The Importance of Wafer Burn-In in Semiconductor Manufacturing
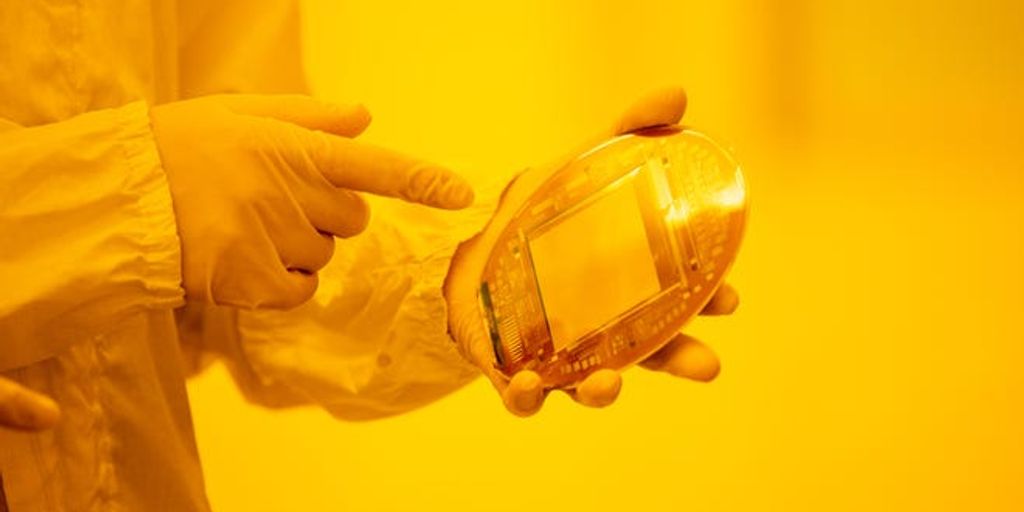
Wafer Burn-In is a crucial step in making semiconductor devices. This process helps catch problems early, ensuring that the final products are reliable and high-quality. By testing at the wafer stage, manufacturers can spot and fix issues before the devices are packaged and shipped. This not only saves money and time but also boosts customer trust in the products.
Key Takeaways
- Wafer Burn-In helps identify defects early, improving the reliability of semiconductor devices.
- This process saves costs by reducing the need for extensive testing after production.
- Wafer Burn-In provides valuable data for better yield analysis and defect understanding.
- Early detection of issues leads to higher customer satisfaction and trust.
- As technology advances, the importance of Wafer Burn-In will continue to grow.
Understanding Wafer Burn-In in Semiconductor Manufacturing
Wafer Level Burn-In (WLBI) is a crucial step in semiconductor manufacturing. It ensures the reliability and performance of semiconductor devices. This process helps manufacturers find and remove early-life failures, improving the overall quality of the final product.
Key Benefits of Wafer Burn-In Testing
Wafer burn-in testing offers several significant advantages in semiconductor manufacturing. By identifying and eliminating defective dies early in the production process, this testing method ensures that only the most reliable components make it to the final product. This not only enhances the overall quality of semiconductor devices but also boosts their performance and longevity.
Enhanced Reliability
Wafer burn-in testing plays a crucial role in improving the reliability of semiconductor products. By catching potential failures early, manufacturers can prevent defective components from reaching the market. This process helps in reducing the chances of device failures in the field, thereby ensuring that the final products are more dependable.
Cost Savings
One of the most compelling benefits of wafer burn-in testing is the significant cost savings it offers. By identifying defects at the wafer level, manufacturers can avoid the expenses associated with packaging and further processing of faulty components. This is especially beneficial for multi-die modules, where even a small percentage of defective dies can lead to substantial cost increases.
Improved Yield Analysis
Wafer burn-in testing also contributes to improved yield analysis. By providing detailed data on the performance and reliability of individual dies, this testing method allows manufacturers to fine-tune their production processes. This leads to higher yields and better overall efficiency in semiconductor manufacturing.
Technical Aspects of Wafer Burn-In
Test Procedures and Protocols
Wafer Burn-In (WBI) involves a series of rigorous tests to find and remove faulty semiconductor devices early in the manufacturing process. The wafers are exposed to high temperatures and electrical stress to speed up potential failure mechanisms. This helps catch defects before the devices are packaged and shipped.
Equipment Used
The implementation of WBI requires advanced equipment, which can be a significant investment for manufacturers. The tools used include temperature chambers, voltage stress testers, and specialized software for monitoring and analysis. These tools are essential for ensuring the reliability and effectiveness of the burn-in process.
