The Importance of Wafer Electrical Test in Semiconductor Manufacturing
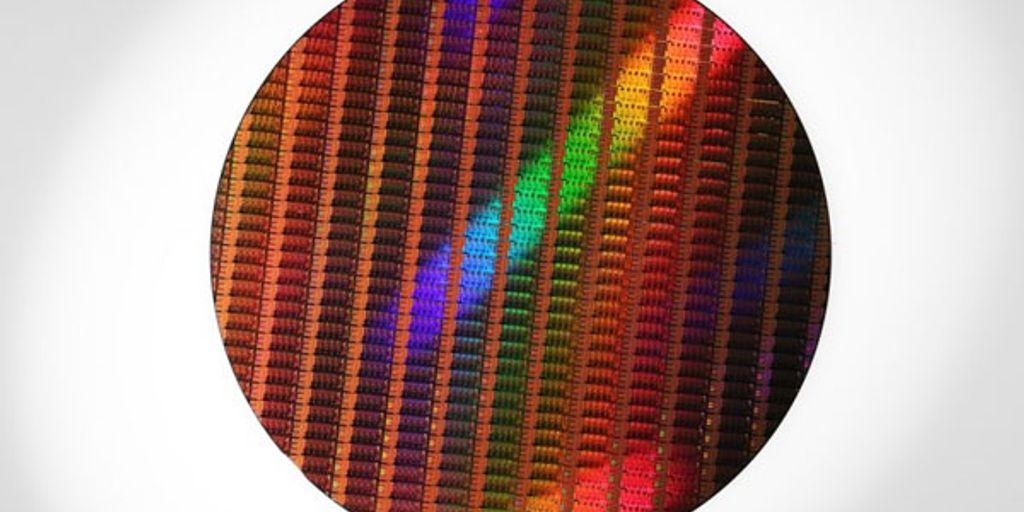
The importance of best practices in wafer electrical testing cannot be overstated for the semiconductor industry. High-quality wafer testing ensures the reliability and performance of semiconductor devices, which are integral to almost every modern technology. Additionally, wafer test analysis, a critical component of this process, involves evaluation and data interpretation to ensure each semiconductor meets the highest standards of quality and functionality, further solidifying the industry’s commitment to excellence.
Key Takeaways
- High-quality wafer electrical testing is critical for ensuring the reliability and performance of semiconductor devices.
- Best practices in wafer testing help minimize defects and optimize test conditions, thereby enhancing overall quality.
- Wafer probing techniques, including contact and non-contact methods, play a crucial role in accurate electrical testing.
- Advanced data analysis tools and regular maintenance of testing equipment are essential for consistent and reliable results.
- Future trends like automation, AI integration, and enhanced data analytics are set to revolutionize wafer electrical testing.
Best Practices in Wafer Electrical Testing
The importance of best practices in wafer testing cannot be overstated for the semiconductor industry. High-quality wafer testing ensures the reliability and performance of semiconductor devices, which are integral to almost every modern technology. Additionally, wafer test analysis, a critical component of this process, involves evaluation and data interpretation to ensure each semiconductor meets the highest standards of quality and functionality.
Ensuring Accuracy and Precision
In wafer test analysis, a blend of precision and attention to detail is vital. From selecting the right materials to designing wafers that accurately replicate production models, every step is crucial. Employing various testing methods like electrical testing for device functionality, Scanning Electron Microscopy (SEM) provides detailed imaging of wafer surfaces, and Focused Ion Beam (FIB) techniques are used for precise material manipulation and analysis.
Minimizing Defects
Each type of test wafer, be it a monitor, dummy, defect, or short loop, plays a distinct role in maintaining high standards in semiconductor testing. These wafers, along with the use of wafer probers and comprehensive chip and die tests, contribute significantly to the production of reliable and high-quality semiconductor products.
Optimizing Test Conditions
After the initial wafer fabrication process is completed, semiconductor chips are subjected to electrical die sorting tests. This process begins with basic electrical tests, with important measured values including DC voltage and the operating parameters of individual chip components (i.e., resistors, capacitors, transistors, and diodes). A wafer-level test and burn-in (WLTBI) are also essential steps in ensuring the long-term reliability of semiconductor devices.
Role of Wafer Electrical Test in Quality Control
Wafer inspection is essential for ensuring that semiconductor devices are reliable and perform consistently across various applications. The quality control processes employed during manufacturing, such as thorough wafer checks, are fundamental to guaranteeing that the wafers are defect-free and meet all specifications. This attention to detail ensures that the final products are less likely to fail, providing reliable safety and sustained performance over time.
Identifying Defective Wafers
Each type of test wafer, be it a monitor, dummy, defect, or short loop, plays a distinct role in maintaining high standards in semiconductor testing. These wafers, along with the use of wafer probers and comprehensive chip and die tests, contribute significantly to the production of reliable and high-quality semiconductor products.
Maintaining Consistency
Wafer testing is a key step in semiconductor manufacturing, verifying the high standards expected in today’s technology. This process checks the quality and performance of wafers, the thin slices of silicon used to make electronic circuits. It’s a complex task that demands careful attention, as even minor errors can have big impacts.
Enhancing Reliability
The importance of best practices in wafer testing cannot be overstated for the semiconductor industry. High-quality wafer testing ensures the reliability and performance of semiconductor devices, which are integral to almost every modern technology. Additionally, wafer test analysis, a critical component of this process, involves evaluation and data interpretation to ensure each semiconductor meets the highest standards of quality and functionality, further solidifying the industry’s commitment to excellence.
