The Future of Wafer Production: Trends and Innovations
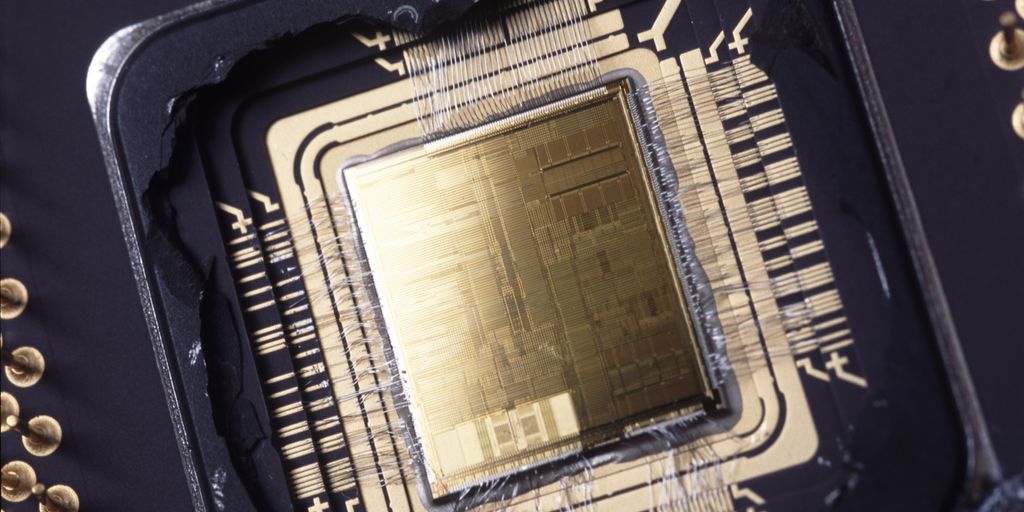
The world of wafer production is changing fast, and new trends and ideas are leading the way. From making bigger wafers to using new materials, these changes are making the semiconductor industry better and more advanced. This article will look at these exciting trends and what they mean for the future.
Key Takeaways
- Bigger wafers help make more chips at once, saving time and money.
- Better surface quality means chips work better and last longer.
- New ways to grow crystals are making wafer production faster and better.
- Using materials other than silicon could make even better chips.
- Nanotechnology and automation are making wafer production more precise and efficient.
Increasing Wafer Diameter
In the ever-changing world of silicon wafer manufacturing, one of the biggest trends is the move towards larger wafer sizes. This shift is driven by the need to produce more chips from a single wafer, which boosts production efficiency and cuts costs. Techcet, previously forecasting a 6% increase for silicon wafers in 2024, is now seeing a hurdle to growth.
Advantages of Larger Wafers
Larger wafers, like those 300mm and beyond, offer several benefits. They allow for more devices to be made on a single wafer, which means higher productivity and better device yield. This leads to lower material costs and higher throughput, making semiconductor technology more accessible and driving further innovation.
Challenges in Scaling Up
Scaling up to larger wafer sizes isn’t without its challenges. Manufacturers face technical hurdles, such as ensuring uniformity and quality across the larger surface area. Additionally, the transition requires significant investment in new equipment and processes, which can be a barrier for some companies.
Impact on Production Costs
Increasing wafer diameter not only enhances production efficiency but also significantly reduces costs. The ability to produce more chips from a single wafer means lower material costs and higher throughput. This cost reduction is crucial for making semiconductor technology more accessible and driving further innovation in the industry.
Improving Surface Quality
Simultaneously, there’s a relentless pursuit of improving surface quality. Achieving near-perfect surface conditions is paramount, as even the smallest defect can impair the performance of a semiconductor device. Innovations in surface treatment processes, including more refined polishing and etching techniques, are driving the production of wafers with unprecedented levels of smoothness and defect-free surfaces, thereby boosting the reliability and performance of semiconductor chips.
New Crystal Growth Methods
The development of new methods of crystal growth is at the forefront of research in the field. Scientists and engineers are constantly exploring innovative techniques to grow silicon crystals more efficiently and with even greater purity. These advancements aim to produce crystals with optimal electrical properties for semiconductor applications, ensuring the continued miniaturization and enhancement of electronic devices.
New techniques such as molecular beam epitaxy and chemical vapor deposition are being used to achieve higher purity and better control in crystal growth. These methods help in producing high-quality wafers that are essential for the performance and reliability of semiconductor devices. The improved control over the growth process also allows for the creation of more complex and efficient semiconductor structures.
