and Foundry Progress
Peter Bennet and Ron Lavallee on The True Cost Of Software Changes
In the dynamic landscape of semiconductor foundries, software changes are a double-edged sword. The cost of software modifications extends beyond the immediate financial outlay, impacting production timelines and yield rates. Software is integral to every stage of semiconductor manufacturing, from design to testing, and changes can introduce unforeseen complications.
The following table outlines the primary areas affected by software changes in the foundry process:
Area Impacted | Short-term Effects | Long-term Consequences |
---|---|---|
Design | Increased design time | Potential for improved efficiency |
Fabrication | Adjustment period for new processes | Enhanced precision and yield |
Testing | Additional testing phases | Higher reliability and lower defect rates |
Maintenance | Immediate increase in support calls | Reduced downtime with stable releases |
It’s crucial for industry professionals to weigh these factors carefully. A hasty software update might promise immediate improvements but could lead to significant disruptions. Conversely, well-planned and executed changes, although costly at first, can pave the way for advancements in efficiency and quality that benefit the foundry in the long run.
Alex Peterson on Welcome To EDA 4.0 And The AI-Driven Revolution
The advent of EDA 4.0 marks a transformative era where artificial intelligence (AI) is becoming a cornerstone of electronic design automation. Alex Peterson’s insights into this revolution underscore the necessity for the industry to embrace AI to stay competitive. The integration of AI into EDA tools is not just an incremental improvement; it’s a paradigm shift that promises to enhance efficiency, accuracy, and innovation in chip design.
As we prepare for an AI-driven future in chips, it’s crucial to understand the implications of this shift. AI algorithms can analyze vast amounts of data to optimize design processes, predict outcomes, and even suggest design improvements. This leads to a significant reduction in time-to-market and opens up new possibilities for complex chip designs that were previously unattainable.
However, the transition to AI-driven EDA tools also presents challenges. The industry must ensure that the workforce is equipped with the necessary skills to leverage these new technologies. Moreover, there must be a concerted effort to maintain the balance between AI assistance and engineering expertise to achieve the best results.
Paul Clifton on Week In Review: Semiconductor Manufacturing, Test
In a week that encapsulated the dynamism of the semiconductor manufacturing and testing landscape, Paul Clifton provided a comprehensive review that industry professionals should not miss. The week’s highlights underscored the critical balance between innovation and reliability in the sector.
Key developments included advancements in testing protocols and the integration of AI into manufacturing processes. These strides are not just technical achievements but also pivotal moments that could redefine industry standards:
- Enhanced testing protocols for next-gen chips
- AI integration in defect detection
- Progress in yield management strategies
Clifton’s insights also touched upon the importance of collaboration across various segments of the industry to foster a more robust and efficient manufacturing ecosystem. As we look forward to the next wave of technological breakthroughs, it’s clear that the lessons from this week will be instrumental in shaping the future of semiconductor foundries.
Emerging Technologies Shaping the Future of Foundries
CdrFrancis Leo on Will There Be Enough Silicon Wafers?
The semiconductor industry stands at a crossroads, with the demand for silicon wafers surging as technology advances. CdrFrancis Leo raises a critical question: will the supply keep up? The answer hinges on several factors, including the expansion of manufacturing capabilities and the development of alternative materials.
To ensure a steady supply, the industry is exploring various avenues:
- Investing in new foundries to increase production capacity.
- Diversifying sources of raw materials to mitigate risks.
- Advancing material science to find substitutes for traditional silicon when possible.
These efforts are crucial for maintaining the momentum of technological progress. Moreover, attracting a domestic workforce for the chip industry, particularly in STEM subjects, is essential for sustaining growth and innovation.
Riccardo Vincelli on How Safe Is Safe Enough?
In the relentless pursuit of semiconductor innovation, safety remains a paramount concern. Riccardo Vincelli raises critical questions about the adequacy of current safety standards in the face of ever-increasing complexity and integration levels. As devices shrink and performance expectations soar, the industry must reassess its safety protocols to ensure they evolve in tandem with technological advancements.
Vincelli’s insights prompt a reevaluation of safety margins, highlighting the need for a dynamic approach to safety that can adapt to the rapid pace of semiconductor development. The following points outline key considerations for enhancing safety in semiconductor manufacturing:
- The integration of more robust safety checks throughout the design and manufacturing process.
- A shift towards predictive safety models that can anticipate potential failure points before they occur.
- Collaboration across the industry to establish universal safety standards that reflect the latest technological capabilities.
The dialogue on safety is not just about preventing immediate hazards; it’s about building a foundation of trust and reliability that will carry the semiconductor industry into the future.
