Understanding Wafer Burn-In: A Comprehensive Guide
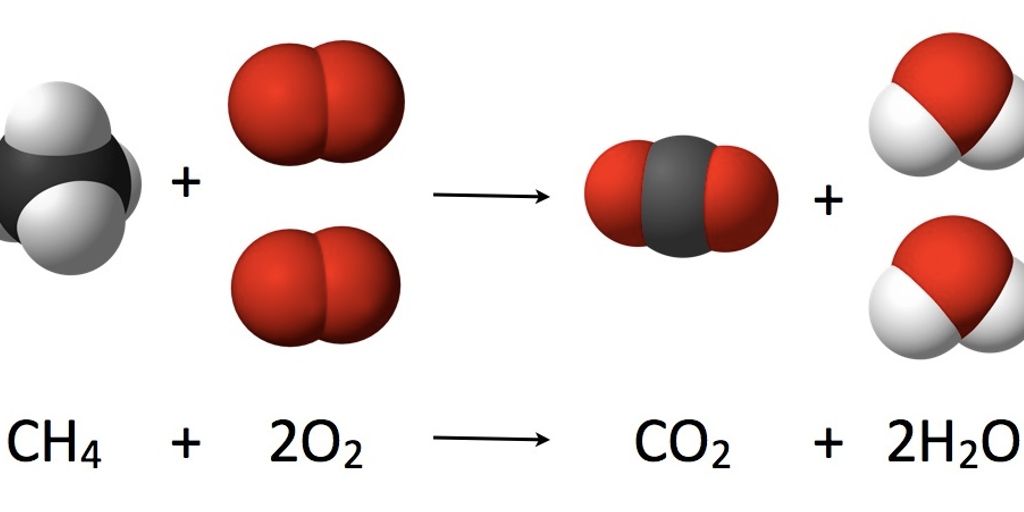
Wafer Burn-In is a vital process in the semiconductor industry. It involves testing semiconductor wafers to find and fix early problems before they become bigger issues. This guide will help you understand what Wafer Burn-In is, why it’s important, and how it can be done effectively.
Key Takeaways
- Wafer Burn-In helps find early problems in semiconductor devices, making them more reliable.
- New technologies are making Wafer Burn-In faster and more efficient.
- Proper planning and best practices are key to successful Wafer Burn-In.
- Using Wafer Burn-In can save money and improve product quality.
- Real-world examples show how effective Wafer Burn-In can be in improving semiconductor manufacturing.
The Fundamentals of Wafer Burn-In
Definition and Importance
Wafer Burn-In (WBI) is a key step in making semiconductors. It involves testing the chips while they are still on the wafer. This helps find and fix problems early. By catching issues at this stage, manufacturers can make sure only the best chips move forward. This makes the final products more reliable.
Technological Advancements
Technology in WBI is always getting better. New tools and methods make the testing faster and more accurate. These advancements help in finding flaws that were hard to detect before. As a result, the overall quality of semiconductor devices improves.
Challenges and Best Practices
Implementing WBI comes with its own set of challenges. These include the need for precise equipment and the ability to handle large volumes of wafers. Best practices involve careful planning and following strict guidelines. This ensures that the process is both effective and efficient.
Implementing Wafer Burn-In in Quality Control
Steps for Effective Implementation
To effectively implement wafer burn-in in quality control, follow these steps:
- Preparation: Ensure all equipment is calibrated and ready for use.
- Loading: Carefully place the wafers into the burn-in chamber.
- Testing: Apply the required stress tests, including elevated temperatures and voltages.
- Monitoring: Continuously monitor the process to detect any anomalies.
- Analysis: After testing, analyze the data to identify any potential issues.
- Reporting: Document the results and take corrective actions if necessary.
Common Pitfalls to Avoid
- Inadequate Calibration: Ensure all equipment is properly calibrated to avoid inaccurate results.
- Overlooking Monitoring: Continuous monitoring is crucial to catch issues early.
- Ignoring Data Analysis: Failing to analyze data can lead to undetected problems.
Best Practices for Success
- Regular Maintenance: Keep all equipment in top condition through regular maintenance.
- Training: Ensure all staff are well-trained in the burn-in process.
- Documentation: Maintain thorough records of all tests and results for future reference.
By following these steps and best practices, companies can significantly improve the reliability and quality of their semiconductor products.
Benefits of Wafer Burn-In
Improved Reliability
Wafer Burn-In (WBI) greatly boosts the reliability of semiconductor devices. By testing integrated circuits while they are still in wafer form, early life failures can be detected and removed. This ensures that only the best chips move forward in the manufacturing process, making the final product more reliable.