Researchers are continually working on refining these methods and developing new ones. For example, a new method for growing molybdenum disulfide on silicon wafers using metalorganic chemical vapor deposition (MOCVD) has shown promising results. This method allows for better material uniformity and faster growth times, making it a significant advancement in the field.
Exploring Alternative Materials
Potential Materials Beyond Silicon
The use of alternative materials is emerging as a pivotal trend. While silicon remains the backbone of the industry, the exploration and integration of new semiconductor materials promise to unlock new capabilities and increase the performance of electronic devices. These materials could offer superior electrical, thermal, or optical properties, opening the door to new technologies and applications previously deemed unattainable.
Advantages and Challenges
Alternative materials offer potential benefits such as higher electron mobility, better thermal conductivity, and the ability to operate at higher frequencies, which can improve overall device performance. However, there are challenges too. For instance, the cost of these materials can be higher, and integrating them with existing silicon-based processes can be complex.
Impact on Device Performance
The integration of these materials with silicon wafers opens up new possibilities for advanced device design and performance. These materials could offer superior electrical, thermal, or optical properties, opening the door to new technologies and applications previously deemed unattainable.
Integration of Nanotechnology
Nanotechnology has emerged as a force in wafer manufacturing, unlocking new possibilities and propelling the industry into a future defined by innovation and excellence. From enhancing collaboration and knowledge exchange to enabling new functionalities, expanding the frontier of materials science, promoting collaboration and knowledge exchange within the semiconductor industry, and driving advancements in manufacturing automation and process control, nanotechnology holds the potential to revolutionize the field.
Automation in Wafer Handling
The adoption of automation in wafer handling is a transformative step for semiconductor manufacturers. It allows for increased productivity, precision, and safety in manufacturing environments. By leveraging modern robotics and automation technology, companies can significantly improve their production capabilities.
Advanced Packaging Techniques
Emerging Packaging Methods
Advanced packaging methods are transforming the semiconductor industry. Techniques like multi-chip modules, 3D ICs, 2.5D ICs, fan-out packaging, and system-in-package (SIP) are becoming more common. These methods allow manufacturers to combine multiple components into a single device, improving signal connections and reducing the distance signals need to travel. This results in faster data transfer and better overall performance.
Benefits for Semiconductor Devices
The benefits of advanced packaging for semiconductor devices are significant. By connecting chips more compactly, manufacturers can achieve faster data transfer rates and improved electrical performance. Additionally, these techniques can lead to better thermal management, which is crucial for maintaining device reliability and longevity. Advanced packaging also allows for the creation of more compact and efficient electronic devices, which is particularly important in the field of microelectronics.
Future Trends and Innovations
Looking ahead, the future of advanced packaging techniques is promising. Innovations such as wafer-level packaging (WLP) are expected to become more prevalent. WLP integrates packaging and interconnects directly at the wafer level, eliminating the need for traditional packaging processes. This approach offers several benefits, including a reduced form factor and enhanced thermal management. As technology continues to evolve, we can expect to see even more innovative packaging solutions that will further enhance the performance and efficiency of semiconductor devices.
Conclusion
In summary, the future of wafer production is bright and full of promise. With ongoing advancements in technology, such as larger wafer sizes, better surface quality, and new materials, the industry is set to achieve new heights. These innovations will not only make production more efficient but also improve the overall quality of semiconductors. As we look ahead, it’s clear that the continuous evolution and collaboration within the industry will keep pushing the boundaries of what’s possible, ensuring that we stay at the forefront of technological progress.
Frequently Asked Questions
What are the benefits of increasing wafer diameter?
Larger wafers allow more chips to be made from a single wafer, which boosts production efficiency and cuts costs.
Why is surface quality important in wafer production?
Better surface quality helps improve the performance of semiconductor devices by reducing defects and enhancing reliability.
What are some new crystal growth methods being explored?
Innovative techniques like the Czochralski process and molecular beam epitaxy are being studied to improve crystal quality and production speed.
Are there materials other than silicon being used for wafers?
Yes, materials like gallium nitride and silicon carbide are being explored for their potential to offer better performance in certain applications.
How is nanotechnology impacting wafer production?
Nanotechnology allows for greater precision and efficiency in wafer production, leading to smaller and more powerful semiconductor devices.
What role does automation play in wafer handling?
Automation, including AI and IoT-enabled systems, helps increase the precision, scalability, and flexibility of wafer handling processes.