Maximizing Efficiency in Wafer Fab Operations: Current Trends and Innovative Approaches
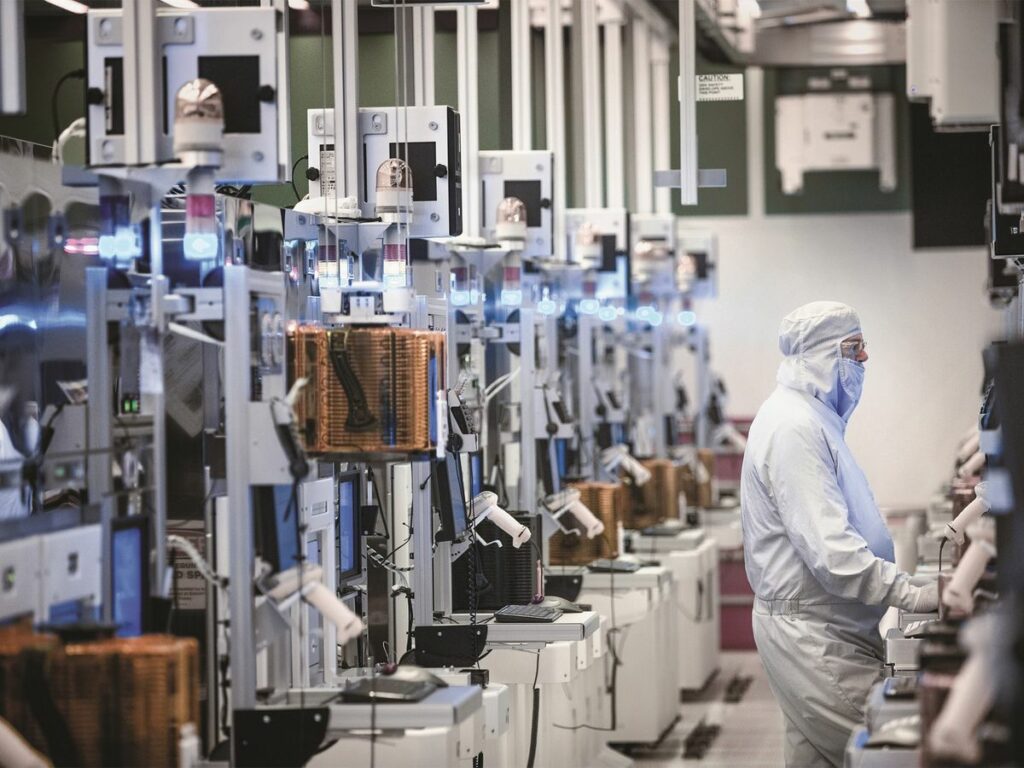
The semiconductor industry is at a pivotal juncture with wafer fab operations seeking to maximize efficiency through cutting-edge trends and innovative approaches. This article will delve into the advancements in wafer fabrication equipment and processes, strategies for enhancing fab yield and reducing costs, as well as the push towards energy efficiency and sustainable manufacturing. Additionally, we will explore the evolution of device structures and the emerging opportunities in memory and heterogeneous integration, all of which are critical for maintaining a competitive edge in the dynamic landscape of semiconductor manufacturing.
Key Takeaways
- Significant revenue growth is expected in wafer fab equipment, especially in mature foundry and specialty markets, driven by investments in regions like China and the adoption of advanced packaging.
- Innovations in substrate patterning and chiplet assembly are essential for overcoming the challenges in >28 nm production technologies and achieving smaller feature sizes and higher assembly reliability.
- The industry is moving towards utilizing lower cost nodes for specific IC functions and mixing pre-designed dies, which can result in new products with reduced design costs and higher fab yields.
- A 1000X improvement in computing energy efficiency is projected, leveraging advancements in materials, process technologies, and sustainable manufacturing practices to meet ambitious environmental goals.
- Transitioning to new device structures like stacked 2D materials and adopting chiplets and heterogeneous integration are key strategies for improving memory performance and cost optimization.