Wafer Probing Techniques
Wafer probing is a process in semiconductor development and manufacturing where each die on a wafer is electrically tested. This is performed with an automated wafer probing system. The system holds a wafer on a stable mount and places a set of very thin pins on designated probe pads on the die. These probe pads are also called contact or connection pads, which the wafers connect to with high precision.
Impact of Wafer Electrical Test on Semiconductor Performance
Wafer electrical testing plays a crucial role in enhancing the performance of semiconductor devices. High-quality wafer testing ensures the reliability and performance of semiconductor devices, which are integral to almost every modern technology. This process involves evaluating and interpreting data to ensure each semiconductor meets the highest standards of quality and functionality.
Improving Device Efficiency
Wafer electrical tests help in identifying and rectifying issues that could affect the efficiency of semiconductor devices. By ensuring that each wafer meets the required specifications, manufacturers can produce devices that operate at optimal efficiency.
Reducing Failure Rates
Through comprehensive testing, defects and performance issues can be detected early in the manufacturing process. This proactive approach significantly reduces the failure rates of semiconductor devices, ensuring that only the best products reach the market.
Ensuring Long-Term Stability
Wafer electrical tests also contribute to the long-term stability of semiconductor devices. By identifying potential issues early, manufacturers can make necessary adjustments to enhance the durability and longevity of their products.
Wafer Electrical Test Equipment
Probers and Testers
Wafer probing machines are automatic testing equipment used in the semiconductor manufacturing process to electrically test the integrated circuits of each wafer die. Two probes are used to measure and assess the electrical properties of the transistors, connections, and other circuit components as they move from one integrated circuit to the next. This is the application of the wafer probing system for the electrical testing of wafers on individual chips. A wafer probe loads and accurately positions the wafer on a round plate called a wafer chuck. The wafers are subsequently moved into electrical contact with a collection of tiny needles called a probe card. The devices on a wafer receive test signals transmitted from this measuring instrument and send them back.
Data Analysis Tools
Data analysis tools are essential for interpreting the vast amounts of data generated during wafer electrical testing. These tools help in identifying patterns, anomalies, and trends that can indicate potential issues or areas for improvement. Advanced software solutions can provide real-time analytics, enabling quick decision-making and enhancing overall test efficiency.
Maintenance and Calibration
Regular maintenance and calibration of wafer electrical test equipment are crucial for ensuring accurate and reliable test results. This includes routine checks, cleaning, and calibration of probes and sensors. Proper maintenance helps in minimizing downtime and extending the lifespan of the equipment. Calibration ensures that the measurements taken are precise and consistent, which is vital for maintaining the quality and reliability of semiconductor devices.
Challenges in Wafer Electrical Testing
Handling Miniaturization
As semiconductor devices continue to shrink, handling miniaturization becomes increasingly challenging. The smaller the components, the more difficult it is to ensure accurate and reliable testing. This requires advanced equipment and techniques to maintain precision.
Dealing with Complex Architectures
Modern semiconductor devices often feature complex architectures that can complicate the testing process. These intricate designs necessitate sophisticated testing methods to accurately assess functionality and performance. Engineers must stay updated with the latest advancements to effectively manage these complexities.
Overcoming Environmental Factors
Environmental factors such as temperature, humidity, and electromagnetic interference can significantly impact wafer electrical testing. To mitigate these effects, testing environments must be carefully controlled. This often involves the use of specialized chambers and equipment to maintain stable conditions, ensuring consistent and reliable test results.
Future Trends in Wafer Electrical Testing
The future of wafer testing in the semiconductor sector is poised for innovative developments, notably through nanotechnology, for more accurate 3D integration testing for improved chip functionality with reduced size.
Conclusion
In conclusion, the importance of wafer electrical testing in semiconductor manufacturing cannot be overstated. This critical process ensures the reliability, performance, and quality of semiconductor devices, which are foundational to modern technology. By adhering to best practices in wafer testing and analysis, manufacturers can identify and mitigate defects early, ensuring that each semiconductor meets stringent industry standards. This not only enhances product quality and cost efficiency but also bolsters customer confidence and market reputation. As technology continues to advance, the role of wafer electrical testing will become increasingly vital in maintaining the high standards required for cutting-edge semiconductor products.
Frequently Asked Questions
What is wafer electrical testing?
Wafer electrical testing is a process used in semiconductor manufacturing to verify the quality and performance of wafers by checking for defects and ensuring they meet specified standards.
Why is wafer electrical testing important in semiconductor manufacturing?
Wafer electrical testing is crucial because it ensures the reliability and performance of semiconductor devices, which are integral to almost every modern technology. It helps in identifying defective wafers, maintaining consistency, and enhancing reliability.
What are the best practices in wafer electrical testing?
Best practices in wafer electrical testing include ensuring accuracy and precision, minimizing defects, and optimizing test conditions. These practices help in producing high-quality semiconductor products.
What types of probing techniques are used in wafer electrical testing?
The main types of probing techniques used in wafer electrical testing are contact probing, non-contact probing, and advanced probing methods. Each technique has its own advantages and is selected based on the specific requirements of the test.
How does wafer electrical testing impact semiconductor performance?
Wafer electrical testing improves semiconductor performance by ensuring device efficiency, reducing failure rates, and ensuring long-term stability. This leads to reliable and high-quality semiconductor products.
What challenges are faced in wafer electrical testing?
Some of the challenges in wafer electrical testing include handling miniaturization, dealing with complex architectures, and overcoming environmental factors. Addressing these challenges is essential for accurate and effective testing.