Understanding the Intricacies of Silicon Wafer Production
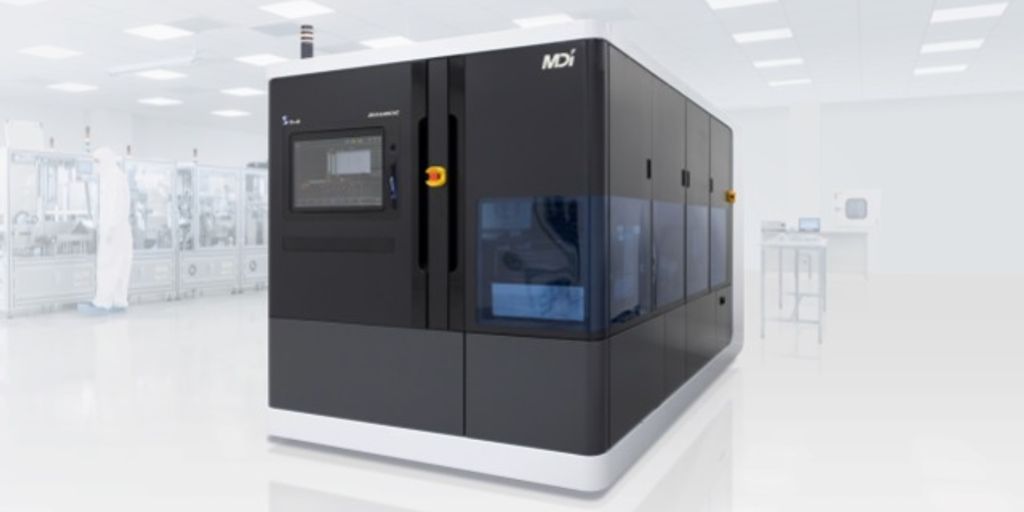
Silicon wafers are the backbone of modern electronics, found in everything from computers to solar panels. Making these wafers is a detailed process that starts with raw materials and ends with a finished product ready for high-tech applications. This article will walk you through each step of the production process, helping you understand the complexity and precision involved.
Key Takeaways
- Silicon wafers are essential for modern electronics, including computers and solar panels.
- The production process starts with raw silicon and involves several steps like purification and crystal growth.
- Different methods, such as the Czochralski method and the Float Zone process, are used to grow silicon crystals.
- Quality control is crucial at every stage to ensure the wafers meet the high standards needed for electronic devices.
- Photolithography and layer deposition are key techniques used to create the intricate patterns on silicon wafers.
The Raw Materials for Silicon Wafer Production
Sources of Silicon
Silicon wafers begin their journey from raw materials like quartzite or sand. These materials are rich in silicon dioxide, which is the primary source of silicon. High-purity silicon is crucial for the production of effective semiconductor devices. The extraction process involves mining these materials and then transporting them to processing facilities.
Purification Processes
Once the raw silicon is extracted, it undergoes stringent purification processes to remove impurities. The most common method is the Siemens process, which involves converting silicon into a gas and then back into a solid to achieve high purity levels. Another method is the use of chemical reactions to eliminate unwanted elements. These purification steps are vital to ensure the silicon meets the quality standards required for semiconductor manufacturing.
Quality Control Measures
Quality control is an essential part of silicon wafer production. Various tests are conducted to ensure the silicon’s purity and suitability for use in electronic devices. These tests include chemical analysis, physical inspections, and electrical property evaluations. By maintaining strict quality control measures, manufacturers can produce silicon wafers that meet the high standards of the technology industry.
Crystal Growth Techniques
Czochralski Method
The Czochralski method involves melting polycrystalline silicon and carefully cooling it to form a large cylindrical ingot. This process requires precise temperature control and slow cooling rates to avoid crystal defects. The ingot is then sliced into thin wafers using a diamond-tipped saw.
Float Zone Process
In the Float Zone process, a rod of polycrystalline silicon is passed through a heating coil, melting a small region. This molten zone is moved along the rod, purifying the silicon as it solidifies. This method produces high-purity silicon with fewer impurities compared to the Czochralski method.
Advantages and Disadvantages
-
Czochralski Method: Advantages
- Can produce large-diameter wafers
- Well-established and widely used
-
Czochralski Method: Disadvantages
- Higher impurity levels
- More expensive due to the need for precise temperature control
-
Float Zone Process: Advantages
- Produces high-purity silicon
- Fewer impurities and defects
-
Float Zone Process: Disadvantages
- Limited to smaller diameter wafers
- More complex and less common
Wafer Slicing and Polishing
After the silicon ingots have been created, they undergo slicing and polishing to transform them into usable wafers. The ingots are sliced into thin circular disks, with the thickness carefully controlled based on the desired specifications. This process is achieved using advanced cutting techniques, such as wire sawing or diamond blade cutting. Following the slicing, the wafers undergo a polishing stage to remove any imperfections and achieve the required smoothness and flatness.