Advancements in Wafer Fabrication Equipment and Processes
Anticipating Revenue Growth in Mature Foundry and Specialty Markets
The semiconductor industry is poised for significant revenue growth, particularly in the mature foundry and specialty markets. The latest TrendForce report reveals a 7.9% jump in 4Q23 revenue for the world’s top ten semiconductor foundries, reaching $30.49 billion. This uptick is a testament to the robust demand and strategic investments in these sectors.
Key factors contributing to this growth include:
- China’s increased investments in mature foundry, specialty markets, and advanced packaging/OSATs.
- Scheduled fab openings that are expected to drive the intake of new wafer fab equipment (WFE) in the 2025 timeframe.
- Continuous investments in current and mature chip companies, ensuring a secure domestic supply of critical chips.
Despite the challenges faced in 2023, companies like TSMC have managed to outperform the industry, thanks in part to the emergence of generative AI-related applications. Looking ahead, TSMC anticipates a healthy growth year in 2024, with revenue growth projected in the low-to-mid 20s percentage range, driven by advancements in 3nm and 5nm technologies, as well as AI applications.
Challenges and Opportunities in >28 nm Production Technologies
The landscape of wafer fabrication for technologies greater than 28 nm is marked by a juxtaposition of challenges and opportunities. Large WFE revenue growth is anticipated, particularly in regions like China that are heavily investing in mature foundry, specialty markets, and advanced packaging/OSATs. However, while some WFE makers are poised to replace international competitors, they face the hurdle of limited production capacities.
Development trends in areas such as 2.5D packaging are pushing the boundaries of packaging area and performance, aiming to deliver cost reductions. Yet, this comes with its own set of challenges, including reticle size limitations, the higher cost of silicon compared to organic and glass, and various device reliability issues. Innovative solutions are being explored, such as transitioning from silicon interposers to silicon bridges and adopting panel-level packaging to enhance cost-effectiveness.
To further improve fab yield and save on costs, there is a significant opportunity to utilize lower cost nodes for specific IC functions. Additionally, the creation of new products by mixing pre-designed dies can lead to savings in design costs. The adoption of high-end performance packaging is also on the rise, reflecting the industry’s push towards more sophisticated and efficient packaging solutions.
Innovations in Substrate Patterning and Chiplet Assembly
The landscape of wafer fabrication is witnessing a transformative shift with the adoption of chiplets and heterogeneous integration. This shift is not only enhancing the functionality of semiconductor devices but also optimizing costs and accelerating time-to-market. The disaggregation of SoC monolithic dies into smaller, function-specific chiplets, followed by their interconnection within the same package, is a prime example of this innovation. The result is a higher yield with more dies per wafer and a finer bump or pad pitch for increased density.
To support these advancements, the industry is focusing on the development of new materials and substrates that serve as the foundation for heterogeneous integration. The CHIPS for America substrates and substrate materials program is a pivotal initiative, aiming to integrate substrate innovations into US manufacturing. The objectives are to accelerate domestic R&D and innovation in advanced packaging materials and substrates. This is crucial for the chiplet ecosystem, as it underpins any implementation of advanced packaging.
Furthermore, equipment, tools, and processes are being adapted to handle the intricacies of patterning substrates and assembling chiplets onto these substrates. The Advanced Packaging Production Facility (APPF) is expected to benefit significantly from these developments, which are essential for achieving reduced patterned feature sizes and reliable chiplet assembly.
Strategies for Enhancing Fab Yield and Reducing Costs
Utilizing Lower Cost Nodes for Specific IC Functions
In the pursuit of cost optimization within wafer fab operations, the strategic use of lower cost nodes for specific integrated circuit (IC) functions has emerged as a compelling approach. By selecting appropriate nodes for less complex or non-performance-critical functions, manufacturers can achieve significant savings in fabrication costs. This method leverages the economic benefits of mature nodes, which often have higher fab yield and lower production expenses compared to their advanced counterparts.
