The Importance of Wafer Burn-In Testing in Semiconductor Manufacturing
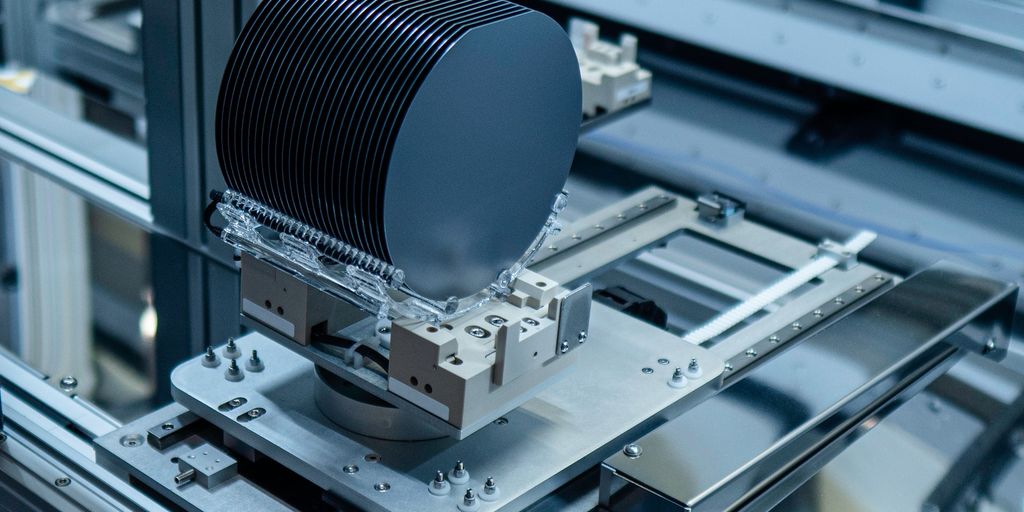
Wafer-level test and burn-in is a critical procedure in the semiconductor industry, ensuring the reliability and quality of semiconductor devices. These processes are essential for detecting and correcting potential flaws and malfunctions early in the manufacturing process before packaging and delivery to customers. By conducting these tests at the wafer stage, manufacturers can identify and resolve issues promptly, minimizing the chances of defective devices entering the market.
Key Takeaways
- Wafer burn-in testing is crucial for identifying latent defects early in the manufacturing process.
- This testing procedure helps in reducing early failure rates of semiconductor devices.
- Burn-in testing provides statistical confidence in the reliability and quality of the manufactured products.
- Technological advancements are making wafer-level burn-in testing increasingly important for mobile and handheld devices.
- Effective thermal management and voltage stress application are key technical aspects of successful wafer burn-in testing.
Understanding Wafer Burn-In Testing
Definition and Purpose
Wafer burn-in testing is a critical procedure in the semiconductor industry, ensuring the reliability and quality of semiconductor devices. By conducting these tests at the wafer stage, manufacturers can identify and resolve issues promptly, minimizing the chances of defective devices entering the market. This process involves subjecting the wafers to electrical stress and elevated temperatures to detect and correct potential flaws and malfunctions early in the manufacturing process.
Historical Context
Historically, burn-in testing was primarily performed at the package level after the wafer die had been assembled into packages. However, with the increasing demand for mobile and handheld devices, wafer-level burn-in has gained importance. This shift allows for earlier detection of defects, improving overall manufacturing efficiency and product reliability.
Key Benefits
The key benefits of wafer burn-in testing include:
- Early Detection of Defects: Identifies potential issues before the packaging stage, reducing the risk of defective devices reaching customers.
- Improved Reliability: Enhances the overall reliability of semiconductor devices by weeding out early failures.
- Cost Efficiency: Reduces costs associated with post-packaging failures and returns.
- Process Control: Provides historical confidence in process control and the ability to monitor and benchmark process or technology changes.
By incorporating wafer burn-in testing, manufacturers can deliver a statistically more reliable product population to the market, ensuring higher customer satisfaction and trust.
The Role of Wafer Burn-In in Quality Assurance
Wafer burn-in testing is a critical procedure in the semiconductor industry, ensuring the reliability and quality of semiconductor devices. These processes are essential for detecting and correcting potential flaws and malfunctions early in the manufacturing process before packaging and delivery to customers. By conducting these tests at the wafer stage, manufacturers can identify and resolve issues promptly, minimizing the chances of defective devices entering the market.
Technical Aspects of Wafer Burn-In Testing
Voltage Stress Application
Voltage stress application is a fundamental aspect of wafer burn-in testing. This process involves applying higher-than-normal voltages to the semiconductor devices to accelerate the aging process and identify potential defects. By conducting these tests at the wafer stage, manufacturers can detect and correct flaws early, ensuring the reliability and quality of the devices.
Thermal Cycling
Thermal cycling is another critical component of wafer burn-in testing. This technique subjects the wafers to repeated cycles of high and low temperatures to simulate the thermal stresses that the devices will encounter during their operational life. The goal is to identify any latent defects that could lead to failure under normal operating conditions.
Monitoring and Data Collection
Effective monitoring and data collection are essential for successful wafer burn-in testing. Advanced systems are used to continuously monitor the performance of the devices under test, collecting data on various parameters such as voltage, current, and temperature. This data is then analyzed to identify any anomalies or trends that could indicate potential issues. Burn-in testing remains one of the keystones for providing statistically driven confidence in semiconductor manufacturing.