Cost Efficiency
WBI helps in cutting down costs by catching defects early. By identifying problems at the wafer stage, manufacturers can avoid the expenses associated with packaging and further testing defective chips. This early detection leads to significant cost savings.
Enhanced Product Yield
WBI also improves the overall yield of semiconductor devices. By ensuring that only known-good chips proceed to the next stages of production, the process enhances the overall yield. This means more functional chips from each wafer, which is beneficial for both manufacturers and customers.
Technological Innovations in Wafer Burn-In
New Techniques and Methods
Recent advancements in wafer burn-in technology have led to more efficient and reliable methods for testing semiconductor devices. One notable technique is the use of conventional wafer probers and multi-chip probe cards. This method eliminates the need for extra specialized equipment, simplifying the process and improving the accuracy of detecting potential failures in random access memories (RAM) before die-sorting.
Impact on Manufacturing
Wafer burn-in optimizes production yield by reducing the number of defective devices that move on to further manufacturing steps. This includes assembly into multi-chip modules and other integrated parts. By catching defects early, manufacturers can save time and resources.
Future Trends
The future of wafer burn-in technology looks promising with continuous improvements on the horizon. Emerging trends include the development of more precise and scalable solutions, as well as the integration of advanced measuring tools and calibration techniques. These innovations aim to further enhance the reliability and efficiency of the burn-in process.
Precision and Scalability in Wafer Burn-In
Achieving High Accuracy
Wafer electrical testing achieves a high level of accuracy by using many precise, calibrated electrical sources and measuring tools for each wafer. This ensures that every device meets the required standards before moving on to the next manufacturing steps. Setting the test standard for tomorrow involves continuous improvements and innovations in testing methods.
Scalable Solutions
Scalability in wafer burn-in is crucial for meeting the demands of large-scale production. In FY24, we shipped our new higher power production system capable of testing and burning in up to 3.5 kW per wafer on the 9 wafer FOX-XP test and burn-in system. This system allows for efficient and effective testing of multiple wafers simultaneously, ensuring that production can keep up with market demands.
Measuring Tools and Calibration
Accurate measuring tools and regular calibration are essential for maintaining the precision of wafer burn-in processes. These tools help in detecting and correcting potential flaws early in the manufacturing process, reducing the number of defective devices that proceed through further manufacturing steps. Regular calibration ensures that the tools remain accurate and reliable, contributing to the overall quality and reliability of the semiconductor products.
Case Studies and Real-World Applications
Industry Examples
In the semiconductor sector, Smiths Interconnect has played a pivotal role. Through real-world examples, we explore how companies have successfully implemented Wafer Level Burn-In (WLBI) to enhance product reliability and yield. One notable success story involves a major semiconductor manufacturer that reduced failure rates by 30% after integrating WLBI into their quality control process.
Lessons Learned
From these case studies, several key lessons emerge:
- The importance of a well-designed testing protocol cannot be overstated.
- The integration of WLBI requires careful planning and execution to avoid potential pitfalls.
- Continuous monitoring and data analysis are crucial for ongoing success.
Success Stories
WLBI is particularly useful in scenarios where high reliability is crucial, such as in aerospace and medical devices. It is also beneficial for application-specific deliverable components, as it can trigger out-of-character performance indicators without weakening properly functioning ones. This makes it an essential part of the quality control plan for many semiconductor manufacturers.
Conclusion
In summary, Wafer Level Burn-In (WLBI) is a key process in making sure semiconductor devices are reliable and high-quality. By testing wafers early, manufacturers can catch problems before they become bigger issues. This not only saves time and money but also makes the final products better. As technology keeps getting better, WLBI will continue to be an important part of making semiconductors. Whether you’re new to this topic or have some experience, understanding WLBI can help you see why it’s so important in the world of electronics.
Frequently Asked Questions
What is wafer burn-in?
Wafer burn-in is a process where semiconductor wafers are tested under extreme conditions to catch early-life failures. This helps improve the reliability and quality of the final products.
Why is wafer burn-in important?
It is important because it helps manufacturers find and fix problems early in the production process, ensuring that only high-quality products reach the customers.
What are the steps to implement wafer burn-in?
To implement wafer burn-in, you need to plan carefully, use the right equipment, follow best practices, and continuously monitor the process to catch any issues early.
What are the benefits of wafer burn-in?
The main benefits include improved reliability, cost savings, and better product yield. It ensures that only the best devices move forward in the production line.
What challenges are involved in wafer burn-in?
Some challenges include the need for specialized equipment, the complexity of the process, and the need for continuous monitoring and adjustments to ensure accuracy.
How has technology improved wafer burn-in?
Technological advancements have made wafer burn-in more effective and efficient by introducing new techniques and better equipment, which help in identifying issues earlier and more accurately.