The concept of System in Package (SiP) further exemplifies this trend, where multiple ICs are integrated into a single package. SiP can incorporate chips from different nodes, allowing for a mix of cost and performance that suits the product requirements. This approach not only saves design cost by reusing pre-designed dies but also accelerates time-to-market by simplifying the development process.
The table below outlines the potential benefits of using lower cost nodes for specific IC functions:
Benefit | Description |
---|---|
Fab Yield Increase | Higher yield due to mature node reliability |
Cost Reduction | Lower production costs at mature nodes |
Design Efficiency | Reuse of existing dies reduces design efforts |
Time-to-Market | Faster product development cycles |
As the industry continues to evolve, the adoption of chiplets and heterogeneous integration (HI) will likely enhance these advantages. By partitioning dies, manufacturers can increase the number of dies per wafer, leading to optimized costs and higher density interconnects.
Mixing Pre-designed Dies for New Product Development
The semiconductor industry is increasingly adopting strategies that leverage existing resources to accelerate time-to-market and reduce costs. Mixing pre-designed dies offers a compelling opportunity to create innovative products without the need for extensive new design efforts. By utilizing dies that are already designed and stocked, companies can save significantly on design costs.
The New Advanced Packaging and Multi-chiplet Platform (NAPMP) initiative is focusing on enhancing chiplet discovery methodologies, high-value chiplet designs, and integration techniques. This approach not only streamlines the development process but also promotes higher fab yields, optimizing costs further. The adoption of advanced packaging and heterogeneous integration (HI) is a testament to the industry’s shift towards more efficient manufacturing paradigms.
Here are some key benefits of this approach:
- Higher yield: More dies per wafer and optimized costs due to partitioned die.
- Density: Finer bump or pad pitch allows for higher density integrations.
- Flexibility: Optimization node per chiplet caters to specific IC functions.
- Speed: Faster time-to-market with pre-designed and readily available components.
Adoption of High-End Performance Packaging
The high-end performance packaging market is on a trajectory of significant growth, with projections indicating an increase from $2.21 billion in 2022 to a staggering $16.7 billion by 2028. This surge is largely attributed to the advancements in 3D technology, particularly in the realm of 3D stacking, which is pivotal for the next generation of High Bandwidth Memory (HBM 3+). The race to become the leading service provider in this domain remains open, with numerous potential players vying for the position.
Advanced packaging techniques are revolutionizing the semiconductor industry by blurring the traditional boundaries between a monolithic chip and a packaged assembly of heterogeneous chips. This evolution allows for the integration of a larger number of dies within a single package, addressing critical aspects such as power delivery and thermal dissipation. The shift towards a chiplet-based approach is a key factor in this transformation, enabling more efficient system integration.
Key markets that stand to benefit from these advancements include High-Performance Computing (HPC)/Artificial Intelligence (AI), telecommunications, automotive, and consumer electronics. As the industry moves forward, the focus on system-level integration over single-chip packaging is becoming increasingly pronounced, with heterogeneous integration (HI) playing a central role. This shift is expected to yield systems with lower power consumption, reduced latency, and enhanced bandwidth capabilities.
Energy Efficiency and Sustainable Manufacturing Goals
Achieving a 1000X Improvement in Computing Energy Efficiency
The quest for energy-efficient computing is driving the semiconductor industry towards a monumental goal: achieving a 1000X improvement in computing energy efficiency within the next decade. This ambitious target is underpinned by a multi-faceted approach that includes leveraging domain-specific accelerators, innovative architectures, and advancements in materials and equipment technologies.
Key strategies to reach this efficiency milestone involve:
- Scaling down energy per bit (EPB) by approximately 0.8x annually.
- Increasing the number of transistors per package by 1.4x each year to maintain the exponential growth in compute performance.
- Harnessing the power of accelerated computing to improve data processing costs and speeds, potentially by a factor of 20:1.