Jem on 3D Structures Challenge Wire Bond Inspection
The advent of 3D structures in semiconductor manufacturing has introduced new complexities in the inspection and metrology of advanced packages. As devices shrink and packaging becomes more intricate, traditional wire bond inspection methods are being pushed to their limits. Experts at the table, including Jem, have discussed the challenges of inspecting and measuring smaller features across large areas with high precision.
To address these challenges, a multi-faceted approach is necessary, encompassing advancements in both hardware and software. The following points outline key areas of focus:
- Development of high-resolution imaging systems.
- Implementation of sophisticated algorithms for feature detection.
- Integration of AI and machine learning for improved defect recognition.
- Adoption of new metrology techniques for accurate 3D measurements.
These initiatives are critical for maintaining yield and reliability in the face of ever-decreasing feature sizes and the increasing complexity of semiconductor packages.
Strategic Insights on Semiconductor Manufacturing
Allen Rasafar on What Data Center Chipmakers Can Learn From Automotive
The automotive industry has long been a pioneer in adopting new technologies to enhance performance and reliability. Data center chipmakers are now looking to the automotive sector for insights on managing complex systems and ensuring robustness. Key lessons include the rigorous testing protocols and the integration of advanced safety features, which are critical in automotive but equally applicable to the high-uptime requirements of data centers.
One area of particular interest is the use of chiplets, which has been instrumental in automotive to achieve modularity and scalability. Jerry Magera highlights the importance of chiplets in automotive, suggesting that similar approaches could benefit data center chips by allowing for more flexible and efficient designs.
To further illustrate the potential crossover benefits, consider the following points:
- Emphasis on early STEM education can cultivate a future workforce adept in both automotive and semiconductor technologies.
- Community outreach and partnerships, as noted by Liz Allan, are essential in driving interest in STEM and chip-related careers.
- The adoption of hybrid bonding techniques can enhance interconnectivity, a method already gaining traction in automotive applications.
By embracing these strategies, data center chipmakers can not only improve their products but also contribute to a more sustainable and innovative industry ecosystem.
Christopher Wendt on The Race Toward Mixed-Foundry Chiplets
The semiconductor industry is witnessing a paradigm shift with the advent of mixed-foundry chiplets, which promises to revolutionize chip design and manufacturing. Christopher Wendt highlights the urgency and potential of this approach, emphasizing the need for collaboration across different foundries to make heterogeneous integration a reality.
The benefits of mixed-foundry chiplets are numerous, including increased design flexibility, cost savings, and faster time-to-market. However, the path to widespread adoption is fraught with challenges such as standardization and intellectual property concerns. Below is a list of key considerations for the successful implementation of mixed-foundry chiplets:
- Establishing universal standards for interoperability
- Ensuring robust IP protection mechanisms
- Fostering partnerships between foundries
- Developing advanced packaging techniques
As the industry races to leverage the advantages of chiplets, it’s clear that a collective effort is required to overcome the technical and logistical hurdles. Wendt’s insights serve as a call to action for stakeholders to align their efforts and push the boundaries of semiconductor innovation.
Dr. Dev Gupta on Chiplet IP Standards Are Just The Beginning
As Dr. Dev Gupta highlights, the establishment of chiplet IP standards marks only the beginning of a transformative journey in semiconductor design and manufacturing. The seamless integration of multi-die systems within a package is becoming increasingly crucial, especially with the rise of artificial general intelligence applications demanding customized chiplets. The path forward includes not only the development of data and protocol interoperability standards for EDA tools but also overcoming numerous technical hurdles.
The table below outlines some of the key challenges and considerations for advancing chiplet IP standards:
Challenge | Consideration |
---|---|
Interoperability | Ensuring compatibility across diverse EDA tools and systems |
Customization | Tailoring chiplets to specific AI and other advanced application needs |
Connectivity | Adopting universal connectors like UCIe for efficient data flows |
Thermal Management | Addressing heat dissipation in densely packed multi-die configurations |
The discourse on chiplet IP standards is evolving, with industry experts like Frank Schirrmeister of Arteris contributing valuable insights into the state of progress towards an open chiplet ecosystem. The vision of a modular approach to system design, where components can be seamlessly connected, is driving innovation and collaboration across the semiconductor industry.
The Evolving Landscape of Semiconductor Security and Reliability
Valerio Del Vecchio on Security Becoming Core Part Of Chip Design — Finally
The semiconductor industry is reaching a consensus that security can no longer be an afterthought in chip design. Valerio Del Vecchio emphasizes the need for a foundational approach to security, integrating it into the hardware layer to complement software defenses. This shift is driven by the increasing complexity of attacks and the recognition that robust security is a critical feature for modern electronics.
While many chip manufacturers may consider implementing agile security in software, Del Vecchio suggests that a hybrid solution, where hardware and software work together, is essential for long-lasting protection. This approach ensures that security measures are not only reactive but also proactive, anticipating potential threats and mitigating them before they can cause harm.