Photolithography in Silicon Wafer Production
Photolithography is a crucial step in making silicon wafers. It helps create the tiny patterns needed for electronic devices. This process uses light-sensitive materials to form these patterns on the wafer’s surface. The steps involved are precise and must be done carefully to ensure quality.
Mask Creation
The first step in photolithography is creating a mask. This mask has the pattern that will be transferred onto the silicon wafer. The mask is placed over the wafer, and light is shined through it. The light only passes through the parts of the mask that are clear, creating a pattern on the wafer.
Light Exposure
Next, the wafer is exposed to light, usually ultraviolet (UV) light. The light hardens the photoresist where it hits, leaving a pattern. The parts of the photoresist that are not exposed to light stay soft and can be washed away. This step is very important because it defines the layout of the circuits.
Etching Processes
After the light exposure, the wafer goes through etching. In this step, the soft photoresist is washed away, and the hard photoresist stays. The exposed parts of the wafer are then etched away using chemicals. This creates the final pattern on the wafer. There are different types of etching, like wet and dry etching, each with its own advantages.
Photolithography is a detailed process that requires precision. It is essential for making the intricate circuits found in modern electronic devices.
Layer Deposition Methods
Chemical Vapor Deposition
Chemical Vapor Deposition (CVD) is a technique where gases react to form a solid material on the wafer. This method is often used to deposit a thin layer of oxide, which provides insulation and helps to prevent electronic interference. CVD is essential for creating high-quality layers that are uniform and free of defects.
Physical Vapor Deposition
Physical Vapor Deposition (PVD) involves the physical transfer of material from a source to the wafer. This can be done through methods like sputtering or evaporation. PVD is commonly used to deposit metals and other conductive materials. The process is crucial for building the complex structures necessary for semiconductor functionality.
Epitaxial Growth
Epitaxial growth is a process where a crystalline layer is grown on a substrate wafer. This method is used to create layers with specific electrical properties. The precise control of layer thickness is crucial, as it impacts the wafer’s electrical properties and overall performance. Understanding these processes and the resulting material properties is essential for optimizing the performance of the final semiconductor devices.
Quality Assurance and Testing
Defect Inspection
Each silicon wafer undergoes a thorough inspection to identify any defects. Advanced microscopy techniques are used to spot even the tiniest imperfections. This ensures that each batch meets the stringent quality standards necessary for reliable performance in electronic devices.
Electrical Testing
Electrical testing is crucial for maintaining the quality and performance of silicon wafers. Various tests are conducted to check the electrical properties and functionality of the wafers. This step helps in identifying any issues that could affect the wafer’s performance in real-world applications.
Thermal Properties Analysis
Thermal properties analysis is another important aspect of quality assurance. This involves testing the wafers to ensure they can withstand the thermal stresses they will encounter during use. By analyzing these properties, manufacturers can guarantee the reliability and durability of the wafers.
Applications of Silicon Wafers
Silicon wafers are the foundation of the modern semiconductor industry and the basis for chips in all electronic applications. Their unique electrical and thermal properties, coupled with high purity, make them essential for the production of semiconductor devices. These thin, circular slices of silicon serve as the foundation for the manufacturing of integrated circuits, microchips, and electronic devices.
Conclusion
Silicon wafer production is a fascinating and complex process that forms the backbone of modern electronics. From the initial stages of cutting silicon crystals to the detailed steps of photolithography and layer deposition, each phase is crucial. Understanding these steps helps us appreciate the precision and technology that go into making the devices we use every day. As technology continues to advance, the methods and techniques in silicon wafer manufacturing will also evolve, ensuring that our electronic devices become even more efficient and powerful.
Frequently Asked Questions
What are silicon wafers used for?
Silicon wafers are used as the base material for making integrated circuits, solar cells, and MEMS devices.
How is silicon purified for wafer production?
Silicon is purified through processes like the Siemens process, which removes impurities to produce high-purity silicon.
What is the Czochralski method?
The Czochralski method is a technique to grow large, single crystals of silicon by pulling a seed crystal from molten silicon.
Why is polishing important in wafer production?
Polishing is crucial to ensure a smooth, flat surface, which is essential for the proper functioning of electronic devices.
What is photolithography?
Photolithography is a process where light is used to transfer a pattern onto a silicon wafer, which is then etched to create circuits.
How are silicon wafers tested for quality?
Silicon wafers undergo defect inspection, electrical testing, and thermal properties analysis to ensure they meet quality standards.