These efforts are not only aimed at enhancing performance but also at addressing the widening gap between compute peak performance and memory/interconnect bandwidth, known as the ‘memory wall’. By focusing on on-die transistor and SRAM energy efficiency, and reducing memory access and wire lengths, the industry can make significant strides in reducing overall power consumption. The CHIPS Act R&D programs are set to prioritize these initiatives, ensuring that the pursuit of energy efficiency is aligned with sustainable manufacturing practices.
Developing Capital and Human-Resource Efficient Semiconductor Manufacturing
The semiconductor industry is at a pivotal point where the development of capital and human-resource efficient manufacturing processes is not just a goal, but a necessity. Creating a semiverse digital twin represents a significant leap in achieving this efficiency. By leveraging AI-enabled deep learning and model development, companies can simulate and optimize semiconductor R&D, design, and manufacturing processes before physical prototypes are created.
To further enhance efficiency, the establishment of a chiplets ecosystem and a 3D heterogeneous integration platform is crucial. This approach facilitates chiplet innovation and advanced packaging, which are essential for the next generation of semiconductor manufacturing. The integration of AI-based model development, along with advanced metrology and sensors, will drive the industry towards a more capital and human-resource efficient future.
Advancements in equipment, tools, and processes are also imperative. The industry anticipates that CMOS equipment and processes will evolve to handle a variety of substrates, including dies, wafers, and panels. This evolution is expected to contribute to the reduction of patterned feature sizes and the reliable assembly of chiplets. The goal is to achieve a manufacturing process that is 10X more capital and human-resource efficient, while also striving for net zero emissions and the use of sustainable materials.
Pursuing Net Zero Emissions and Sustainable Material Use
The semiconductor industry is actively working towards achieving net zero emissions, a goal that is not only environmentally imperative but also beneficial for long-term operational sustainability. Key initiatives include the development of next-generation semiconductor manufacturing processes that are significantly more capital and human-resource efficient.
Efforts to support a sustainable domestic capacity for advanced packaging materials and substrate R&D are underway. This includes the translation of innovations into US manufacturing, ensuring that these technologies benefit the economy and national security. The CHIPS Act R&D programs are set to play a pivotal role in this transition, with a focus on prioritizing applications that address grand challenges in sustainability.
To illustrate the commitment to sustainable practices, the following table outlines the objectives set forth for the industry:
Objective | Description |
---|---|
Energy Efficiency | Aim for a 1,000X improvement in computing energy efficiency over the next decade. |
Sustainable Manufacturing | Develop manufacturing processes that minimize waste and use sustainable materials. |
Workforce Development | Promote a skilled and diverse workforce pipeline for a sustainable domestic manufacturing sector. |
These objectives are not only ambitious but also reflect a collective responsibility to integrate environmental considerations into the core of semiconductor manufacturing.
Next-Generation Device Structures and Scaling Innovations
Transition from CFET to Stacked 2D Materials
The semiconductor industry is witnessing a pivotal shift in transistor technology as it transitions from conventional FinFETs to innovative stacked 2D materials. This evolution is driven by the need for further device scaling and enhanced performance. Stacked 2D materials offer the potential for reduced power consumption and increased transistor density, addressing the limitations of current FinFET architectures.
Key challenges in this transition include managing the increased parasitic capacitance that accompanies more three-dimensional structures. To combat these issues, industry experts are exploring various energy reduction strategies, such as geometry optimization and the development of lower dielectric constant (K) materials. The table below summarizes the anticipated benefits and challenges of moving to stacked 2D materials:
Benefit | Challenge |
---|---|
Enhanced transistor density | Increased parasitic capacitance |
Reduced power consumption | Complexity in material integration |
Potential for continued scaling | Need for advanced patterning techniques |
As the industry navigates this complex transition, a multifaceted approach that includes both material innovation and device structure optimization will be crucial for maintaining the momentum of Moore’s Law.
Device Structure Evolution and Scaling Challenges
As semiconductor technology advances, the evolution of device structures presents both challenges and opportunities for scaling. Mixed-dimensional transistors are emerging as a potential solution to the plateau reached in the downscaling of electronic devices. These innovations, moving from CFET to stacked 2D materials, are crucial for continuous scaling, despite the increasing parasitic capacitance ratio in more 3D-like structures.