Comparing Wafer-Level and Package-Level Burn-In
Process Differences
Wafer-level burn-in (WLB) and package-level burn-in (PLB) are two distinct approaches in semiconductor testing. WLB involves testing the semiconductor devices at the wafer stage before they are diced and packaged, while PLB tests the devices after they have been assembled into their final packages. This fundamental difference impacts the testing process, equipment used, and the types of defects that can be detected.
Advantages of Wafer-Level Burn-In
- Early Detection of Defects: By conducting tests at the wafer stage, manufacturers can identify and resolve issues promptly, minimizing the chances of defective devices entering the market.
- Cost Efficiency: Testing at the wafer level can be more cost-effective as it reduces the need for packaging defective dies.
- Time Savings: WLB can streamline the manufacturing process by catching defects early, thus reducing the time spent on rework and repairs.
Use Cases for Each Method
- Wafer-Level Burn-In: Ideal for high-volume production and applications where early defect detection is critical, such as mobile and handheld devices.
- Package-Level Burn-In: Suitable for detecting defects introduced during the assembly process and for products where final package testing is essential.
Aspect | Wafer-Level Burn-In | Package-Level Burn-In |
---|---|---|
Stage of Testing | Before dicing and packaging | After assembly into final packages |
Cost Efficiency | Higher | Lower |
Defect Detection | Early-stage defects | Assembly-related defects |
Ideal For | High-volume, mobile devices | Final product quality assurance |
Challenges and Solutions in Wafer Burn-In Testing
One of the primary challenges in wafer burn-in testing is managing the high power output required during the process. High power levels can lead to overheating and potential damage to the wafers. To address this, manufacturers often employ advanced cooling systems and power management techniques. These solutions help in maintaining the integrity of the wafers while ensuring effective stress application.
Thermal management is crucial in wafer burn-in testing as it directly impacts the reliability of the test results. Inadequate thermal management can result in uneven heating, leading to inaccurate test outcomes. Solutions include the use of thermal interface materials, optimized heat sinks, and precise temperature control systems. These measures ensure that the wafers are uniformly heated, providing consistent and reliable test results.
Consistency in test results is vital for the credibility of wafer burn-in testing. Variations in test conditions can lead to discrepancies in the data, undermining the reliability of the process. To ensure consistent results, manufacturers implement standardized testing protocols, regular calibration of equipment, and rigorous quality control measures. These practices help in maintaining the accuracy and reliability of the burn-in tests, ensuring that only high-quality semiconductor devices reach the market.
Future Trends in Wafer Burn-In Testing
Technological Advancements
The semiconductor industry is witnessing rapid technological advancements that are reshaping wafer burn-in testing. Emerging technologies such as AI and machine learning are being integrated to enhance the accuracy and efficiency of these tests. These innovations are expected to significantly reduce the time and cost associated with wafer-level test and burn-in.
Impact on Mobile and Handheld Devices
Wafer-level burn-in is becoming increasingly important for mobile and handheld end applications. As these devices demand higher reliability and performance, manufacturers are focusing on improving burn-in processes to meet these requirements. This shift is driven by the need to detect and correct potential flaws early in the manufacturing process, ensuring that only high-quality devices reach the market.
Predicted Industry Shifts
The industry is expected to see significant growth in the adoption of wafer-level burn-in testing. Our discussions with customers indicate that the key markets Aehr is addressing for semiconductor wafer-level test & burn-in have significant growth potential. This trend is likely to continue as manufacturers seek to enhance the reliability and quality of their semiconductor devices.
Conclusion
In conclusion, wafer burn-in testing plays a pivotal role in the semiconductor manufacturing process. By identifying and addressing potential defects early in the production cycle, manufacturers can ensure the reliability and quality of semiconductor devices before they reach the market. This not only minimizes the risk of defective products but also enhances customer confidence in the reliability of the devices. As the industry continues to evolve, the importance of burn-in testing remains undiminished, serving as a cornerstone for quality assurance and process control. Ultimately, the rigorous application of wafer burn-in testing contributes significantly to the advancement and trustworthiness of semiconductor technology.
Frequently Asked Questions
What is wafer burn-in testing?
Wafer burn-in testing is a process used in semiconductor manufacturing to detect and correct potential flaws and malfunctions in semiconductor devices early in the manufacturing process. It involves subjecting the wafer to voltage stress and thermal cycling to identify latent defects.
Why is wafer burn-in testing important?
Wafer burn-in testing is crucial for ensuring the reliability and quality of semiconductor devices. By identifying and resolving issues at the wafer stage, manufacturers can minimize the chances of defective devices entering the market, thereby enhancing product reliability and customer confidence.
What are the key benefits of wafer burn-in testing?
The key benefits of wafer burn-in testing include detecting latent defects, reducing early failure rates, and enhancing the overall reliability of semiconductor devices. This process helps in providing statistically driven confidence in the manufacturing process and assures customers of the product’s reliability.
How does wafer burn-in testing help in quality assurance?
Wafer burn-in testing helps in quality assurance by detecting and discarding defective components before they reach the market or are assembled. It allows manufacturers to monitor and benchmark process or technology changes, ensuring consistent quality and reliability of the final products.
What is the difference between wafer-level and package-level burn-in testing?
Wafer-level burn-in testing is conducted on the wafer before it is diced into individual chips, while package-level burn-in testing is performed after the chips are packaged. Wafer-level burn-in is beneficial for early detection of defects, whereas package-level burn-in is useful for identifying defects that may arise during packaging.
What challenges are associated with wafer burn-in testing?
Challenges in wafer burn-in testing include managing high power output, addressing thermal management, and ensuring consistent results. As semiconductor devices move to higher power outputs, enhanced features in socket and burn-in systems are required to manage target die temperatures effectively.