The following points highlight the key aspects of incorporating security into chip design:
- Establishing a secure hardware root of trust
- Designing for resistance to physical tampering
- Implementing encryption and secure boot processes
- Ensuring secure communication protocols
- Regularly updating security measures to keep pace with evolving threats
David Leary on Improving Reliability In Chips
In the quest for ever-more capable electronics, reliability has become a cornerstone of semiconductor design. David Leary emphasizes the critical nature of this aspect, particularly as chips find their way into safety-critical applications. Enhancing reliability involves a multifaceted approach, addressing everything from the architecture to the materials used.
Key strategies for improving chip reliability include rigorous testing protocols, advanced error correction techniques, and the implementation of redundancy where necessary. Below is a list of considerations that Leary suggests are paramount in the pursuit of reliability:
- Comprehensive failure analysis and stress testing
- Adoption of error-correcting code (ECC) memory
- Design for manufacturability to minimize defects
- System-level checks to anticipate and mitigate failures
Leary’s insights resonate with the industry’s broader concerns, as highlighted in a recent article titled ‘Memory’s Future Hinges On Reliability – Semiconductor Engineering’. The article underscores the importance of proper architecture enhancements and parallelization to bolster memory reliability.
Ann Mutschler and Kevin Parmenter on The Threat Of Supply Chain Insecurity
In the intricate web of semiconductor manufacturing, supply chain insecurity poses a significant threat to the industry’s stability and reliability. Ann Mutschler, a seasoned author at Semiconductor Engineering, emphasizes the growing concerns around security issues and requirements in commercial applications. Kevin Parmenter echoes these sentiments, highlighting the vulnerabilities that companies face in an interconnected global market.
The semiconductor supply chain is a complex network of suppliers, manufacturers, and distributors. Any disruption can lead to cascading effects that compromise the integrity of the entire system. To mitigate these risks, experts suggest a multi-faceted approach:
- Rigorous vetting of suppliers and subcontractors
- Implementation of robust cybersecurity measures
- Adoption of industry-wide standards and best practices
- Continuous monitoring and assessment of supply chain health
As the industry moves forward, it is imperative that these strategies are not only discussed but actively integrated into the operational frameworks of semiconductor companies. The goal is to ensure that the supply chain becomes a fortified backbone, resilient against the myriad of threats it faces in the modern era.
Conclusion
The retrospective journey through the evolution of semiconductor foundry technology has been a testament to the industry’s relentless pursuit of innovation and excellence. From the early days of simple integrated circuits to the complex landscape of AI-driven EDA, EUV lithography, and hybrid bonding, the foundry sector has continuously adapted to meet the ever-increasing demands of the digital age. The insights from industry experts underscore the challenges and triumphs faced along the way, highlighting the critical role of collaboration, education, and strategic foresight in shaping the future. As we look ahead, it is clear that the semiconductor foundry industry will remain at the forefront of technological advancement, driving progress across all sectors and powering the next wave of breakthroughs in computing and communication.
Frequently Asked Questions
How has the semiconductor foundry technology evolved over the years?
Semiconductor foundry technology has evolved significantly, moving from simple transistor fabrication to complex integrated circuits with billions of transistors. Advances include the transition from micron-scale to nanometer-scale processes, the adoption of Extreme Ultraviolet (EUV) lithography, the development of 3D stacking techniques, and the integration of AI and machine learning for process optimization.
What are the challenges of managing yield with EUV lithography and stochastics?
EUV lithography presents challenges such as pattern complexity, mask defects, and stochastic effects due to the reduced wavelength of EUV light. These can lead to variability in the printed features, impacting yield. Foundries must employ advanced inspection techniques, process controls, and computational modeling to manage these challenges.
In what ways is the intersection of software and foundry progress important?
The intersection of software and foundry progress is crucial for optimizing manufacturing processes, improving design efficiency, and enabling the creation of more complex chips. Software advancements in Electronic Design Automation (EDA) and AI-driven tools are key to handling the increasing complexity of semiconductor design and production.
What emerging technologies are shaping the future of semiconductor foundries?
Emerging technologies shaping the future of foundries include advanced materials like silicon carbide, new transistor architectures, 3D stacking, chiplets, and heterogeneous integration. Additionally, the push for more sustainable and secure supply chains is influencing foundry strategies.
How are semiconductor security and reliability evolving?
Security and reliability in semiconductors are evolving through the adoption of secure design practices, hardware-based security features, and improved testing and validation methods. Reliability is being addressed by advanced packaging techniques, robust design margins, and real-time monitoring of chip performance.
Why is engineering education important for the future of the semiconductor industry?
Engineering education is vital for the future of the semiconductor industry as it prepares the next generation of engineers with the skills and knowledge required to innovate and keep pace with rapidly advancing technologies. It also ensures a steady supply of talent to address the complex challenges faced by the industry.