The transition to new device structures such as forksheet and CEFT is expected to encounter higher capacitance with given effective width (Weff). To combat these challenges, the industry is exploring various energy reduction strategies, including geometry optimization and the innovation of lower K materials. However, the slowing of chip area scaling due to factors like contact poly pitch (CPP) and SRAM area, as well as the reduction in standard cell area mainly driven by cell height reduction, remains a significant hurdle.
The table below summarizes the key challenges and potential solutions in device structure evolution and scaling:
Challenge | Potential Solution |
---|---|
Higher parasitic capacitance | Geometry optimization, lower K materials |
Slowing chip area scaling | Innovations in cell design and materials |
Increased threshold voltage range | Research in low voltage and high reliability operations |
Approaches to Reduce Parasitic Capacitance in New Structures
As semiconductor devices continue to scale down, the challenge of managing parasitic capacitance becomes increasingly critical. Innovative materials and geometries are essential for reducing the effective capacitance in new device structures. The transition to 3D-like structures has inadvertently increased the parasitic capacitance ratio, necessitating novel solutions.
One such solution is geometry optimization, which involves the meticulous design of device features to minimize unwanted capacitive effects. Additionally, the introduction of lower dielectric constant (K) materials can significantly reduce parasitic capacitance. These materials, when integrated into the device architecture, can offer substantial energy savings.
The table below summarizes key approaches and their impact on parasitic capacitance reduction:
Approach | Description | Impact on Parasitic Capacitance |
---|---|---|
Geometry Optimization | Designing device features to minimize capacitive effects | High |
Lower K Material Innovation | Integrating materials with lower dielectric constants | Moderate to High |
While these strategies are promising, they must be balanced with other considerations such as device reliability and manufacturing complexity. The industry continues to explore a range of techniques to address these challenges, with the ultimate goal of achieving more efficient and powerful semiconductor devices.
Emerging Opportunities in Memory and Heterogeneous Integration
Addressing the Memory Wall and Interconnect Bandwidth Gap
The memory wall represents a growing challenge in semiconductor design, where the increase in processor compute density outpaces the rise in memory bandwidth. This discrepancy leads to a bottleneck that hampers overall system performance, particularly in AI-related workloads. To address this, industry leaders are exploring various strategies to bridge the gap.
One approach focuses on enhancing on-die transistor and SRAM energy efficiency, which can directly impact the power consumed by memory components. Additionally, reducing memory access frequency and shortening global or semi-global wire lengths are key tactics in improving energy distribution across different applications and use cases.
Advanced semiconductor packaging trends, such as the use of hybrid bonding and nano Through-Silicon Vias (nTSVs), are pivotal in advancing heterogeneous integration. These technologies facilitate 3D stacking, which can potentially match or exceed the energy efficiency of on-die data access. The table below summarizes the expected benefits of these advanced interconnect technologies:
Technology | Benefit |
---|---|
Hybrid Bonding | Enhanced signal integrity and thermal management |
nTSV | Improved power integrity and logic-on-logic integration |
Despite these advancements, challenges remain, particularly in maintaining signal and power integrity within complex 3D structures. As the industry moves forward, the interaction among various roadmaps—transistor, interconnect, memory, advanced packaging, and devices—will be crucial for domain-specific applications.
Energy Efficiency Improvements in Transistor and SRAM Design
The quest for energy efficiency in semiconductor design is a critical challenge, particularly in the realm of transistor and SRAM design. As the gap between peak compute performance and memory/interconnect bandwidth widens, the focus intensifies on reducing power consumption in memory, which often exceeds that of logic components.
Innovations in SRAM design are pivotal for enhancing energy efficiency. Research indicates that new SRAM topologies can lead to significant improvements in power usage. The design of the transistor within the SRAM cell is a key factor in this advancement. By optimizing on-die transistor/SRAM energy efficiency, we can contribute to the overall reduction of energy consumption in computing systems.