Challenges and Solutions
One of the main challenges in WBI is the high cost of the equipment and the complexity of the test procedures. Smaller companies may find it difficult to adopt these tests due to limited resources. However, the benefits of early defect detection and improved yield often outweigh the costs. Solutions include investing in scalable equipment and training staff to handle the sophisticated tools and protocols.
Impact on Product Quality and Market Confidence
Early failure detection is crucial in semiconductor manufacturing. By identifying potential issues before products reach the market, manufacturers can avoid costly repairs and product recalls. This not only saves money but also protects the company’s reputation. Burn-in testing performance results may well be the “permission to play” credential for the markets of tomorrow.
Customer satisfaction is directly linked to the reliability of the products. A high failure rate is unacceptable under any circumstance. Field failures can lead to costly repairs, product recalls, and customer dissatisfaction which will harm both the bottom line and the viability of a manufacturer. By ensuring that products are reliable, manufacturers can build trust with their customers and ensure long-term success.
In the competitive world of semiconductor manufacturing, delivering reliable products is essential. Manufacturers have developed ways to enhance the probability of delivering the highest possible reliability to the end-user. Perhaps the best approach to achieve this goal would be to perform a short but enhanced test case of the device in the actual field stress environment, essentially validating the performance signature of the field conditions. This information is essential for improving overall yield and ensuring the quality of the final products.
Future of Wafer Burn-In Testing
Technological Advancements
The future of wafer burn-in testing is set to be shaped by significant advancements in testing technologies. Smaller geometries and larger die sizes are driving the need for more sophisticated testing methods. These advancements will help in detecting even the smallest defects, ensuring higher reliability of semiconductor devices.
Industry Adoption
The economic considerations of wafer level burn-in tests are substantial. The initial investment in sophisticated equipment and the ongoing costs of maintaining and operating these tools can be high. Balancing cost and reliability is crucial, as manufacturers must ensure that the benefits of early defect detection and improved yield outweigh the expenses.
Potential Challenges
Implementing wafer level burn-in tests requires advanced equipment and tools, which can be a significant investment for manufacturers. The complexity of the test procedures and protocols can pose challenges, especially for smaller companies or those with limited technical expertise. The need for specialized knowledge and equipment can limit the widespread adoption of wafer-level burn-in tests.
Case Studies and Real-World Applications
Success Stories
One notable case study on a semiconductor manufacturing company is ABCTronics. They take their process and wafer health-related issues very seriously. By implementing wafer burn-in testing, they saw a significant reduction in early failures, which boosted their product reliability and customer trust.
Lessons Learned
From various case studies, it’s clear that early detection of defects is crucial. Companies have learned that investing in robust wafer burn-in testing can prevent costly recalls and enhance overall product quality. This proactive approach not only saves money but also strengthens market position.
Best Practices
- Regular Testing: Consistently perform wafer burn-in tests to catch potential issues early.
- Data Analysis: Use the data from these tests to improve manufacturing processes.
- Customer Feedback: Incorporate feedback to refine testing protocols and ensure product reliability.
By following these best practices, companies can ensure their products meet high standards and maintain customer satisfaction.
Conclusion
In summary, Wafer Level Burn-In (WLBI) testing is a key part of making semiconductors. By finding and fixing problems early, WLBI helps ensure that only the best and most reliable products reach customers. This not only saves money by cutting down on the need for more tests later but also makes the final products work better. As technology keeps getting better, the role of WLBI testing will become even more important, helping to keep up the high standards of semiconductor devices.
Frequently Asked Questions
What is Wafer Burn-In Testing?
Wafer Burn-In Testing is a process used in making semiconductors. It helps find and fix problems in the wafers before they are cut into individual chips. This makes sure the final products are reliable and work well.
Why is Wafer Burn-In Testing important?
This testing is important because it catches defects early. By finding problems at the wafer stage, manufacturers can ensure fewer faulty products reach customers. This saves money and time.
How does Wafer Burn-In Testing improve product reliability?
By identifying and fixing defects early, Wafer Burn-In Testing makes sure that only the most reliable products make it to the market. This boosts the overall quality and reliability of the final products.
What are the benefits of Wafer Burn-In Testing?
The benefits include enhanced reliability, cost savings, and better yield analysis. It helps manufacturers find issues early, saving money and improving the quality of the final product.
What challenges are faced during Wafer Burn-In Testing?
Some challenges include the need for specialized equipment and the risk of over-stressing the wafers. However, these can be managed with proper protocols and procedures.
What is the future of Wafer Burn-In Testing?
The future looks promising with technological advancements and wider industry adoption. However, there may be challenges like keeping up with new technologies and ensuring cost-effectiveness.