To sustain the exponential growth in compute performance, it is essential to increase the number of transistors per package and scale the energy per bit (EPB) effectively. This requires a multifaceted approach, including leveraging domain-specific accelerators, architectural innovations, and advancements in materials and process technologies.
Adoption of Chiplets and Heterogeneous Integration for Cost Optimization
The adoption of chiplets and heterogeneous integration (HI) is revolutionizing the semiconductor industry, enabling more dies per wafer and consequently higher yields. This shift is not only optimizing costs but also facilitating a faster time-to-market for new products. The economics of chiplets suggest that while they may add cost due to the larger total area of silicon required for die-to-die interconnects, they ultimately reduce costs by allowing smaller individual dies to achieve higher fab yields.
In the burgeoning chiplet ecosystem, the development of chiplet discovery methodologies is crucial for ensuring reusability and efficient design. The need for small chiplets with fine connection pitches is clear, as they perform better with reduced distances. Moreover, the ecosystem demands robust standards and infrastructure for warehousing and transporting these delicate components.
Factor | Impact on Cost Optimization |
---|---|
Higher Dies per Wafer | Increases Yield |
Finer Bump/Pad Pitch | Enhances Density |
Optimization Node per Chiplet | Tailors Performance |
As industry experts like Jean-Christophe Eloy and George Orji highlight, the future of semiconductor packaging lies in simplifying and cost-effectively manufacturing complex packages. The disaggregation of SoC monolithic dies into smaller, function-specific chips and their subsequent interconnection within a single package is a testament to the potential of chiplets in driving economic efficiency.
Conclusion
In summary, the wafer fab industry is on the cusp of transformative growth, driven by significant investments in mature foundry, specialty, and advanced packaging sectors. With the advent of innovative technologies for >28 nm production and the potential replacement of international equipment makers, the industry is poised to overcome current limitations in production capacities. Advances in patterning substrates, assembling chiplets, and passivating finer substrates are crucial for achieving reductions in feature sizes and enhancing reliability. The integration of CMOS equipment to handle diverse form factors, coupled with the adoption of high-end performance packaging, presents opportunities to save on both fab and design costs. The push towards computing energy efficiency and sustainable manufacturing, fueled by initiatives like the CHIPS Act, is set to revolutionize the sector with domain-specific accelerators, new materials, and process technologies. Furthermore, the shift towards transistor scaling, increased areal density of chips, and heterogenous integration underscores the industry’s commitment to innovation and efficiency. As we look towards emerging opportunities to address the memory wall and improve energy efficiency, the adoption of chiplets and the optimization of tool productivity will be pivotal in meeting the growing demands of AI and other advanced applications. The future of wafer fab operations is bright, with a clear trajectory towards more efficient, sustainable, and cost-effective manufacturing processes.
Frequently Asked Questions
What are the expected trends in revenue growth for wafer fab equipment?
Significant revenue growth is anticipated in mature foundry, specialty markets, and advanced packaging/OSATs, particularly in areas where China is investing.
What challenges are associated with >28 nm production technologies?
While some wafer fab equipment makers can replace international ones, the production capacities for technologies >28 nm are still limited, presenting a challenge.
How is substrate patterning and chiplet assembly evolving?
Advances are being made to reduce patterned feature sizes on large areas, including through-substrate vias, and to reliably assemble chiplets onto these substrates with effective passivation.
What strategies can enhance fab yield and reduce design costs?
Using lower cost nodes for specific IC functions and mixing pre-designed dies for new product development can save on fab and design costs, respectively.
What are the goals for energy efficiency and sustainability in semiconductor manufacturing?
The industry aims for a 1000X improvement in computing energy efficiency over a decade and to develop semiconductor manufacturing that is significantly more capital and human-resource efficient, with net zero emissions and sustainable material use.
What are the emerging opportunities in memory and heterogeneous integration?
To address the memory wall and interconnect bandwidth gap, there are opportunities in improving on-die transistor/SRAM energy efficiency, reducing memory access, and adopting chiplets and heterogeneous integration for cost optimization.